|

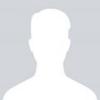
Cracked Gas Compressor Query
#1
Posted 16 December 2019 - 10:06 AM
I m getting that wash water will hv lot of impact on wash oil always ?
#2
Posted 17 December 2019 - 04:28 AM
I don't know what you are doing but I am sure it is wrong.
You can't theoretically calculate the amount of wash oil required.
Wash water is not really wash water. A better name would be quench water.
It is injected at multiple compressor wheels in each casing and by vaporizing it reduces the outlet temperature of each compressor stage so as to reduce the formation of polymers inside the compressor.
#3
Posted 17 December 2019 - 05:59 AM
https://www.exxonmob...wE&gclsrc=aw.ds
Hi,
Let you consider this link and may be consult them together with the compressor manufacturer .
My view
Breizh
Edited by breizh, 21 December 2019 - 07:18 AM.
#4
Posted 17 December 2019 - 10:06 AM
Sir, I agree with you that it is a quench oil and not wash water. I have modelled compressor in Hysys here and tried to find out optimum rate of quench water here. Please help me in this
#5
Posted 17 December 2019 - 10:07 AM
Chemical manufacturer for these products will give thumb rule or best practices like 0.2 percent of cracked gas rate as a standard. But i want to caculate it using simulation here.
#6
Posted 17 December 2019 - 04:45 PM
Have you asked the manufacturer?
As Bobby Strain pointed out in your other post about this subject (https://www.cheresou...r-optimization/), it's unlikely that your simulation will give any meaningful results.
#7
Posted 18 December 2019 - 05:34 AM
Once again: you can't theoretically calculate the optimum wash oil rate using Hysys, or whatever other simulator.
Every CGC will foul. The amount of fouling depends on many factors, such as:
cracking feedstock, design (licensor) of the cracking furnaces, cracking severity, compressor internal design, wash oil properties (aromatics content, boiling range, ....), compressor (outlet) temperature, use of additives, et cetera.
Every ethylene plant has to figure out empirically what works best for them. At the end of the day it is an economical decision.
Quench water can be used to limit the compressor (outlet) temperature. To simulate that accurately you would need to split up each compressor stage into its individual wheels and add some water injection before the inlet of the last wheels. Water injection shall be limited so that all water is vaporized before entering each wheel. You start with injecting water before the last wheel, then before the previous wheel, et cetera, until you obtain the desired compressor stage (casing) outlet temperature. Obviously you can't do this on existing compressor that was not designed for intermediate water injection.
#8
Posted 27 April 2020 - 05:26 AM
Dear Sir,
Thanks for your email
I have tried to do snesitivity analysis of wash water impact on CGC Ethylene Compresor Polytropic Efficiency . and i found that effiency is increasing when water is added from o percent to 2 percent of cracked gas flow here.
Also I want to know what is the exact location wash oil and wash water in CGC? is it at suction or discharge only? IF it is at suction water will be in liquid phase till it reaches discharge line as temp is lesser at suction for water to vaporous here.
Also water addition improves polytrophic effiency of compressor ? also when I calculate polytopic effieincy with formula in hysys, it is coming as 30 percent for H & MB values. why it is so low ?
Regards,
Chetan Chavan
#9
Posted 29 April 2020 - 02:57 AM
Wash oil is injected at compressor suction.
Wash water (quench water) is injected at intermediate points in the compressor casing, as I already explained.
Injecting oil or water at the compressor discharge obviously makes no sense as it has no impact on the compressor. Sometimes it is simulated like that as a simple means to get the streams into the H&M balance, but that does not reflect reality.
The efficiency of the compressor is a function of its wheel design and rotational speed. I don't see how you could detect an improvement in efficiency if water or oil is injected.
Fouling will reduce compressor efficiency, as it makes the wheels less smooth. Wash oil should remove part of that fouling, but there is no way that you can calculate that effect by using a simulator.
It seems to me you are wasting your time using Hysys. Start using your brain.
#10
Posted 01 May 2020 - 01:09 AM
Dear Sir,
Thanks for your reply on this.
Firstly, For simulation purpose, can I consider wash oil and wash water at suction point of compressor? Also as centrifugal compressor is designed for only gas flow and not two phase flow of liquid and gas , injecting wash water will make it two phase flow ? in this case, how compressor tolerates liquid in the compressor casing ?
Secondly, Also want to know if polytropic efficiency of compressor is alone good indicator of fouling as efficiency is a function of temp and pressure ratios and gas composition also. so if anything is changed in feedstocks as a disturbance , then it will change efficiency also. Is it right ?
Wash water is used to reduce discharge temp of gas along with dissolution of any inorganic salts present due to contamination from caustic tower and quench tower also.
Is it correct ? will wash water serve same purpose as that of wash water used in desalter for salts removal ?
What is wash water adjusted polytropic efficiency ? will wash water density impacts overall charged gas gas density and thereby efficiency and composition ?
Regards,
Chetan Chavan
#11
Posted 01 May 2020 - 08:54 AM
The efficiency of the compressor is provided by the vendor in the form of graphs or tables. For each stage it is a function of volumetric throughput and rotational speed.
I am not familiar with Hysys but I would expect that there is a way to input those efficiency data in your model. Read the user manual.
There is no such thing as "wash water adjusted polytropic efficiency".
The quench water merely reduces the outlet temperature. Hysys (or any other simulator) cannot calculate its effect, if any, on efficiency.
To simulate that water injection properly you would need to simulate each wheel in a casing separately. For example: if a stage of your CGC has 8 wheels then you simulate it as 8 compressors in series. Some water is then injected at the outlet of wheel #7 but less than the gas could vaporize to avoid liquid water entering wheel #8. Some water can also be injected at the outlet of wheel #6 but again not too much. See whether the outlet temperature of wheel #8 is now what you want it to be. If it is still too high then also inject water at outlet of wheel #5, et cetera.
Wash oil is just to wash the wheels to remove fouling. There is no real point to include it in the simulation as it is normally not continuous anyway. If you cannot resist to include it just add it at the outlet of the compressor and it will end up in the H&M balance at the correct point.
Again: Hysys (or any other simulator) cannot calculate its effect on efficiency.
Again: stop wasting your time with Hysys. Get the vendor info on efficiency, et cetera.
Try to visualise what happens inside the compressor when water is injected as I described before.
#12
Posted 01 May 2020 - 12:18 PM
Dear Sir,
Thanks for your reply now.
Firstly, I have 5 stage compressor for CGC here. I understand that wash water is injected at compressor casings intermediate points .So do I need to simulate each stage in multiple wheels system ? How do i know how many wheels are there in each stage here?
Secondly, WASH Water is used to remove inorganic salts from Compressor which are deposited due to upstream quench tower contamination right ? Is it called wash water because of that ?
Thirdly, HYSYS has the feature to input those compressor characteristic curves in simulator like flow vs Head and Efficiency vs Flow , power vs Flow for various speeds of compressor here. But in my system , i ma doing like this, I am mixing wash water with cracked gas flow and evaluate temp drop from normal PFD values , then if for this discharge temp and suction conditions, what will be my efficiency ? i am calculating that also.
Also when i mix wash oil and wash water, I am getting two phase flow in compressor suction here also . Do i need to calculate wet efficiency here also? I know reciprocating compressor has oil filled system like in screw compressors here.
Also wash water flow is generally as 0.05 to 1 percent of cracked gas flow generally as per thumb rule in field. Is it wash water to be injected at suction of compressor or condensate free liquid we should get at the outlet of compressor ? Similarly for wash oil also.
Request your valuable guidance on this.
Regards,
Chetan Chavan
#13
Posted 02 May 2020 - 10:11 AM
Chetan,
It seems that you are not reading advise from PingPong properly. I will rehash them:
1. It is not useful to simulate this. However, if you are insistent, simulate each wheel separately. You can get this information from the compressor vendor or as-built information of compressor.
2. Wash water is used only to reduce the compressor discharge temperature. This should help is reducing fouling in the compressor.
3. It is virtually impossible to predict efficient gain due to water injection. To me it seems that what you are trying to do is to match the information from your licensor. Do you know if this is the way your licensor modeled the unit? In reality water is injected inside the casign. It mixes with the gas a quickly vaporizes, thus reducing the temperature. The principal reason to do this is to reduce polymerization by reducing temperature.
4. Your compressor discharge should be free of any liquid. If there is liquid, it means that water is not vaporizing completely and the next wheel would see mixed phase, for which it may not be designed.
Hope this helps,
Abhishek
#14
Posted 03 May 2020 - 04:57 AM
Secondly, WASH Water is used to remove inorganic salts from Compressor which are deposited due to upstream quench tower contamination right ? Is it called wash water because of that ?You are the one calling it wash water, not me.
I have never heard of adding water to the suction of a CGC to remove salts.
If that were necessary one would have to feed a lot of water to the suction as would require them to leave the compressor in liquid water at the discharge. So the water quantity would need to be so high that there is still sufficient water left at the compressor discharge to remove those "salts".
Note that if all water would vaporize inside the compressor and no liquid water was left at the discharge then obviously those "salts" would not leave the compressor but would merely be moved from begin to middle of the compressor.
You better check with the compressor vendor before you try this.
It is still not clear to me whether this topic is about an existing CGC, or whether this is just a purely theoretical discussion.
#15
Posted 03 May 2020 - 09:17 AM
Dear Sir,
Wash water is terminology used in all compressor CGC. If it is purely used to reduce discharge temp, then we do not need it liquid phase at the compressor discharge right. Also as compressor can not stand liquid in suction, then it should be completely vaporizable right ?
#16
Posted 03 May 2020 - 11:45 AM
If it is purely used to reduce discharge temp, then we do not need it liquid phase at the compressor discharge rightRight, but in that case it is better to call it quench water, not wash water.
Also as compressor can not stand liquid in suction, then it should be completely vaporizable right ?You should not inject water in the suction. Not to remove "salts" (which I can't believe are present), and not for any other reason.
If one nevertheless feels the need to inject liquid at the compressor suction then first check with the compressor vendor how much, for what period of time, and at what maximum rotational speed.
In the mean time it is still not clear to me whether this topic is about an existing CGC, or whether this is just a purely theoretical discussion.
#17
Posted 04 May 2020 - 07:23 AM
Dear Sir,
Thanks for your advice on this.
1. If we are injecting wash water in the intermediate points of compressor casing and wheels at ambient temp , when it goes to discharge line, does it need to saturate the vapour stream . Will there be any free liquid present in compressor discharge here? if yes, why we need free water liquid to be present there? How we can theoretically determine saturated condition ?
2. Sir, this topic is about existing CGC only.
3. What is the effect of free water going to aftercoolers ?
Regards,
Chetan Chavan
#18
Posted 04 May 2020 - 03:58 PM
2) Does that existing CGC have water injection nozzles on the compressor casings?
If not, did your company already check with the compressor vendor whether it is possible to install such injection nozzles on the existing casings?
#19
Posted 07 May 2020 - 08:51 AM
Water injections are there at casings at intermediate points.
Secondly, i want to calculate water wash adjusted polytropic effieincy . how to do it ? As only normal effieincy calulctions will depsit very high percent improvement in efficiency , we need to adjust this efficiency value as if there is no wash water additons and ajust this value
Regards,
Chetan Chavan
#20
Posted 07 May 2020 - 09:57 PM
For some compressors, water is injected in the suction and for some, it is injected at intermediate points in the casings specifically return channel of the the impeller. Is it true?
Secondly, we are injecting wash water in the form of free liquid in the suction of compressor, but it is said that water can not be present in centrifugal compressor as it can damage the compressor.
Thanks.
Best Regards,
Chetan Chavan
#21
Posted 08 May 2020 - 05:57 AM
Dear Sir,
I read somewhere that they calculate wash water calculated polytropic efficiency for this system. how to do it ?
I think we need to compensate for wash water addition here
Regards,
Chetan Chavan
#22
Posted 08 May 2020 - 07:48 AM
Secondly, i want to calculate water wash adjusted polytropic effieincy . how to do it ?There is no such thing as "water wash adjusted polytropic efficiency".
The purpose of the injected water is only to cool (quench) the gas inside the compressor so as to reduce fouling of diffusers and impellers due to formation of polymers. The amount of injected water is to be such that it will all vaporize and no liquid is left inside the compressor.
Sometimes an operating company will increase the injected water for a short period of time to remove some polymer fouling by erosion.
The polymer fouling is not water soluble so it is not really washed away.
Before you attempt this you better check first with your compressor vendor whether that is feasible with the selected compressor materials and coatings, as you might otherwise erode the impellers and diffusers.
Secondly, we are injecting wash water in the form of free liquid in the suction of compressor, but it is said that water can not be present in centrifugal compressor as it can damage the compressor.Yes, free liquid can damage the compressor. Check with your compressor vendor how much liquid could be injected in suction, for how long, and at what maximum rotational speed.
I read somewhere that they calculate wash water calculated polytropic efficiency for this system. how to do it ?I don't know what that is supposed to mean.
Injected water vaporizes and lowers the charge gas temperature. As a result the volumetric flowrate of the charge gas will change due to the injection. As a result the operating point could shift a little bit, both on the head curve and on the polytropic efficiency curve. Efficiency could therefor be slightly higher, or slightly lower, when you compare operation with water injection, and without water injection.
The effect of water injection on efficiency is in the long term, not because of the water injection itself but because of less fouling a year later.
#23
Posted 09 May 2020 - 01:32 AM
Dear Sir,
Thanks for your email.
I agree with your point that injected water will reduce gas volumetric flow rate and thereby as per compressor characteristic curves , changing head requirement as well as efficiency of the system as well here.
But in this case of revised operating conditions how to calculate polytropic efficiency revised for this ? As discharge temp of the gas reduces drastically when we add water say 20 deG C , with this dishcrge temp, it will give very high increase in efficiency which is not possible practically of the order of 20 percent improvement. So I could find the term on web of many chemical treatment vendors that water wash polytropic efficiency here. Can you please guide me on this
Regards,
Chetan Chavan
#24
Posted 09 May 2020 - 05:00 AM
But in this case of revised operating conditions how to calculate polytropic efficiency revised for this ?The slight change in volumetric flowrate inside the compressor has only a minor effect on efficiency. You would need to have efficiency curves of each wheel (impeller) in each stage to estimate the impact.
s discharge temp of the gas reduces drastically when we add water say 20 deG C , with this discharge temp, it will give very high increase in efficiency which is not possible practically of the order of 20 percent improvement.I doubt that you can reduce discharge temperature bij 20 oC without getting liquid water inside the compressor.
In any case, how do you get the idea that efficiency would improve by 20 % ?
#25
Posted 11 May 2020 - 03:41 AM
Sir,
we got this from simulation but as a rule of thumb , it is not possible, as max efficiency that can be achieved with this is 5 parent from bas line value and max discharge temp reduction is 15 deG C only. so they talk about wash water adjusted efficiency values here
Regards,
Chetan Chavan
Similar Topics
Psv On Centrifugal Compressor DischargeStarted by Guest_Lyne_* , 10 Jun 2025 |
|
![]() |
||
![]() Lng Boil Off Gas Compressor Suction DrumStarted by Guest_Lyne_* , 04 Jun 2025 |
|
![]() |
||
Parallel Compressor Setup With Uneven CapacitiesStarted by Guest_sinrem_* , 13 May 2025 |
|
![]() |
||
![]() Hysys Expander/compressor Input Using Dimensionless CurveStarted by Guest_Alfreedo_* , 21 Apr 2025 |
|
![]() |
||
Centriugal CompressorStarted by Guest_Rahimzadeh_* , 02 Mar 2025 |
|
![]() |