|

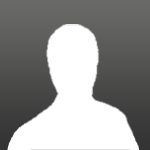
Smr Reformer Flue Gas Flow
#1
Posted 14 February 2025 - 08:05 PM
Recently, a question about our factory has puzzled me a lot. The measured flue gas flow rate of our SMR reformer is significantly higher than the design flow rate(almost 50% higher than design). I use this flow rate to calculate the environmental pollution tax, and this flow rate is directly related to the pressure difference of the SCR catalyst bed (design pressure difference of 1KPa, measured pressure difference of 1.21KPa at 100% load), so we are very concerned about this flue gas flow rate.
The flowmeter is located at a height of 35 meters above the ground on the stack. The flow velocity is measured using a pitot tube, and the flow rate is calculated based on the cross-sectional area before being converted to a dry standard state flow rate.
Below is more information so that you can help me with the analysis:
1. I used Aspen Hysys to calculate the flue gas volume based on the actual fuel gas flow rate, composition, and excess oxygen content. The result is close to but lower than the design flow rate.
2. The instrument man checked the parameter settings of the flue gas flowmeter and it seems that the stack cross-sectional area is set correctly. We also invited a third-party organization to measure the flue gas flow rate, and the results were close to the displayed value of our own flowmeter, We will conduct more checks.
3. The reforming process side: the steam-to-carbon ratio is 3.3 higher than design 3, Is this the cause of the high flue gas flow rate?
My question is, what may be the common reasons for the large amount of flue gas in the reformer ? High steam-to-carbon ratio or leakage of convection coil? Do I need to analyze the composition of the flue gas next? Thank you.
#2
Posted 14 February 2025 - 10:06 PM
#3
Posted 15 February 2025 - 04:20 AM
Hi,
Checking the composition of the flue gas is a good way to find out any leakage in your system.
I suppose you are reporting mass flow (cumulative) to authorities.
How do you calculate this? velocity * area of the cross section of the stack* density of the gas?
This means you need to get access to composition of the flue gas, pressure and temperature to get the density.
This calculation should be integrated over the time to get a cumulative mass.
Please share with us the calculation.
Breizh
#4
Posted 16 February 2025 - 10:42 PM
Hi,
Mass balance with O2 in Flue gas analysis will give you the correct picture.
#5
Posted 24 March 2025 - 03:59 PM
The fact that more flue gas was generated means that more heat exchange occurred in the reformer. If it was generated three times more than the design's expected value, it might be worth reviewing whether there was an issue with the reformer heat exchange calculations. The fact that similar calculation results were obtained in HYsys suggests that the ideal heat exchange equation provides an approximation, but the Tube/Heat Exchanger applied in the actual design might have reflected inappropriate values for heat transfer area or other correction factors.
Similar Topics
![]() Flare Header Reverse FlowStarted by Guest_Ahmadhamzahperta_* , 04 Apr 2025 |
|
![]() |
||
![]() Steam Flow And Heating Time In Batch ReactorStarted by Guest_seagal6_* , 16 Jul 2025 |
|
![]() |
||
![]() Fired Heaters/ Burners/ Flue VelocityStarted by Guest_Lyne_* , 15 Mar 2024 |
|
![]() |
||
Heat Exchanger Steam FlowStarted by Guest_aliebrahem17_* , 25 Nov 2024 |
|
![]() |
||
![]() Flow Through Normally No Flow LineStarted by Guest_iippure_* , 08 Apr 2025 |
|
![]() |