|
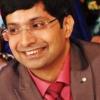
How To Specify Control Valve Pressure Drop Across A Centrifugal Pump
#1
Posted 09 December 2007 - 10:02 AM
accordingly Pump discharge presure is obtained.
According to guidelines 30% of dynamic pressure drop is assumed for maximum flow conditions.
Then how can we specify the Pressure Drop for normal and min flow corresponding to the assumption in maximum flow conditions.
#2
Posted 09 December 2007 - 12:10 PM
What do you mean by the statement “According to guidelines 30% of dynamic pressure drop is assumed for maximum flow conditions”? Where does this guideline come from and what does it apply to? What is meant by “dynamic pressure drop”? Is this the maximum, obtainable pressure drop across the Control Valve (CV) while maintaining a specified flow rate?
The basic operation of a liquid flow CV calls for throttling the fluid - and the greater the throttling, the greater the resulting pressure drop across the valve and the LESS the resulting flow rate through the valve.
You must (or should) know the maximum discharge pressure of your pump at the various discharge flow rates. Here, I have to presume you have a centrifugal pump since you (like many others) fail to state the type of pump. You obtain this value from the field or from the accurate pump performance curve that applies to the pump.
From that value and the value that you also know for the pressure required downstream of the CV, you know the Maximum Pressure Drop obtainable for your pump system. If this is what you call “dynamic pressure drop”, then you can take 30% of this value as that related to the maximum flow you want. However, I don’t know if the final, downstream pressure is the value you need. You have to work towards that final value in a backwards calculation.
You want good CV controllability and response; but you also are bound by the flow characteristics of the centrifugal pump’s performance curve. The curve sets the design criterion for the design of the CV’s flow characteristics in accordance with the downstream requirements.
#3
Posted 11 December 2007 - 12:30 PM
What do you mean by the statement “According to guidelines 30% of dynamic pressure drop is assumed for maximum flow conditions”? Where does this guideline come from and what does it apply to? What is meant by “dynamic pressure drop”? Is this the maximum, obtainable pressure drop across the Control Valve (CV) while maintaining a specified flow rate?
The basic operation of a liquid flow CV calls for throttling the fluid - and the greater the throttling, the greater the resulting pressure drop across the valve and the LESS the resulting flow rate through the valve.
You must (or should) know the maximum discharge pressure of your pump at the various discharge flow rates. Here, I have to presume you have a centrifugal pump since you (like many others) fail to state the type of pump. You obtain this value from the field or from the accurate pump performance curve that applies to the pump.
From that value and the value that you also know for the pressure required downstream of the CV, you know the Maximum Pressure Drop obtainable for your pump system. If this is what you call “dynamic pressure drop”, then you can take 30% of this value as that related to the maximum flow you want. However, I don’t know if the final, downstream pressure is the value you need. You have to work towards that final value in a backwards calculation.
You want good CV controllability and response; but you also are bound by the flow characteristics of the centrifugal pump’s performance curve. The curve sets the design criterion for the design of the CV’s flow characteristics in accordance with the downstream requirements.
Well ! Let me first thank you for sparing precious time on this topic.
Certain things need to be clarified.
1.The Pump is centrifugal as mentioned in the topic (the topic name i have mentioned it to be centrfugal pump)
2.Pump discharge is still to be obtained.I know my suction pressure ,Gravity Head and pressure drops along the instruments/Exchangers in pump circuit.
and Control valve prssure drop is required to have discharge pressure. Acc to guidelines or a euphemism "General Engg Practises" (whichever you like ,i mean that!)
we take a safe value of 25-30% Delta P corresponding to Dynamic Losses at maximum flow .(I dont feel a need to explain whats dynamic losses).
Now the question is how do i know delta p at Normal or minimum flow conditions. (Controller has to kill more pressure because Dynamic Losses will be lesser due to lower velocity )
since pump discharge is not known we can not have any head capacity curve ..so that point is invalid here.
#4
Posted 11 December 2007 - 12:44 PM
With the hydraulics of the system set up (using either your own spreadsheet or some purchased software) and the general pump curve, you do the calculations again but for your other flows (normal and minimum). This time, put in the pump discharge pressure at the reduced flows (from the curve) and the difference in pressure from the pump discharge to the required delivery pressure will be the pressure your control valve station will have to "eat" up. Note that I say "control valve station" because if you have reducers iaround the control valve, their effect enters into the overall control valve calulation.
You record all this on your control valve data sheet and give it to your instrument engineer or go directly to the vendor. They will work out the proper control valve to use.
Once your piping system is actually designed (Isometrics or piping drawings developed) and the actual (but not tested; see below) pump curve is available from the vendor, recheck your calculations to see if you need to make some adjustments in the pump you purchsed before it is actually built and shipped.
Once you've issued a purchase order for a pump, the vendor should be able to give you a curve specifically for that pump and impeller. You can use this for the check calculation. The odds are your calculations are fine and/or the control valve will more than be able to handle any slight deviations determined in the check calculation. The worst case would be a slightly different sized impeller; not the worse thing in the world to have to face.
#5
Posted 28 April 2009 - 10:40 PM
Thank you for the interesting discussion. I do have a question to add on:
Take for example, the pump has a discharge pressure of 15barg, and it is desired to achieve 7barg at the end of the piping to a vessel. This means that the maximum pressure drop through the piping network and control valve is 8barg.
Is there any sort of guidelines / good engineering practice for the pressure loss across the control valve? For example, the control valve should be designed to "eat" 60% of the 8barg (for adequate controlability), and say 20% for friction loss, and the remaining 20% to static loss?
Appreciate your replies.
#6
Posted 29 April 2009 - 01:04 AM
Thank you for the interesting discussion. I do have a question to add on:
Take for example, the pump has a discharge pressure of 15barg, and it is desired to achieve 7barg at the end of the piping to a vessel. This means that the maximum pressure drop through the piping network and control valve is 8barg.
Is there any sort of guidelines / good engineering practice for the pressure loss across the control valve? For example, the control valve should be designed to "eat" 60% of the 8barg (for adequate controlability), and say 20% for friction loss, and the remaining 20% to static loss?
Appreciate your replies.
ALLowed pressure drop across CV= NPSH(available) - NPSH(required)
#7
Posted 29 April 2009 - 11:43 AM
gyan,
I have never heard of this approach and I cannot accept it. As I've stated before, a control valve at the discharge of a centrifugal pump is typically the main control element of the pumped system. It must perform its intended function, which is to allow the desired variability of the flowrate through the system without unduly stressing the system's components. Practically this means that it must be able to move up and down the pump's curve.
#8
Posted 29 April 2009 - 05:58 PM
Gyan,
The control valve would be located downstream of the pump, therefore why would you use NPSH to assign the dP for the control valve?
I dont see the link between these two.
#9
Posted 29 April 2009 - 07:51 PM
My company has a similar preliminary control valve sizing guideline, except it says the control valve should have at least 30% of the frictional pressure drop of the system. Pressure differences due to elevation and velocity are not included.
#10
Posted 07 May 2009 - 01:41 AM
Thank you for the interesting discussion. I do have a question to add on:
Take for example, the pump has a discharge pressure of 15barg, and it is desired to achieve 7barg at the end of the piping to a vessel. This means that the maximum pressure drop through the piping network and control valve is 8barg.
Is there any sort of guidelines / good engineering practice for the pressure loss across the control valve? For example, the control valve should be designed to "eat" 60% of the 8barg (for adequate controlability), and say 20% for friction loss, and the remaining 20% to static loss?
Appreciate your replies.
In my experience, I've encountered these design guidelines:
1. 33% of frictional pressure drop
2. 10% destination pressure
3. 10 psi
Whichever is larger, then that would set the normal CV pressure drop.
This is by no way to be used in general however, this largely depends on the engineering company/clients themselves.
Hope this helps

But from a design standpoint, you have to determine
1. Hydraulic losses from pipes/equipment
2. Operating destination pressure
3. Relative elevations of the pump and the destination
first before you can determine the adequate CV delP. Then using some design guidelines for determination of shutoff head (or using an appropriate pump curve), then you can establish the discharge pressure.
#11
Posted 12 May 2009 - 05:59 PM
thank you for your kind inputs.
I guess I must have got confused with the procedures on how a hydraulics system is designed and set up. From pleckner's post, a control valve's dP is first allocated (eg. design guidelines by Dacs) together with the piping losses, and the pump head required (hence the pump curve is achieved) is determined by back-calculating (adding up) all the pressure losses with the destination's pressure. Therefore, it is impossible to assign say a certain percentage of pressure loss to piping, control valve respectively.
I hope I got it right this time.

#12
Posted 13 May 2009 - 09:12 AM
jerald,
I do think you got it right. As you seem to have realized, the initial design efforts are estimates. You don't really know how much pressure drop your control valve will take until after the pump is purchased and you come to know what the actual pump curve will look like.
#13
Posted 13 May 2009 - 07:28 PM
jerald,
I do think you got it right. As you seem to have realized, the initial design efforts are estimates. You don't really know how much pressure drop your control valve will take until after the pump is purchased and you come to know what the actual pump curve will look like.
Just to reinforce djack77494's reply, these are indeed estimates that are used to choose the right pump. And usually when this is done and the vendor furnishes the pump curve, it's the designer's responsibility to verify if indeed the pump is suitable for the process.
#14
Posted 14 May 2009 - 02:32 PM
Early on the front end process engineer is working in a vacuum. He/she has no clue about the hardware that will be purchased to perform the task required. To adequately handle a wide range of equipment and piping components that may be assembled to do this particular job, he/she adds in some very general allowances. They will normally be suitable for most choices of the actual equipment and piping selections, and allow for small variations that are inevitable during subsequent design and development.
Even later, when we think we know about the small number of candidate pumps that might be selected, we also know of the variations in characteristics among this population (of pumps). Finally we select a pump and impeller. The impeller will not be cut to the exact dimension you expect and it will not perform exactly ass you expect even if it were made precisely. There's a standard that covers this but I don't remember which one. Anyway, you might be surprised to discover the variability in the product that may be delivered and that would be deemed as meeting the specs. It's not as narrow as you might suppose. Allowances are absolutely necessary to deal with these realities.
#15
Posted 09 May 2011 - 12:07 PM
Minimum control valve pressure drop = 69 kPa for single control valve, for X no of control valves in the circuit, it should be 69X kPa.
10% of the discharge vessel operating pressure to take into account any fluctuations in the operating condition of the discharge vessel.
33% of the system frictional pressure drop (system frictional drop refers to the frictional losses through line, instruments and equipments and it excludes static head and control valve pressure drop.
Maximum of these three is taken as control valve pressure drop.
#16
Posted 14 September 2011 - 05:55 PM
#17
Posted 23 September 2011 - 11:31 AM
Β. Nevertheless a few additional notes (assumed to concern globe valves) can be useful for liquid service, when specifying control valves in detail (ΔPs at min, normal, max flow), according to books or engineering practices.
1. Control action is generally satisfactory in the range 10%Cv to 80%Cv, or a bit lower (Cv corresponds to 100% open valve).
2. Check rangeability R= Cv1/Cv2=(Q1/Q2)sqrt(ΔP2/ΔP1), where Q=volumetric flow, 1=max controllable flow conditions, 2=min controllable flow conditions. R should be below 8 depending on valve size and construction. Highest recommended value met in process engineering practice was R=12. If R exceeds this value, address to instrumentation specialists for a solution (apparently most complicated).
3. Above limits on rangeability has been taken from documents of 1970s/80s (Chemical Engineering included), advising to distrust high R values, not being able to be maintained in practice. It is also pointed out that rangeability can have a meaning different to the above. On the other hand modern air conditioning valves can have much higher Rs. Advice on today status of process valve R would be welcomed.
4. I think that short cut rules for control valves (e.g. ΔP rules in the post by Subhendu237) are useful, seeing that (at least here) we do not elaborate a detailed hydraulic analysis (*) in the control system, which is not easy. These rules are applicable in basic engineering, at least for new equipment.
For instance, suppose that an horizontal line develops 3 bar frictional ΔP to the destination tank, and the liquid transfer occurs through a centrifugal pump taking suction from another (atmospheric) tank. An online flow control valve should develop ΔP=33%*3=1 Bar at rated flow (corresponding to, say, Cv=α). The pump should develop 3+1 Barg at discharge (static levels neglected for simplicity).
In detail engineering, selected valve max Cv will be, say, 1.6α. During startup, if flow controller is set to rated flow, valve will close to Cv=α (or to a somehow different Cv, compensating for calculating errors, if any, in ΔPf). Rated flow can be considered as intermediate between max controllable and normal flow, so value of Cv = 0.625maxCv seems acceptable. This check can be done before placing the order for the control valve.
So the conventional procedures / assumptions help for a result during basic engineering and puts engineering activities in a useful sequence. What has serious drawbacks here (in local work place) is the systematic check & revision during detail engineering, according to my understanding.
C. Any comments or opinions on above are gladly welcomed.
Note (*): Mentioned analysis can include control effectiveness and best valve size; checking whether selected components can control in all controllable flow range. Having tried it once, I found it difficult.
ΔP for max, min, normal flow (as suggested by djack77494), or at least at max and min flow, had better be specified in the control valve data sheet.
Edited by kkala, 23 September 2011 - 12:17 PM.
Similar Topics
Hysys Depressuring Utility Pressure QuestionStarted by Guest_cammycheme_* , 15 Aug 2025 |
|
![]() |
||
Positive Displacement PumpStarted by Guest_Selvakannan_* , 31 Jul 2025 |
|
![]() |
||
Automatic Choke ValveStarted by Guest_Mudassssir011_* , 22 Jul 2025 |
|
![]() |
||
![]() Relief Path To Be Considered For Inlet Pressure Drop CalculationStarted by Guest_Ascanio E._* , 09 Jul 2025 |
|
![]() |
||
![]() Valve Cv InputsStarted by Guest_QuantumEng_* , 01 Apr 2024 |
|
![]() |