I would like to ask one student question,
Considering evaporative cooling employed in highly humid area (>85%), I found one reference saying that is possible to combine hot humid air with water and achieve very efficient cooling. This type of "evaporative cooling" is not quite what it suppose to be, meaning that liquid water effluent is very high.
The concept is to spray given (available) amount of liquid water over the tubes and inroduce sufficient air flow (induced draft fans) in order to suppress air outlet temperature to be higher than 70C (environmental reasons). Now, calculating overall heat and material balance, I found that basically everything that happens in this case is sensible heat transfer - air is being enriched with water vapor (this is the only one evaporative cooling that takes place) and liquid water is heated up by 40C, from 30C to 70C. The aim of this concept is to transfer as much heat as possible and to gain heat recovery (water is used as boiler feed water) as much as possible.
I remember from my operations and technical service days, that introducing liquid water over the finned tubes is a disaster: it leads to accelerated corrosion and countless deposits that reduce effective heat transfer. And something that looks attractive in the beginning, very soon turns out to be a disaster. I don't want liquid water on my tubes outter surface, but I don't know how to investigate this further.
Any hints on this?
Thanks in advance,
|
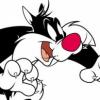
Evaporative Cooling
Started by Zauberberg, Feb 02 2008 10:11 AM
5 replies to this topic
Share this topic:
#1
Posted 02 February 2008 - 10:11 AM
#2
Posted 02 February 2008 - 01:24 PM
Zaub:
I don’t believe that I quite understand the application you are describing. An evaporative cooling system usually involves three (3) fluids:
- The hot process fluid that is desired to be cooled and flows in a “coil” (or a tube bundle) within the bottom section of the evaporative cooler;
- The cooling water that is circulated around the evaporative cooler by a recirculating pump; and,
- The ambient air (preferably cool and dry) that is usually drawn in by an induced draft fan (or a forced draft fan can be used in small applications) and allowed to evaporate a percentage of the water circulated, causing the resulting water flow to adiabatically cool down due to the evaporative mass transfer operation.
In the normal, evaporative process, a constant flow of make-up water is needed in order to maintain the inventory of required circulating cooling water. The water evaporation takes place in mass transfer with the dry air and also as it is allowed to heat up and gain its latent heat of evaporation while in contact with the process fluid coil surface as a water film. If it were not for this latter evaporative effect, the evaporative cooler would be nothing more than another conventional water cooling tower with the exception that it has a process cooling coil inserted in its basin.
What I visualize as the concept that you are studying is that you have a highly humid (>85%), flow of air whose outlet temperature you want to suppress such that it is less than 70 oC (for environmental reasons). Combined with this objective, you would use the resultant, heated water as boiler feedwater and obtain some energy recovery savings (that presumably would be an incentive for the environmental costs). You estimate that the product, exiting hot water is heated up by 40 oC, from 30 oC to 70 oC (basically with a majority of sensible heat transfer).
In your concept, then, I gather that you want to cool down a hot stream of vented, humid air and produce a hot water product at the same time. Am I correct? The part that confuses me is that you mention that “introducing liquid water over the finned tubes is a disaster: it leads to accelerated corrosion and countless deposits that reduce effective heat transfer” --- and you are absolutely correct! However, where does the process coil play a part in your concept? You have not mentioned that you are using a process coil inside the evaporative cooler and what its conditions are. Have I missed something?
I also share your concern for creating a “caliche” mine. I too had a horrendous experience just 2 years out of university. I designed and employed “trombone” type coolers in order to employ a low-cost method to cool down hot MEA solution. I was almost driven to tears when I saw the resultant amount of calcium carbonate deposits growing around and over all of the cooler surfaces on a day-to-day basis. I was using deep-well cooling water on a once-through basis and there was nothing I could do about the net effect – except to change it at the first, immediate turn-around.
Since that time, many years ago, I have used various evaporative coolers – all with success. I have employed both Baltimore Aircoils and Marley evaporative coolers..
http://www.baltimore...tors/index.html
and,
http://www.baltimore...s/AC_index.html
http://spxcooling.co...h-fluid-cooler/
and
http://spxcooling.co.../MHF-TS-06A.pdf
Could you give us some more details and, perhaps, a sketch of the application?
#3
Posted 03 February 2008 - 10:42 AM
Mr Montemayor,
Thank you for your excellent reply and quality links you provided.
I am attaching a scheme of this “evaporative system”, with process heat and material balance data written below.
Process stream is a 3-phase fluid, consisting of hydrocarbon gas, steam, oil and high percentage of liquid water (72% water cut). Total mass flow rate is 311,000 kg/h with pressure set at 2.5barG and temperature of 127C upstream of heat transfer equipment. The aim is to cool this stream down to 60C. Allowable pressure drop for heat transfer utilization is 1bar.
For cooling purposes, 368,000 kg/h of boiler feed water is available at temperature of 30C. It is also an interesting option for heat integration and recovery because it will unload downstream deaerator and reduce steam consumption.
Process heat load (45,000 kW) is such that BFW flow rate is not sufficient to meet the target temperature of 60C and additional cooling streams have to be introduced. One of many concepts that is being proposed to us is so-called “evaporative cooling” where, as you said, mass transfer phenomenon (diffusion) is used to enhance cooling and provide required temperature level of process stream.
I remember from my previous experience that evaporative cooling concept is nothing but saturation of air with fine water vapor mist, in order to reduce air temperature from dry bulb to wet bulb conditions. Doing that way, driving force for heat transfer is increased and less surface area is required for the same heat load. Or, as I encountered in the past, it is possible to debottleneck some process condensers lacking of required cooling capacity.
The concept was to calculate amount of water that can be evaporated and diffused into the air, by using fine, high pressure drop nozzles and high purity water (at least cooling water – not service water or fire water) in order to avoid accelerated fouling and corrosion. And at the same time, I remember that no liquid water was allowed to be in the contact with tubes (process stream inside) – due to thermal stresses, sticking effect of liquid water (sites for fouling) and corrosion potential. So the trick was to produce very fine water mist and provide sufficient time for water evaporation before air hits the process tubes.
Here, in this concept, situation is quite a bit different: complete flow of boiler feed water is introduced over the tubes and additional air flow is provided to meet process targets. As I calculated, evaporation of water does take place and – ideally speaking – reduces air temperature down to wet bulb temperature. But, in my opinion, the gross heat transfer is sensible heat transfer and not evaporative cooling!
Because of this environmental restriction (not discharging air hotter than 70C), calculated fan capacity which results in meeting process and environmental demands is 160,000 kg/h. This way, 40,000 kg/h of boiler feed water is lost in the form of vapor. Remaining liquid portion of 70C water is collected from the basin and transported to deaerator.
My question is: is it possible (and feasible) to operate the system (“evaporator”) in this manner, by introducing huge amount of liquid water over hot process tubes? In such case, relative humidity of air does not play any role in equipment design since the higher portion of heat exchange is occurring via sensible heat transfer and not by evaporation and air conditioning. The weather here is very humid, with lots of sand storms and accumulated dust in plant area. I am confused about this concept and it doesn't look to me like it will work.
Can you throw some additional light on this subject?
Many thanks again,
[attachment=711:Water_Fi...aporator.xls]
Thank you for your excellent reply and quality links you provided.
I am attaching a scheme of this “evaporative system”, with process heat and material balance data written below.
Process stream is a 3-phase fluid, consisting of hydrocarbon gas, steam, oil and high percentage of liquid water (72% water cut). Total mass flow rate is 311,000 kg/h with pressure set at 2.5barG and temperature of 127C upstream of heat transfer equipment. The aim is to cool this stream down to 60C. Allowable pressure drop for heat transfer utilization is 1bar.
For cooling purposes, 368,000 kg/h of boiler feed water is available at temperature of 30C. It is also an interesting option for heat integration and recovery because it will unload downstream deaerator and reduce steam consumption.
Process heat load (45,000 kW) is such that BFW flow rate is not sufficient to meet the target temperature of 60C and additional cooling streams have to be introduced. One of many concepts that is being proposed to us is so-called “evaporative cooling” where, as you said, mass transfer phenomenon (diffusion) is used to enhance cooling and provide required temperature level of process stream.
I remember from my previous experience that evaporative cooling concept is nothing but saturation of air with fine water vapor mist, in order to reduce air temperature from dry bulb to wet bulb conditions. Doing that way, driving force for heat transfer is increased and less surface area is required for the same heat load. Or, as I encountered in the past, it is possible to debottleneck some process condensers lacking of required cooling capacity.
The concept was to calculate amount of water that can be evaporated and diffused into the air, by using fine, high pressure drop nozzles and high purity water (at least cooling water – not service water or fire water) in order to avoid accelerated fouling and corrosion. And at the same time, I remember that no liquid water was allowed to be in the contact with tubes (process stream inside) – due to thermal stresses, sticking effect of liquid water (sites for fouling) and corrosion potential. So the trick was to produce very fine water mist and provide sufficient time for water evaporation before air hits the process tubes.
Here, in this concept, situation is quite a bit different: complete flow of boiler feed water is introduced over the tubes and additional air flow is provided to meet process targets. As I calculated, evaporation of water does take place and – ideally speaking – reduces air temperature down to wet bulb temperature. But, in my opinion, the gross heat transfer is sensible heat transfer and not evaporative cooling!
Because of this environmental restriction (not discharging air hotter than 70C), calculated fan capacity which results in meeting process and environmental demands is 160,000 kg/h. This way, 40,000 kg/h of boiler feed water is lost in the form of vapor. Remaining liquid portion of 70C water is collected from the basin and transported to deaerator.
My question is: is it possible (and feasible) to operate the system (“evaporator”) in this manner, by introducing huge amount of liquid water over hot process tubes? In such case, relative humidity of air does not play any role in equipment design since the higher portion of heat exchange is occurring via sensible heat transfer and not by evaporation and air conditioning. The weather here is very humid, with lots of sand storms and accumulated dust in plant area. I am confused about this concept and it doesn't look to me like it will work.
Can you throw some additional light on this subject?
Many thanks again,
[attachment=711:Water_Fi...aporator.xls]
#4
Posted 04 February 2008 - 08:51 PM
Zaub:
I've downloaded your workbook and although your sketch is great, I could find no material balance table, or a listing of the fluid streams below the sketch as you indicate.
Nevertheless, the idea I get is similar to yours: The atmospheric air being blown across the process tubes is going to be next to nothing in giving you any thermal advantages. I believe the air drawn in is going to just complicate things and share in taking with it some of the process heat you want (or need) in the boiler feed water (BFW). I suspect the apparatus will function as just a sensible heat transfer machine and not as a true evaporative machine. And, if that is the case, then you have gained nothing but additional practical operating problems in the location where you find yourself (Muscat). What I visualize you would wind up with is a sensible heat transfer to the drawn air and to the BFW. However, knowing Muscat and the area near the Gulf, you will start to contaminate the basin with fine sand particles and you will have to introduce filters and spare pumps to allow you to work continuously. And this is not considering any biological treatment that you may need due to the atmospheric exposure of the water. All of this - when compared with a counter-current heat exchanger device between the hot process fluid and the BFW - just means more operating costs and troubles due to the constant contamination of the introduced BFW.
Granted, I haven't seen the heat and material balance but from what you describe I get the idea that if you are forced to recoved the heat in the process to dedicate to pre-heating BFW, I would opt for a closed and common counter-current heat exchanger with the BFW in the tube side.
Does what I say make any sense or have I gotten the wrong idea?
#5
Posted 05 February 2008 - 10:08 AM
That was a great reply again Mr Montemayor and it was exactly what I needed.
The concept of evaporative cooling I know is – basically (and not related to any project in particular) – conditioning of air with sufficient amount of water in order to reach wet bulb conditions. That means no liquid water is present in the air stream flowing across the tubes – just the air cooled (“conditioned”) down to the wet bulb temperature. Another issue is – as you said – whether it offers any thermal advantages or not. And I completely agree with you in this subject – there is no practical use of this configuration.
In this concept proposed from the client and the vendor I do not see ANY advantage over employing standard heat exchanger devices. I should flush 370 t/h of Boiler Feed Water (BFW) across the tubes and then recollect it from evaporator basin and transport it further? Why would I want to do that? I will ruin the quality of chemically and biologically clean BFW by exposing it to atmosphere and sand particles, and probably would need to re-treat it again. Not to mention huge losses of BFW evaporated in this weird heat transfer arrangement, fouling, plugging and corrosion of evaporator process tubes etc… I've made a kind of personal report with two extreme options for evaporative cooling, attached below.
I apologize for not attaching material balance data. I am doing it now, and also adding few more documents. In order to avoid confusion, you can see heat and material balance data within heat exchanger datasheets (just necessary parts). So, the process stream that enters heat exchangers upstream of bulk separator vessel is the process stream that is meant to be cooled in an evaporator (in this weird concept), and the BFW data are provided in the second exchanger (train) datasheets: inlet BFW stream at 30C and corresponding flowrate. If you have any problems in managing with this information, just let me know and I will rearrange it.
I proposed to the client exactly what you have said: good old shell and tube technology. The case I have here is how to convince the client to choose shell & tube heat exchangers for this application. They are not so much concerned about future operational problems (a great mistake in a way of thinking!) and almost everything is related to capital expenditures and very tricky design of these babies: as you may guess, the duty is rather high (2 production sites with 46,000 kW of heat load which gives almost 100,000 kW in total duty required). This means that heat exchanger network has to be employed, with all possible restrictions and limitations I have (see attached workbooks) – very small pressure drop available upstream of bulk separator vessel and very high area required. Since the total head load and temperature level of process stream are such that available BFW flow rate is not sufficient for meeting process targets (60C final temperature), I have to split this heat load in two sequences: upstream and downstream of bulk separator vessel, and to employ air coolers as compressor suction condenser/cooler. Of course, as you can see, the maximum duty that can be obtained in heat exchanger train upstream of bulk separator vessel directly affects the load of compressor suction cooler and operation of exchanger train downstream of separator vessel. The more duty achieved in 1st exchanger train, the better: heat recovery goes up and the size of compressor suction air cooler goes down. But again, pressure drop margin is very tight and I should keep the velocities inside heat exchangers within recommended limits.
By balancing heat loads between upstream and downstream exchanger train, I came out with very general results – in terms of total UxA required for a given heat load. The thing I always keep in my mind is: maximum allowable pressure drop across heat exchanger train upstream of separator vessel cannot exceed 0.7 bar and there should be no more than 3 parallel trains due to flow maldistribution concerns. So how to determine the duty that is reasonably to obtain in the 1st exchanger train (upstream of bulk separator)? For first-hand calculations, I have chosen TEMA AES type of exchangers, knowing that pressure drop is generally low in these devices (and that heat transfer performance is poor – no temperature crosses). You can see in the attached workbook my concept of keeping hot fluid outlet temperature always 5-25C above cold fluid outlet temperature. But for the biggest duty UxA factor is huge, and by taking the lowest calculated U value for this service (250W/m2.C) area comes out to be very large – without knowing if other criteria will be met (pressure drop, velocities etc.).
The issue here is that I don’t have any heat exchanger network design software and I think it is impossible to do it manually… Or it would take months to do it in a proper manner.
Thank you for your time to go through this rather long thread. I certainly have my reasons, and the biggest one is – learning from a professional like you.
Onwards,
[attachment=714:Evaporat..._cooling.pdf]
[attachment=715:Heat_Rec...t_Design.xls]
[attachment=716:Art___Process_Data.xls]
The concept of evaporative cooling I know is – basically (and not related to any project in particular) – conditioning of air with sufficient amount of water in order to reach wet bulb conditions. That means no liquid water is present in the air stream flowing across the tubes – just the air cooled (“conditioned”) down to the wet bulb temperature. Another issue is – as you said – whether it offers any thermal advantages or not. And I completely agree with you in this subject – there is no practical use of this configuration.
In this concept proposed from the client and the vendor I do not see ANY advantage over employing standard heat exchanger devices. I should flush 370 t/h of Boiler Feed Water (BFW) across the tubes and then recollect it from evaporator basin and transport it further? Why would I want to do that? I will ruin the quality of chemically and biologically clean BFW by exposing it to atmosphere and sand particles, and probably would need to re-treat it again. Not to mention huge losses of BFW evaporated in this weird heat transfer arrangement, fouling, plugging and corrosion of evaporator process tubes etc… I've made a kind of personal report with two extreme options for evaporative cooling, attached below.
I apologize for not attaching material balance data. I am doing it now, and also adding few more documents. In order to avoid confusion, you can see heat and material balance data within heat exchanger datasheets (just necessary parts). So, the process stream that enters heat exchangers upstream of bulk separator vessel is the process stream that is meant to be cooled in an evaporator (in this weird concept), and the BFW data are provided in the second exchanger (train) datasheets: inlet BFW stream at 30C and corresponding flowrate. If you have any problems in managing with this information, just let me know and I will rearrange it.
I proposed to the client exactly what you have said: good old shell and tube technology. The case I have here is how to convince the client to choose shell & tube heat exchangers for this application. They are not so much concerned about future operational problems (a great mistake in a way of thinking!) and almost everything is related to capital expenditures and very tricky design of these babies: as you may guess, the duty is rather high (2 production sites with 46,000 kW of heat load which gives almost 100,000 kW in total duty required). This means that heat exchanger network has to be employed, with all possible restrictions and limitations I have (see attached workbooks) – very small pressure drop available upstream of bulk separator vessel and very high area required. Since the total head load and temperature level of process stream are such that available BFW flow rate is not sufficient for meeting process targets (60C final temperature), I have to split this heat load in two sequences: upstream and downstream of bulk separator vessel, and to employ air coolers as compressor suction condenser/cooler. Of course, as you can see, the maximum duty that can be obtained in heat exchanger train upstream of bulk separator vessel directly affects the load of compressor suction cooler and operation of exchanger train downstream of separator vessel. The more duty achieved in 1st exchanger train, the better: heat recovery goes up and the size of compressor suction air cooler goes down. But again, pressure drop margin is very tight and I should keep the velocities inside heat exchangers within recommended limits.
By balancing heat loads between upstream and downstream exchanger train, I came out with very general results – in terms of total UxA required for a given heat load. The thing I always keep in my mind is: maximum allowable pressure drop across heat exchanger train upstream of separator vessel cannot exceed 0.7 bar and there should be no more than 3 parallel trains due to flow maldistribution concerns. So how to determine the duty that is reasonably to obtain in the 1st exchanger train (upstream of bulk separator)? For first-hand calculations, I have chosen TEMA AES type of exchangers, knowing that pressure drop is generally low in these devices (and that heat transfer performance is poor – no temperature crosses). You can see in the attached workbook my concept of keeping hot fluid outlet temperature always 5-25C above cold fluid outlet temperature. But for the biggest duty UxA factor is huge, and by taking the lowest calculated U value for this service (250W/m2.C) area comes out to be very large – without knowing if other criteria will be met (pressure drop, velocities etc.).
The issue here is that I don’t have any heat exchanger network design software and I think it is impossible to do it manually… Or it would take months to do it in a proper manner.
Thank you for your time to go through this rather long thread. I certainly have my reasons, and the biggest one is – learning from a professional like you.
Onwards,
[attachment=714:Evaporat..._cooling.pdf]
[attachment=715:Heat_Rec...t_Design.xls]
[attachment=716:Art___Process_Data.xls]
#6
Posted 05 February 2008 - 02:21 PM
Zauber:
The more I study the basic data and the information you submitted, the more I am getting convinced that what you have is a SHE (Spiral Heat Exchanger) application.
I recommend you visit:
http://www.alfalaval...Heat_V3_low.pdf
I’ve used SHEs and I’ve seen some very large ones in Germany (@ BASF) and the performances are very impressive. The initial capital cost for a SHE is more than for an equivalent TEMA model – but their performance and maintenance costs are superior. And the design and fabricating quality from suppliers such as Alfa Laval is well-known. Here are the outstanding points I can cite for a SHE:
- It approaches the ideal in counter-current heat transfer. The long passages on each side permit very close temperature approaches;
- The media cannot intermix; the SHE is isolated by the welded closing on one side of each passage;
- It is compact and requires less installation and footprint space than conventional exchangers of equal surface (although an equal TEMA unit would require much more heating surface);
- They are easily maintainable;
- They avoid problems with differential thermal expansion;
- Because of less turbulent flow requirements in order to achieve heat transfer, the SHE yields a much lower pressure drop than other types of exchangers.
- The possibility of leakage in a SHE is less than in a TEMA model because the SHE is fabricated from much thicker plate than comparable condenser tube walls. And this is a big reason why the SHE has to cost more capital. – you get your money’s worth.
You are facing a formidable engineering design problem that might be transferred to a supplier – such as Alfa Laval. Alfa will easily give you a quick, budget capital cost – and upon studying your actual large size of unit, you might be able to talk them into doing a feasibility design that could convince a lot of people – based on Alfa’s reputation for sound and credible engineering in heat transfer. This could save you engineering money. Alfa has fabrication capabilities in India and this might be attractive to you for delivery and cost. Additionally, if it is worthwhile to exchange as much heat as possible into the BFW and cool the main Process stream as much as possible, Alfa might run optimization calculations for you. I would at least give them a call and have them visit your application. They are large heat exchanger experts and this is right up their alley.
I hope this helps out.
Similar Topics
![]() Guidance On Sizing Jacketed Pipe For Glycerine CoolingStarted by Guest_Kentucky08_* , 28 Jun 2025 |
|
![]() |
||
![]() What Kind Of Cooling System Should I Use To Cool Down A Jacketed MixinStarted by Guest_HollyBoni_* , 31 Jan 2025 |
|
![]() |
||
![]() Pressure Loss In Piping - Cooling Tower-Shelltube HeatexchangerStarted by Guest_Alneto_* , 29 May 2024 |
|
![]() |
||
Chiller Efficiency Dependence On Cooling Water TemperatureStarted by Guest_Neha Vensiyani_* , 29 Apr 2024 |
|
![]() |
||
Sizing Of Cooling Water Pipe LineStarted by Guest_Asif Azeez_* , 08 Jan 2021 |
|
![]() |