|
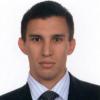
Waste Heat Boiler Design
#1
Posted 10 February 2008 - 08:56 PM
I am a student of 3rd year of Chemical Engineering. I have been asked to design a waste heat boiler present in a previous process design. The process was HCN by BMA process (Degussa). Well the waste heat boiler that I need to design is located just after the catalytic reactor, the process gases leave the reactor at a temperature of 1250oC and pressure of 2.06 bara and then enter the waste heat boiler. The gases leave the w.h.b at 300oC and a maximum pressure of 1.85 bara.
The gases leaving the reactor are mainly HCN, Ammonia, Hydrogen and methane. The flow rate of the gases is 2333.4 kg/h (most of it is HCN with a flow rate of 1723.1 kg/h)
The steam required from the waste heat boiler is at the follow conditions:
Pressure: 40 bara
Temperature: 280oC
The boiler feed water is taken from the utilities manager at a temperature of 105oC and a pressure of 41 bara.
I was wondering if you can give me ideas how can i tackle the design of the w.h.b.
What are the basic stages in desgin and what books or journals do I need to read.
Well all suggestions are welcome as this is my first design and I will appreciate any help from people with experience in this field
Thanks
#2
Posted 11 February 2008 - 09:19 AM
Heisenberg:
The first thing I recommend in this sort of assignment is to make a definitive decision on the type of heat transfer equipment that you will employ to carry out the project. In other words, you should select the specific type of hardware that you will design around first. This is not as simple or easy as you may think – and it is important to do this first.
In order to select the type of heat transfer equipment, you have to do some serious thinking and research (if required) on the equipment AND the process. Using the characteristics and properties of the process as well as the total Scope of Work of the Project, you can start to eliminate some rather obvious options. For example,
A kettle type of exchanger seems to be undesirable – although it is probably one of the most popular. The fact that the steam would be located on the shell side at 40 bara, makes it undesirable because the high pressure requires a very thick shell – and the shell of a kettle type is extraordinarily larger than other exchangers. Also, the process would be in the tube bundle and the relatively large size of the process flow rate makes for a humongous size of bundle (& shell) or for multiple units (which is uneconomical).
A standard TEMA type shell & tube exchanger is also out. The process would have to be in the tube side to allow steam to be generated on the shell and the multiple tube passes would consume the 0.32 bar pressure drop allowable. Besides, this apparatus does not give any vapor disengagement for the steam side – a very important and necessary feature of any steam generator. This is the reason why we looked at the kettle type, which has inherent vapor disengagement.
A coil or tube bundle inserted into a pressure vessel can also serve as a steam generator. However, this is a limited design in capacity. The size of the disengagement vessel required for a bundle sized for the large process gases would be very large once again. Besides, this design, while very simple and low in first capital costs, is very expensive to operate since it requires total disassemble of the bundle to clean and maintain it and the unit has to be totally out of service. This is impractical, since your Scope of Work probably requires that the unit be 100% on stream while there is process gas available.
What you may have to consider is to have multiple (two or three) heat transfer apparatuses connected to a common steam drum. In fact, this is one of the favorite ways to tackle this problem in industry. Please refer to the attached Excel Workbook for an idea of what I am describing. This method allows you to have spare connected capacity in the event you have to do maintenance on one of the units. Since the heat transfer pieces (simple BEU type of TEMA vertical exchangers) are vertical, they are easy to clean by rodding out the tubes in the event your process gas is a dirty or fouling one. Cleanliness of your process gas is another item that has to be considered in selecting your hardware.
You should study a classic book in Process Heat Transfer by Donald Q. Kern, called – guess what? - “Process Heat Transfer”.
Once you are decided on the type of hardware to apply, then make your Process Flow Diagram and generate your mass and heat balance. You can do this manually or use a simulation program, but do it and do it in this sequence. Your calculations should substantiate whether you will be condensing any portion of your process stream, in the heat exchange, or not. If you will have condensation, then a downward, vertical flow is to your advantage. But you can now see why it is very important to know beforehand what your physical constraints are at the beginning. You can always go back and change the type of heat transfer equipment or re-arrange the equipment configuration. But you must ensure that the physical equipment complies with the process requirements and results as well as with the Scope of Work.
After checking the accuracy and logic of your PFD, then generate a Piping and Instrumentation Diagram (P&ID).
To give you a kick-start on heat transfer application, I’m also attaching another heat transfer workbook for your study and use.
I hope you apply all your effort to this assignment. You will never regret it as you progress on to become a professional engineer.


#3
Posted 11 February 2008 - 08:29 PM
First that all I would like to thank you for your response. I found your suggestions extremly useful.
I also found the heat transfer workbook really good, it is full of excellent information, thanks again.
Coming back to the design, I think that you are right suggesting a system with few units. I was personally considering a vertical thermosyphon reboiler with a steam drum. I managed to get an article from a journal called: Petroleum Refiner the article is under the title: What you need to design thermosyphon reboilers and it was written by James R Fair.
I have read few pages of the article, it seems to be good and very informative but it emphises that the process fluid flows inside the vertical tubes (which implies boiling in the tubes) and as you told me and I have already thought the boiling for my desgin might take place in the shell and not on the tubes so I am a bit confused of what other piece of literature to look at. ( Heat transfer by Kern is already in my room)
I am also confused about the materias of contruction I am not very sure what material will stand temperatures like 1250C. I have checked Perry but I have not find an answer for that yet. (Have you got any suggestion of good literature that help me with the materials of construction as I also need to do the costing of my previous design (HCN plant) and I need to define materials for a series of equipement).
Meanwhile I am reading basic books like your reccommended Kern.
Muchas Gracias
Heisenberg
#4
Posted 12 February 2008 - 01:30 PM
Heisenberg:
If you are reading James Fair’s articles you are already helping yourself to some on the best heat transfer knowledge as applied to reboilers and similar equipment. Heat transfer has always been Fair’s strong suit and he’s is very strong on that subject. James Fair made a great name for himself while in industry and working for Monsanto, I believe. He later went into the academic field and is presently with the University of Texas in the Chemical Engineering Department there (I also believe). I have tried to read everything he has written on heat transfer, and I probably have the original article you are referring to.
A thermosyphon reboiler works best with a minimum pressure drop in the process side. That’s why Fair would put the boiling process fluid in the tube side with one pass. That makes sense for a reboiler application. What you have is the reverse: the process fluid is cooling down, not boiling. I show the hot process fluid in the tube side and the steam generation on the shell side – as you have suspected. And that is the usual configuration employed in industry. It seems the most logical because it retains the hot process in the smallest containment space – the tubes. And it is the tubes that are the easiest to clean and maintain since the shell side is totally welded and closed off to the outside.
You probably have known for some time that you were going to have a serious problem in trying to safely contain a super hot fluid at 1,250 oC. I have never even dreamt of going into that level of heat. Even Nickel and Titanium – or their alloys - may not be sufficient to safely contain this level of temperature. Consequently, you may be left with only one logical and sane alternative: quench the stream down to a manageable 650 oC level by injecting Boiler Feed Water into it. Then you can apply Nickel or Titanium alloys. What this means is that by reducing the driving force of the ultimate steam generator process, you are now requiring a large heat transfer area (bigger exchangers) and raising the capital cost. But you may not have an option simply because God didn’t give us a tough enough metal that is available, machineable, and weldable. Sometimes in engineering we get to that limit and we can go no further. It’s humbling, I know. But it is also one of the reasons that I maintain my religious faith.
#5
Posted 20 February 2008 - 09:55 PM
Just a quick question I need to find the Overall hea transfer coefficient (U) for my waste heat boiler design. I did find a value for gases and water which is in the range of (20-300) (W/m2C). Value found in Chemical Engineering Design Coulson and Richardson's volume 6 pag 637.
Somehow I believe that for my specific case having boiling on the shell of my heat exchanger the value I found has to be different.
Can anyone suggest how can I find the right value of U?
Thanks
#6
Posted 13 February 2009 - 02:26 AM
Greeting
I happen to get through your spreadsheet below, that makes me concievable about my topic of discussion.
Well iam an engineerir in cement company , and got an oppurtunity to design WASTE HEAR RECOVERY SYSTEM , in cement 30% of heat is being vented off which results in energy loss. To utilize this heat waste heat system proven out to be the best culprit of companies inclination of towards power generation.
My query is
1) In WHR raw heat is being used to generate the power , but as we have just stepped in to this process is there any spead sheet to design the equipments. I have the input , but to convert that input into output with having specifying the boiler , turbine makes me pose to proceed furthur . Basicall in cement plant if we know the capacity of clinker , we can prognosis the Power geeneration, but that is not end .
2) I am using your spread sheet of process heat transfer which gives consideratble and concious coverage what we want. But will this be enough to design the boiler or sizing the boiler if yers thn can you tell me how to start the process
3) You exuded to use the book Process Heat Transfer by Donald Q.. Can i get the same from you on my below mail ID . I did some googling to get it but fortunate googling always does not gives specific doucuments
AWAITING FOR YOUR VALUABLE REPLY
MY Mail ID is rahul.chaubey@flsmidth.com
Thanks in anticipation
REGARDS
RAHUL
#7
Posted 13 February 2009 - 07:00 AM
Rahul:
If you go to:
http://www.amazon.co...n/dp/0070341907
You will find that you can purchase Process Heat Transfer (in Hardcover) by D. Q. Kern for US $135.00 (used).
I recommend you start there.
#8
Posted 14 February 2009 - 01:46 AM
#9
Posted 16 February 2009 - 12:29 AM
Thanks for your generosity
But my concern is little bit focus on your attachment for Process heat transfer . What is want to know is how that sheet is going to patronage me.
Well while going the=rough the excel sheet , i admitted it to be very significent and perhabs this is what i was looikng for.
The sheet have the sub-shhets named as . But what does they do is something i want to get uderstand
1) TEMA Designation
2) Tube counts
3) HX Design
4) Typical U
5) Shell side pressure drop
6) Exchanger rating
7) Exchanger rating-2
8) TUBE SHEET
9) Square pitch
10) Total tubes
11) Tube pitch
Look sir, above data perhabs gives all that preliminary design stuff, but what is the application of above sheet and how to start the process , is something i want to get understand from you.
I did some correspondence to get through and here is my process what i adopted :-
1) Scaleout the exchanging rate fron Exchanging rate data sheet'
2) Specify the shell dia and tube dia with complete geometry- From which sheet to calc
3) Nu of shell passes- From which sheet to calc
4) Enter the data in HX design sheet
Note:- Above query is just for a preliminary design and to get the outline idea to design , i do perceived that there are spectrum of another process is also req like simulation to finalize the spec. But just to fuel up to get the idea of process to degn the boiler , perhabs this sheet could stake-out the actionable result
In HX design the presssure of steam is taken 450PSI , presumably good enough to meet the requrement for power generation
Sir i spoke to my mgt to issue the book, but since the data sheet given by you, i do not want to skip up without getting any consious coverage, bcaz as i conveive it be extreme panecia for me
Awaiting for your reply
Rahul
#10
Posted 01 March 2009 - 06:23 PM
i am 4th year mechanical engineering and i am working on the graduation project which is a design of waste heat recovery boiler , and i have some questions which i will be very gratefull if you replied to me
first the process gases is at 160 bar, 400 c , water is at 125 bar 125 c
steam is required at 350 c
i would like to know if the design of the economizer and the evaporator should be done as non seperate parts
OR 2 seperate H.EX
i tried to design the economizer as a shell and tube heat exchanger and i think it has suitable dims (A0= 572 m2 , L = 8.5 m , Ds = 1 m )
also i was asked to make a comparison betn atmospheric pressure gases
but i have a problem in the design of the economizer as a shell and tube as the pressure drop is an imaginary no in both cases when the water inside tubes or shell
so how can i design it ( CAN i design it as an air cooler H.EX)
finally i have the (PROCESS HEAT TRANSFERE )but i didnt find any data about the construction of the waste heat boilers
if there any books or documentation that could help me to know about the constructions and how to choose the suitable one please tell me
THANK U VERY MUCH IN ADVANCE AND I REALLY APRECIATE YOUR HELP
#11
Posted 01 March 2009 - 07:32 PM
Ahmed:
First of all, this thread is over 1 year old. Please let it rest in peace. You have a completely new topic and nothing to add to this thread that is of value to it. So why "skyjack" this thread?
Instead, start a new thread of your own that can be dedicated specifically to your topic alone. That way, other members can feel secure that they can add value to your thread by commenting and recommending their ideas on your specific questions and/or queries.
When you start your new thread, please organize your basic data and ideas. You have written a very complex and confusing post. List your basic data. For example, you have failed to give us the most important piece of information: the flow rate of the process gases and their composition - total composition. Make sure to note if your process gas is a clean one or if it contains solids or other impurities.
You also fail to tell us how much steam you want to produce - as well as showing us your calculations for the total heat transferred in the steam generator. This is gross negligence in presenting basic data for a heat transfer piece of equipment.
You write of an economizer and an evaporator without identifying what you are economizing and what purpose the evaporator serves. Are you confusing the process steam generator as an evaporator? I think we all know what a generic economizer is - but what exactly are you economizing? A boiler economizer, for example, exchanges heat between the flue gas and the feed water. What does yours do? You must furnish an engineering sketch of your process steam generation system and you must select the type of steam generator apparatus that will generate the steam. If you don't know how to select the type of apparatus, then be honest and forthright and tell us that. Also admit what you don't know and what you need help in. However, do the basic engineering calculations and sketches in order to communicate what you have done up to now.
Do not expect us to do your work for you. You claim to be a senior student and therefore I expect a complete and detailed engineering description of what you propose and a copy of your calculations to check your work. We will help you with those areas where you have problems by answering your questions and checking what you propose. But we will not do the original thinking, research, calculations, and organization that is expected from you.
I will be on the lookout for your new thread in the Student Forum.
#12
Posted 02 March 2009 - 04:07 AM
I didn’t mentioned all the data as I didn’t mean to make the calculation for me
as u said I don’t expect any body to do my work for me
the economizer is a generic economizer to heat the feed water before entering the
evaporator from 125 c to less than Tsat by about 15 c ( 125 – 313)
as you suggested I will write a new topic in the student forum & I will try to organize my basic data taking in consideration your points that you have mentioned.
THANKS FOR YOUR CONCERNING
#13
Posted 07 July 2009 - 08:45 AM
I didn't mentioned all the data as I didn't mean to make the calculation for me
as u said I don't expect any body to do my work for me
the economizer is a generic economizer to heat the feed water before entering the
evaporator from 125 c to less than Tsat by about 15 c ( 125 – 313)
as you suggested I will write a new topic in the student forum & I will try to organize my basic data taking in consideration your points that you have mentioned.
THANKS FOR YOUR CONCERNING
Hello sir
Great to have you on this subject.
Apparantly we are cement manufacturer and proposing to have waste heat recovery boiler. Since the dust particle in flue gas are sticky in nature . Geometrically i been understand from our suppler to go for hozontal boiler(horizontal fluegas and vertical tubes) in view o get teh cross flow of the syste,. Indeed crossflow accounts good heat transfer coeff and seems to be perfect, but what makes me constraint to go with this approach is area availability in cement plant.
I intend there is technology of vertical boiler (fluegas vertical, tubes vertical) including some mechanical arrngement in essence to achieve cross flow and appropriate heat transfer coeff, do you see this arrangement viable. The reason to adhere with the vertical tubes is to get the dust sticked at tubes fall down by using mechanical hammer
What is your opinion(Advantage and disadvantage) with this application of approach . Do you have this type of arrangement
Give me your personal mail ID for furthur correspondence
#14
Posted 07 January 2010 - 03:54 AM
Waste Heat Boilers are usually supplied with an overhead Steam Drum for water and steam circulation with a large recirculation rate to ensure effective cooling. For more information you can find more articles on the internet.
_____________________
Greentech are specialists in a range of Gasification Boilers Services
#15
Posted 10 January 2010 - 06:45 AM
For the successful design and fabrication of heat recovery equipment for the extraction of heat from high temperature process or flue gas streams, the following factors has to be considered. Waste Heat Boilers can be designed to cool process gases with temperatures above 2,600 degrees F (1,400 degrees C) and pressures above 3,000psi (210 kg/cm2), generating high quality steam to pressures higher than 2,100 psi (150 kg/cm2) and for steam generation rates up to 500,000 lb/hr (230,000 kg/hr).
Can somebody advise minimum waste gas temperature that would (economically) justify installation of a Waste Heat Boiler downstream? We speak about stack gases without dust of near atmospheric pressure and of flow rates higher than (say) 6 kg/s (approx 18000 Nm3/h), found in industrial boilers, etc.
This question concerns many "old" installations. Chau's cement process has the additional disadvantage of dusty flue gases. Acid dew point for fuels of 0.8% sulphur can be about 135 deg C.
Of course approximate (order of magnitude) values are expected.
In local work place this temperature limit was considered as about 550 deg 15 years ago, but now it is certainly lower (probably 250 deg C ?).
Edited by kkala, 10 January 2010 - 06:54 AM.
#16
Posted 10 January 2010 - 11:31 AM
kkala:
This topic is over 2 years-old and, more importantly is from a very troubled and eccentric student(?) who kept changing his nickname over 5 times in the short time he was inquiring with our Forums. He has, thankfully, gone away now after raising a lot of commotion and concern due mostly to his clandestine and suspicious claims - not to mention his torture of the English language.
If you have a related topic, please follow the instructions given you in our Forum Guidelines: do not skyjack this thread but, instead, start your own detailed and personal thread so that our members can address and comment on your specific topic.
I will delete your posting after you start your own thread. Let's cooperate with the Forum Guidelines and start our own threads instead of following our lazy instincts and using other's threads to generate contributions.
#17
Posted 27 January 2010 - 06:02 PM
Bob Walsh advised recently on upper temperature limit (7 Jan 2010) and I supplementary asked for low temperature limit (10 Jan 2010), which concerned exploitation of flue gases upstream of stacks. The latter means "Waste Heat Boiler" for a lot of people.
If you have a related topic, please follow the instructions given you in our Forum Guidelines: do not skyjack this thread but, instead, start your own detailed and personal thread so that our members can address and comment on your specific topic.
I will delete your posting after you start your own thread. Let's cooperate with the Forum Guidelines and start our own threads instead of following our lazy instincts and using other's threads to generate contributions.
Forgetting the "lazy instincts" and "skyjack", I request Art Montemayor not to delete the postings but leave them as they are. Backwriting is not good.
Colleagues, asked about my question of 10 Jan 2010, recommend flue gas temperature of approximately 250 0C (min) for an Waste Heat Boiler.
Flue gases exit from stack should be 160 0C (25 0C above acid dew point), so 6 kg/s flue gases can be further cooled by 90 0C, giving 1*6*90=540 kJ/s, or about 3 t/h of 1.5 Barg steam. Advice from manufacturers is necessary to assess feasibility of such an installation.
Edited by kkala, 29 January 2010 - 02:42 PM.
Similar Topics
Design Capacity Of Hydrogen Pullet During Hydroprocessing Units UpsetStarted by Guest_Divid Kelin_* , 18 Jun 2025 |
|
![]() |
||
Hot Oil Loop / Heating Medium DesignStarted by Guest_Lyne_* , 30 Mar 2024 |
|
![]() |
||
![]() Hello, Design Of Natural Gas Liquefaction Processes.Started by Guest_guoyinyanliner_* , 18 Jun 2025 |
|
![]() |
||
Steam Pressure In Heat ExchangerStarted by Guest_mvanrijnbach_* , 15 Apr 2025 |
|
![]() |
||
![]() Scrubber DesignStarted by Guest_nasss_* , 07 Aug 2024 |
|
![]() |