In a few ongoing projects, TEG dehydration unit design encompasses reboiler type selection and detailed design. All three types (direct fired, electrical, and hot-oil system) are being considered.
Contactor operates with 99.9% glycol purity, and is regenerated in a packed still column operating at 204°C reboiler temperature. From reboiler, it passes through a small stripping column in order to achieve desired TEG purity.
Since reboiler will be operating at maximum allowable temperature (in order to suppress glycol thermal degradation), I am looking for a “hands-on experienced” advice related to maximum hot-oil supply temperature and maximum metal skin temperature in this service.
According to different standards and available literature, maximum allowable temperature difference between the reboiler tube wall and bulk fluid outside the tubes is about 6-7°C (for organic compounds), and maximum allowable glycol film temperature is limited to approx 206-207°C. On the other hand, standard heat flux applicable for TEG regenerator reboilers (literature values) goes up to 25,000 W/m² which, in return, for calculated heat transfer coefficient in pool boiling service, gives rather high MTD and – consequently – very high hot oil supply temperature. Following the first criteria, I ended up with 60m² surface area; while using max. allowable heat flux and calculated heat transfer coefficient, I found surface area to be about 7m². Reboiler tubes are SS 316L.
Also, in direct-fired or electrical heaters, how does one calculate the required surface area based on reboiler duty requirements?
Can anyone shed some light on this interesting subject?
Thank you in advance,
|
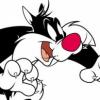
Glycol Reboiler
Started by Zauberberg, May 02 2008 06:52 AM
3 replies to this topic
Share this topic:
#1
Posted 02 May 2008 - 06:52 AM
#2
Posted 02 May 2008 - 08:45 AM
Zauber:
I always use the heat flux criteria to design the TEG reboiler tube bundle. I use 8,000 Btu/hr-ft^2 as the design flux. I believe you will find most suppliers of TEG dehydration units design on a basis of 10,000+ Btu/hr-ft^2 as their flux. The higher the flux, the higher the skin temperature (you have less heat transfer area available). 400 oF is the max. temperature I operate a TEG reboiler at. I have found that I can meet my product gas dew point specs holding that max. temperature constant and using my stripping gas as the means to ensure the quality of the lean TEG going to the contactor.
Hot oil is, in my opinion, the best heat transfer you can apply to a TEG reboiler. The skin temperature should be the lowest when compared to direct-fired or electric element. I've used all 3. The flux = Q/A. With a constant Q, the area will be larger with a lower flux. That's why I won't go higher than 8,000.
Hope this helps.
I always use the heat flux criteria to design the TEG reboiler tube bundle. I use 8,000 Btu/hr-ft^2 as the design flux. I believe you will find most suppliers of TEG dehydration units design on a basis of 10,000+ Btu/hr-ft^2 as their flux. The higher the flux, the higher the skin temperature (you have less heat transfer area available). 400 oF is the max. temperature I operate a TEG reboiler at. I have found that I can meet my product gas dew point specs holding that max. temperature constant and using my stripping gas as the means to ensure the quality of the lean TEG going to the contactor.
Hot oil is, in my opinion, the best heat transfer you can apply to a TEG reboiler. The skin temperature should be the lowest when compared to direct-fired or electric element. I've used all 3. The flux = Q/A. With a constant Q, the area will be larger with a lower flux. That's why I won't go higher than 8,000.
Hope this helps.
#3
Posted 02 May 2008 - 09:23 AM
Thank you for reply Mr Montemayor,
Heat flux value of 25,000W/m² looks OK. I also found some other references for operating regenerator reboilers with even higher heat fluxes - more than 31,500W/m², as you said.
What confuses me is the fact that 25,000W/m² flux can be achieved with different hot oil supply/return temperatures (but same MTD), for the same boiling heat transfer coefficient. However, based on maximum TEG film temperature of 206-207°C and maximum allowable temperature difference between outside tube wall and bulk TEG fluid (refer to Kern's chapter related to vaporization services), I calculated that my hot oil supply temperature cannot exceed ~220°C. And depending on choosen return temperature, hot oil flowrate changes for the fixed duty. I wanted to confirm if this is the right way to design reboiler, because it will also affect hot oil system design parameters.
Best regards,
Heat flux value of 25,000W/m² looks OK. I also found some other references for operating regenerator reboilers with even higher heat fluxes - more than 31,500W/m², as you said.
What confuses me is the fact that 25,000W/m² flux can be achieved with different hot oil supply/return temperatures (but same MTD), for the same boiling heat transfer coefficient. However, based on maximum TEG film temperature of 206-207°C and maximum allowable temperature difference between outside tube wall and bulk TEG fluid (refer to Kern's chapter related to vaporization services), I calculated that my hot oil supply temperature cannot exceed ~220°C. And depending on choosen return temperature, hot oil flowrate changes for the fixed duty. I wanted to confirm if this is the right way to design reboiler, because it will also affect hot oil system design parameters.
Best regards,
#4
Posted 18 April 2010 - 05:55 PM
Hello,
In your post u stated that you read in the literature and I quote "goes up to 25,000 W/m² which, in return, for calculated heat transfer coefficient in pool boiling service, gives rather high MTD and consequently very high hot oil supply temperature. Following the first criteria, I ended up with 60m² surface area."
I would pretty much appretiate if you direct me to this literature or source of your that looks helpfull in my paper i'm writing in school.
Thank you,
Chem_fan
In your post u stated that you read in the literature and I quote "goes up to 25,000 W/m² which, in return, for calculated heat transfer coefficient in pool boiling service, gives rather high MTD and consequently very high hot oil supply temperature. Following the first criteria, I ended up with 60m² surface area."
I would pretty much appretiate if you direct me to this literature or source of your that looks helpfull in my paper i'm writing in school.
Thank you,
Chem_fan
Similar Topics
Levels For Kettle Type ReboilerStarted by Guest_RajD_* , 04 Apr 2025 |
|
![]() |
||
Phe As ReboilerStarted by Guest_Chemeng40_* , 20 Feb 2025 |
|
![]() |
||
![]() How To Replace Existing Reboiler With A Thermosyphon Reboiler In HysysStarted by Guest_tomr91_* , 04 Feb 2025 |
|
![]() |
||
![]() Thermosiphon ReboilerStarted by Guest_Abdelrahman Tarek_* , 17 Sep 2024 |
|
![]() |
||
![]() Kettle Reboiler Flow FractionsStarted by Guest_Lyne_* , 31 Mar 2024 |
|
![]() |