|
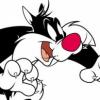
Reboiler Type Selection
Started by Zauberberg, Aug 01 2008 07:25 AM
8 replies to this topic
Share this topic:
#1
Posted 01 August 2008 - 07:25 AM
During evaluation of various reboiler types which are suitable for condensate stabilizer application, I ended up with two final solutions:
1. AKT/BKT kettle-type units, and
2. Forced circulation arrangement
Heating fluid (hot water) flow is limited and therefore not suitable for standard U-tube configuration: in order to obtain high heat transfer coefficients on the tube side I need at least 6 passes. Forced circulation looks also interesting, but I think it's not mandatory to choose such design since the condensate originates from retrograde reservoir system and is - esentially - clean, which makes kettle reboiler very attractive. Furthermore, forced circulation type has additional pumping expenses.
I need assistance from ChE forum members regarding applicability and reliability of AKT/BKT units in reboiling service - how does this type of rear head actually works out there in the field. Are these units employed anywhere? Any operational, safety and reliability issues which I'm not aware of? Till now, I had experience only with the most common AKU/BKU types.
Thanks in advance,
[attachment=976:AKT.JPG]
1. AKT/BKT kettle-type units, and
2. Forced circulation arrangement
Heating fluid (hot water) flow is limited and therefore not suitable for standard U-tube configuration: in order to obtain high heat transfer coefficients on the tube side I need at least 6 passes. Forced circulation looks also interesting, but I think it's not mandatory to choose such design since the condensate originates from retrograde reservoir system and is - esentially - clean, which makes kettle reboiler very attractive. Furthermore, forced circulation type has additional pumping expenses.
I need assistance from ChE forum members regarding applicability and reliability of AKT/BKT units in reboiling service - how does this type of rear head actually works out there in the field. Are these units employed anywhere? Any operational, safety and reliability issues which I'm not aware of? Till now, I had experience only with the most common AKU/BKU types.
Thanks in advance,
[attachment=976:AKT.JPG]
#2
Posted 01 August 2008 - 08:51 AM
Zauberberg:
You don't explicitly tell us what you propose to put through the tubes and what will be in the kettle. Therefore, I have to presume you are proposing to flow hot water through the tubeside while you have condensate being reboiled in the shell.
I have been – and continue to be – totally opposed to the application of a removable tube bundle in a Kettle shell that has a removable, pull-through, floating head. In the past, before I followed the given instructions, I was dead-set against it but I was a Junior engineer and had to follow orders from my supervisors. The bad results proved I was right and I never forgot how really impractical the basic concept of a removable, pull-through, floating head design is WHEN YOU ARE DEALING WITH TOTALLY CLEAN, HOMOGENOUS FLUID IN THE TUBESIDE.
Please note carefully what I have highlighted. I have never found an engineer that could justify the use of a removable, pull-through, floating head when a practical and credible reason can't be presented that would require that type of construction. Hot water certainly doesn't justify it and neither does steam – especially high pressure steam (or hp water). HOWEVER, I will apply a removable, pull-through, floating head when I am putting a dirty, fouling fluid through the tubes that will eventually require a need to "rod out" the tubes. I will also apply it only if the tubeside fluid is process and safety-compatible with the shellside fluid. THAT, I can justify – but not what you are describing. I have had the experience where I had to replace that type of construction with a 100% U-tube – and the solution worked for years. The problems with a removable, pull-through, floating head design are not only the capital costs, the weight, the ungainly and large diameter required, but more importantly THE INEVITABLE LEAKAGE of the tubeside fluid through the inherent gasket that is subject to continuous stress and the inability to tighten and secure the flanged connection. This type of joint inserted into a continuous process is a leak waiting to happen and is nothing but a pain in the backside of Operations personnel and maintenance departments. And, I can assure you, the flanged joint WILL leak. Depending on the reboiler temperature, your bolting will require pre-loading in order to ensure that the threads won't back-off during operation and cause leakage – and possibly gasket rupture. But even that isn't guaranteed.
Now, compare the above with the fact that I can easily design a fixed, welded U-tube bundle to have 4 – and even 6 – tubeside passes. Besides that fact, you are also stating that "the condensate originates from retrograde reservoir system and is - essentially – clean". I have to also assume that your hot water is relatively clean (since it is hot). Unless your hot water has a lot of contaminants, solids, and will foul your tubes, then I see no reason for worrying about a fixed, U-Tube bundle. Even if the pressure drop through a 6-tube pass unit was too large, I would still look at applying a hot water pump to "pump through" the reboiler hot water. That, in my opinion is much better to live with than an internal flanged connection.
Even if your boss (or client) is insisting on a removable, pull-through, floating head design, I would challenge the logic, justification, practicality, and common sense of this type of fabrication. I totally agree with your choice of a Kettle; I disagree with your type of tube bundle.
I hope this experience is of some help.
You don't explicitly tell us what you propose to put through the tubes and what will be in the kettle. Therefore, I have to presume you are proposing to flow hot water through the tubeside while you have condensate being reboiled in the shell.
I have been – and continue to be – totally opposed to the application of a removable tube bundle in a Kettle shell that has a removable, pull-through, floating head. In the past, before I followed the given instructions, I was dead-set against it but I was a Junior engineer and had to follow orders from my supervisors. The bad results proved I was right and I never forgot how really impractical the basic concept of a removable, pull-through, floating head design is WHEN YOU ARE DEALING WITH TOTALLY CLEAN, HOMOGENOUS FLUID IN THE TUBESIDE.
Please note carefully what I have highlighted. I have never found an engineer that could justify the use of a removable, pull-through, floating head when a practical and credible reason can't be presented that would require that type of construction. Hot water certainly doesn't justify it and neither does steam – especially high pressure steam (or hp water). HOWEVER, I will apply a removable, pull-through, floating head when I am putting a dirty, fouling fluid through the tubes that will eventually require a need to "rod out" the tubes. I will also apply it only if the tubeside fluid is process and safety-compatible with the shellside fluid. THAT, I can justify – but not what you are describing. I have had the experience where I had to replace that type of construction with a 100% U-tube – and the solution worked for years. The problems with a removable, pull-through, floating head design are not only the capital costs, the weight, the ungainly and large diameter required, but more importantly THE INEVITABLE LEAKAGE of the tubeside fluid through the inherent gasket that is subject to continuous stress and the inability to tighten and secure the flanged connection. This type of joint inserted into a continuous process is a leak waiting to happen and is nothing but a pain in the backside of Operations personnel and maintenance departments. And, I can assure you, the flanged joint WILL leak. Depending on the reboiler temperature, your bolting will require pre-loading in order to ensure that the threads won't back-off during operation and cause leakage – and possibly gasket rupture. But even that isn't guaranteed.
Now, compare the above with the fact that I can easily design a fixed, welded U-tube bundle to have 4 – and even 6 – tubeside passes. Besides that fact, you are also stating that "the condensate originates from retrograde reservoir system and is - essentially – clean". I have to also assume that your hot water is relatively clean (since it is hot). Unless your hot water has a lot of contaminants, solids, and will foul your tubes, then I see no reason for worrying about a fixed, U-Tube bundle. Even if the pressure drop through a 6-tube pass unit was too large, I would still look at applying a hot water pump to "pump through" the reboiler hot water. That, in my opinion is much better to live with than an internal flanged connection.
Even if your boss (or client) is insisting on a removable, pull-through, floating head design, I would challenge the logic, justification, practicality, and common sense of this type of fabrication. I totally agree with your choice of a Kettle; I disagree with your type of tube bundle.
I hope this experience is of some help.
#3
Posted 01 August 2008 - 03:13 PM
Dear Zauberberg
Hello, Although broadly speaking I agree to Art's Comments as regards your non-exact tube side fluid service indication.
I only take this opportunity to share that I in my early days of working with previous refinery; I came across a very similar design of 'BFW/LP Condensate Reboiler or LP steam generator' utilyzing outflowing (PDA) propane de-asphalting unit resiuum's heat downstream of the resid strippers.
We had two of similar design units; which occassionally experienced water-hammer whenever the tube side's BFW or Condensate stream temperature was lower than design during winter month's night time change-over/ commissining and improper isolating valves operations.
May be this sounds helpful.
Regards
Qalander
Hello, Although broadly speaking I agree to Art's Comments as regards your non-exact tube side fluid service indication.
I only take this opportunity to share that I in my early days of working with previous refinery; I came across a very similar design of 'BFW/LP Condensate Reboiler or LP steam generator' utilyzing outflowing (PDA) propane de-asphalting unit resiuum's heat downstream of the resid strippers.
We had two of similar design units; which occassionally experienced water-hammer whenever the tube side's BFW or Condensate stream temperature was lower than design during winter month's night time change-over/ commissining and improper isolating valves operations.
May be this sounds helpful.
Regards
Qalander
#4
Posted 03 August 2008 - 11:08 AM
Gentlemen, thanks for the replies.
Art, I had difficulties in designing BKU unit with 6 tube passes - wondering how to manage total number of tubes and the number of tubes per pass, while avoiding excessive difference (+/- 5%) between passes. Your comment is correct, and the possibility of frequent leakage crossed my mind several times. This plant should be designed with availability of 99.5% and that is exactly why I needed your input and guidance in selecting such design which will not be a nightmare for Operations and Maintenance people.
Qalander, thank you for your comments.
Best regards,
Art, I had difficulties in designing BKU unit with 6 tube passes - wondering how to manage total number of tubes and the number of tubes per pass, while avoiding excessive difference (+/- 5%) between passes. Your comment is correct, and the possibility of frequent leakage crossed my mind several times. This plant should be designed with availability of 99.5% and that is exactly why I needed your input and guidance in selecting such design which will not be a nightmare for Operations and Maintenance people.
Qalander, thank you for your comments.
Best regards,
#5
Posted 04 August 2008 - 01:01 AM
Dear,Since I am not anymore with my previous employer therefore authenticating access to the verify my comment is not possible right now with documentations, however I am confident it was either a four or six pass design if recalled correctly.
If managed digging-out personal past papers/notes then I may be in a position to help at a later stage.Busy in domestic family importance issues right now.
Best Regards
Qalander
If managed digging-out personal past papers/notes then I may be in a position to help at a later stage.Busy in domestic family importance issues right now.
Best Regards
Qalander
#6
Posted 04 August 2008 - 02:12 PM
Dear Zaubergerg.
Another typical and undesirable, usually invisible and not very much noticeable phenomenon verified during my stay at the previous employer's place was; very peculiar observation in one of the smaller Low Pressure (300#watertube) boiler steam drum was found to contain resid/bitumen lump 3~4 ft long and variable haphazard shape 3~4 inches dia in the middle.
Probably a result of prolonged carry-over of fine molten entrained resid/bitumen particles from various plant sources& accumulated over very period of time(e.g 1) Resid strippers back flow if steam fails and NRV's get stuck,2)Similar as discussed in above post LP steam generators/LP condensate re-boiler over-pressurization and tubes material incidental leakage into shell steam chest area and carry-over etc.)
Hope this is also somewhat telling about the problem areas and care-taking needs.
Regards
Qalander
Another typical and undesirable, usually invisible and not very much noticeable phenomenon verified during my stay at the previous employer's place was; very peculiar observation in one of the smaller Low Pressure (300#watertube) boiler steam drum was found to contain resid/bitumen lump 3~4 ft long and variable haphazard shape 3~4 inches dia in the middle.
Probably a result of prolonged carry-over of fine molten entrained resid/bitumen particles from various plant sources& accumulated over very period of time(e.g 1) Resid strippers back flow if steam fails and NRV's get stuck,2)Similar as discussed in above post LP steam generators/LP condensate re-boiler over-pressurization and tubes material incidental leakage into shell steam chest area and carry-over etc.)
Hope this is also somewhat telling about the problem areas and care-taking needs.
Regards
Qalander
#7
Posted 05 August 2008 - 01:33 PM
Zauberberg,
Perhaps I'm being a bit dense, but what constraints are pushing you away from the 6 pass solution? It sounds like a good answer to me. If pressure drop is excessive you must adjust tube diameter, length, number of tubes, or number of tube passes. Fouling is combatted by maintaining velocity. I don't understand what "differences" you refer to. I concur with the desire to avoid the rear "T" head though my objection would be more mild unless even a very small cross-contamination would be a big problem. Please describe your problem in more detail.
Doug
Perhaps I'm being a bit dense, but what constraints are pushing you away from the 6 pass solution? It sounds like a good answer to me. If pressure drop is excessive you must adjust tube diameter, length, number of tubes, or number of tube passes. Fouling is combatted by maintaining velocity. I don't understand what "differences" you refer to. I concur with the desire to avoid the rear "T" head though my objection would be more mild unless even a very small cross-contamination would be a big problem. Please describe your problem in more detail.
Doug
#8
Posted 13 August 2008 - 02:41 PM
Hello Doug,
Contamination - as such - is not actually an issue, since heating medium is hot oil while reboiled liquid is stabilized condensate (light crude oil with TBP end point of approx. 400C). Any leakage of hot oil into the process fluid will not cause contamination but from availability point of view, plant operation would be adversely affected. And, as Art has pointed out, it would definitely be a "backpain" for Maintenance and Operations people.
I found myself to be "between a rock and hard place" in designing this system, since available hot oil flowrate is fixed. Inlet temperature, on the other hand, can be increased - but with a serious trade-off: risk of localized critical flux and vapor blanketing which would make this service inefficient. Therefore I decided to utilize hot oil pressure drop and boost the tube-side film coefficient, and I found rather difficult for myself to deal with 6-passes U-tube configuration without software assistance. So the idea was to try to explore the possibility of replacing BKU with BKT unit, which is - from my point of view - a little bit easier thing to be designed.
Anyway, U-kettle design is finalized and things went smooth to the very end. There's nothing so good like feeling satisfied and happy with the design you selected and executed - knowing that you have put big efforts in providing the basis for trouble-free plant operation.
P.S. I apologize because I stated that heat transfer fluid is hot water instead of hot oil, in my first post.
Contamination - as such - is not actually an issue, since heating medium is hot oil while reboiled liquid is stabilized condensate (light crude oil with TBP end point of approx. 400C). Any leakage of hot oil into the process fluid will not cause contamination but from availability point of view, plant operation would be adversely affected. And, as Art has pointed out, it would definitely be a "backpain" for Maintenance and Operations people.
I found myself to be "between a rock and hard place" in designing this system, since available hot oil flowrate is fixed. Inlet temperature, on the other hand, can be increased - but with a serious trade-off: risk of localized critical flux and vapor blanketing which would make this service inefficient. Therefore I decided to utilize hot oil pressure drop and boost the tube-side film coefficient, and I found rather difficult for myself to deal with 6-passes U-tube configuration without software assistance. So the idea was to try to explore the possibility of replacing BKU with BKT unit, which is - from my point of view - a little bit easier thing to be designed.
Anyway, U-kettle design is finalized and things went smooth to the very end. There's nothing so good like feeling satisfied and happy with the design you selected and executed - knowing that you have put big efforts in providing the basis for trouble-free plant operation.
P.S. I apologize because I stated that heat transfer fluid is hot water instead of hot oil, in my first post.
#9
Posted 17 August 2008 - 12:55 PM
QUOTE (Zauberberg @ Aug 13 2008, 02:41 PM) <{POST_SNAPBACK}>
Hello Doug,
Contamination - as such - is not actually an issue, since heating medium is hot oil while reboiled liquid is stabilized condensate (light crude oil with TBP end point of approx. 400C). Any leakage of hot oil into the process fluid will not cause contamination but from availability point of view, plant operation would be adversely affected. And, as Art has pointed out, it would definitely be a "backpain" for Maintenance and Operations people.
I found myself to be "between a rock and hard place" in designing this system, since available hot oil flowrate is fixed. Inlet temperature, on the other hand, can be increased - but with a serious trade-off: risk of localized critical flux and vapor blanketing which would make this service inefficient. Therefore I decided to utilize hot oil pressure drop and boost the tube-side film coefficient, and I found rather difficult for myself to deal with 6-passes U-tube configuration without software assistance. So the idea was to try to explore the possibility of replacing BKU with BKT unit, which is - from my point of view - a little bit easier thing to be designed.
Anyway, U-kettle design is finalized and things went smooth to the very end. There's nothing so good like feeling satisfied and happy with the design you selected and executed - knowing that you have put big efforts in providing the basis for trouble-free plant operation.
P.S. I apologize because I stated that heat transfer fluid is hot water instead of hot oil, in my first post.
Contamination - as such - is not actually an issue, since heating medium is hot oil while reboiled liquid is stabilized condensate (light crude oil with TBP end point of approx. 400C). Any leakage of hot oil into the process fluid will not cause contamination but from availability point of view, plant operation would be adversely affected. And, as Art has pointed out, it would definitely be a "backpain" for Maintenance and Operations people.
I found myself to be "between a rock and hard place" in designing this system, since available hot oil flowrate is fixed. Inlet temperature, on the other hand, can be increased - but with a serious trade-off: risk of localized critical flux and vapor blanketing which would make this service inefficient. Therefore I decided to utilize hot oil pressure drop and boost the tube-side film coefficient, and I found rather difficult for myself to deal with 6-passes U-tube configuration without software assistance. So the idea was to try to explore the possibility of replacing BKU with BKT unit, which is - from my point of view - a little bit easier thing to be designed.
Anyway, U-kettle design is finalized and things went smooth to the very end. There's nothing so good like feeling satisfied and happy with the design you selected and executed - knowing that you have put big efforts in providing the basis for trouble-free plant operation.
P.S. I apologize because I stated that heat transfer fluid is hot water instead of hot oil, in my first post.
Dear Doug& Zauberberg Hello and Good Evening,
This served a Great Deal towards a nice closing feed back, as well as source of Good Working Design Achievement as situation has become very clear and definitely praisworthy.
Best Regards
Qalander
Similar Topics
Selection Type Of Heater For Refrigerated PropaneStarted by Guest_livetolove003_* , 07 May 2025 |
|
![]() |
||
Levels For Kettle Type ReboilerStarted by Guest_RajD_* , 04 Apr 2025 |
|
![]() |
||
Phe As ReboilerStarted by Guest_Chemeng40_* , 20 Feb 2025 |
|
![]() |
||
![]() How To Replace Existing Reboiler With A Thermosyphon Reboiler In HysysStarted by Guest_tomr91_* , 04 Feb 2025 |
|
![]() |
||
![]() Activated Carbon SelectionStarted by Guest_Talhafarooq_* , 25 Nov 2024 |
|
![]() |