|
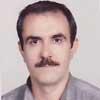
Optimum Dead Band
#1
Posted 04 July 2009 - 10:30 AM
How much value is the optimum dead band between each two systems among below systems in atmospheric/low pressure tanks:
-Vacuum relief system
-Blanketing system
-Operating vent system
-Pressure safety valve
-Emergency valve
Regards
#2
Posted 04 July 2009 - 11:14 AM
MAWP
MAWV
The operating band of the device from reseat to full open.
If you search this forum, you will find other postings on this subject.
#3
Posted 04 July 2009 - 12:17 PM
Thanks for your reply,but:
I want to know how much is the minimum value of dead band preventing two devices being operative at the same time.
#4
Posted 04 July 2009 - 01:04 PM
#5
Posted 05 July 2009 - 04:37 AM
How about the optimum value as i mentioned in my first post?
Can 100 mbar be an proper operative band for pressure/vacuum relief device?
#6
Posted 05 July 2009 - 08:43 AM
You can then, using the full operating band of each vent or valve, have them operate as far apart as is practical. In theory you can have the operating band of one device end where the band of the next device begins. Other than that I can not tell you anymore. I can not set an arbitrary value to your devices. You need to operate with the parameters available to you. In selecting equipment you may find that certain manufacturers equipment can operate at closer tolerances than others.
I will caution you that you must respect the MAWP and MAWV for the safety of your people and equipment.
#7
Posted 05 July 2009 - 10:53 AM
Sorry,i made mistake to convert 4" w.c. to mbar.Actually what i meant above was 10 mbar.
#8
Posted 05 July 2009 - 01:50 PM
#9
Posted 05 July 2009 - 05:16 PM
Vacuum Breaker fully open at MAWV
Vacuum Breaker set at 1/2 MAWV
Normal Relief set at 1/4 MAWP
Normal Relief fully open at 1/2 MAWP
Emergency Relief set at 1/2 MAWP
Emergency Relief fully open at MAWP
Like I said these are rough guidelines. I get my first pass with these guidelines, then I "tweak" it to reality where set pressures are whole numbers and not fractions. I like to have more "operating latitude" between the Normal Relief fully open and the Emergency Relief set pressure to minimize the leakage out the Emergency Relief.
#10
Posted 06 July 2009 - 05:20 AM
Emergency Relief set at 1/2 MAWP
Thanks a lot Latexman.
Looking above two equal values,then you will consider possible dead band inbetween?
In your typical example,set point of pressure regulating valve (if any,e.g. for blanketing) would be below 1/4 MAWP (around 1/8 MAWP as per your defined criteria?).
Am i right?
#11
Posted 06 July 2009 - 10:47 AM
Vacuum Breaker fully open at MAWV
Vacuum Breaker set at 1/2 MAWV
Normal Relief set at 1/4 MAWP
Normal Relief fully open at 1/2 MAWP
Emergency Relief set at 1/2 MAWP
Emergency Relief fully open at MAWP
Like I said these are rough guidelines. I get my first pass with these guidelines, then I "tweak" it to reality where set pressures are whole numbers and not fractions. I like to have more "operating latitude" between the Normal Relief fully open and the Emergency Relief set pressure to minimize the leakage out the Emergency Relief.
The fact that vent units achieve full open conditions at about 2x set pressure? Where did you come up with this fact? This is vendor specific and loads of vendors give full flow pressures at 10 or 20% overpressure.
#12
Posted 06 July 2009 - 12:28 PM
My assessment was based on low pressure vents that are dead weight or spring loaded, not pilot operated. My recommendations came from consultation with 3-4 major, worldwide suppliers and buying, testing, and maintaining thousands of them every year. At 10-20% overpressure in breather vents the flow is very erratic. 90% of full flow is usually around 70% overpressure. It is common practice to base designs on 100% overpressure.
What you say is true - for pilot operated low pressure vents.
#13
Posted 06 July 2009 - 02:53 PM
Sorry mate, 10 to 20% is valid for weight (pallet) loaded breather valves and emergency vents.
#14
Posted 06 July 2009 - 03:33 PM
The literature is copyrighted in 2009. How long has this technology been on the market? First time I'm seeing it. Any idea how much extra it costs over standard vent units?
#15
Posted 06 July 2009 - 07:10 PM
Might I suggest some caution, while recognizing the caveat by latexman.
First, the reseat pressure of some vents is abominable, and you need to confirm with the vendor. Some vendors will not know or reveal it. There are other vents on the market that can achieve full open at either 10 or 20% o.p. by using safety valve technology, i.e. huddling chambers.
Basically, you need to find out as much as possible as you can about the manufacturers characteristics. You may decide that the more expensive will be best. I recently found, that the lesser pressure build up to full flow, was not only desirable, but was the only way to stay within the MAWP.
Last, don't forget that most blanketing valves are simple PRV's with droop.
All of this is why I suggested that the designer use simple bar charts to visualize the overall problem, and to see where changes to set points would be useful.
#16
Posted 07 July 2009 - 12:44 AM
Emergency Relief set at 1/2 MAWP
Thanks a lot Latexman.
Looking above two equal values,then you will consider possible dead band inbetween?
In your typical example,set point of pressure regulating valve (if any,e.g. for blanketing) would be below 1/4 MAWP (around 1/8 MAWP as per your defined criteria?).
Am i right?
Hope my above questions have not been forgotten.
#17
Posted 07 July 2009 - 07:29 AM
You must have skipped "Like I said these are rough guidelines. I get my first pass with these guidelines, then I "tweak" it to reality where set pressures are whole numbers and not fractions. I like to have more "operating latitude" between the Normal Relief fully open and the Emergency Relief set pressure to minimize the leakage out the Emergency Relief."
Yes, 1/8 MAWP is in the right direction. A thorough understanding of all the critical pressures (MAWV, MAWP, set pressures, reseating pressures, "leak point" pressures, sizing pressures, etc.) must be understood before assigning the design values
#18
Posted 07 July 2009 - 08:45 AM
I believe you and I are on the same page, and I do not have an objection to your practice, especially as you point out that it is a first step or rough guideline.
My point is that there are operating characteristics of the mechanical equipment that must be considered in the final step, and this information is often not available in the catalog or sometimes even made available upon request. Reseat is a good example.
Your comment 'more "operating latitude" ' is especially valuable in this respect. Even more so when the system is aged and the seats are not performing at the efficiency they did at factory final test. (I spent 30+ years working for valve manufacturers, before entering consulting.)
Anyway, fallah, you should have all the information that you require to proceed with your work. It now is up to you and your good engineering judgment.
#19
Posted 08 July 2009 - 12:49 PM
#20
Posted 08 July 2009 - 01:40 PM
I recommended them to a client and he was very impressed, even considering the higher cost, because of the ability to reduce the pressure buildup.
#21
Posted 08 July 2009 - 03:30 PM
#22
Posted 08 July 2009 - 03:39 PM
Thanks very much.
Similar Topics
Dead LegStarted by Guest_Muhammad Hamid Khan_* , 26 Nov 2022 |
|
![]() |
||
Actace Band Sound Pressure From SilencerStarted by Guest_shvet1_* , 21 May 2020 |
|
![]() |
||
![]() Dead Leg At High Steam (Hs Line)Started by Guest_irsanagustian_* , 07 Aug 2018 |
|
![]() |
||
Optimum Outlet Temperature Of Cold UtilityStarted by Guest_rofice_* , 27 Nov 2017 |
|
![]() |
||
Dead Heading A Centrifugal PumpStarted by Guest_Mattgreen286_* , 08 Nov 2016 |
|
![]()
|