|
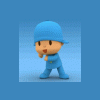
He - Overdesign Purpose
#1
Posted 06 January 2010 - 01:01 AM
as for shell & tube for example, why sometimes clients want to add margin on the surface area? planning to use higher flow rate next time? i will say it may not. adding margin into the surface area will make the HE larger but lesser or near-to-zero margin still make it works. can anybody explain?
#2
Posted 07 January 2010 - 04:16 PM
as for shell & tube for example, why sometimes clients want to add margin on the surface area? planning to use higher flow rate next time? i will say it may not. adding margin into the surface area will make the HE larger but lesser or near-to-zero margin still make it works. can anybody explain?
Most of sizes coming out of computation have some degree of uncertainty, so the client tries to cover it through margins to be on the safe side.
This will not increase e.g temperature of heated fluid out, if there is some temperature control on the exchanger.
It is true that heat design of the exchangers is usually precise enough today, yet physical properties or fouling factors (for example) can have a rather important uncertainty. The client may not know them well and adds a margin, trying to be on the safe side. Same for the operating conditions.
Of course checking the exchanger offered (as well as its requested margin) is another cup of tea, but even this check has some uncertainty.
This margin is more apparent in structural mechanics, where the strength of materials is statistical, hence "safety factors" can be as high as 4 times failure strength. Moreover looking at several heat transfer relations in graphic form, one can see points far enough from the curve, indicating uncertainties to be covered. Client may want to be more conservative than manufacturer in this coverage.
#3
Posted 08 January 2010 - 08:20 AM
HE overdesign as per my understanding more to manufacturer benefit and less to client and more depend on services requirement.
Thanks
Toor
#4
Posted 08 January 2010 - 08:45 AM
Thanks for the information. YES, sometimes client unable to give us the correct n sufficient input for design computation. because of this, deviation may exist.
While for Toor, "client" term has a wide understanding. there are a lot of hands in this industry, even just for a small project.

#5
Posted 08 January 2010 - 11:13 AM
Even though there are several people involved and various other reasons from client..manufacturer..if we consider this from the process point of view the feed temperature,pressure and composition in most of the cases are not constant and in a plant there might be many HXs preceding the one we are taking about(example) and their performances may not be up to the mark. All these would effect the exchanger performance,when added up the error might be big enough such that if we have 10-15% extra heat transfer area to reach the particulat temp, is worth.I think this is the reason we normally add extra area.Thanks.

#6
Posted 08 January 2010 - 04:12 PM
Design of any process equipment is dependent on the physical properties, especially the design of an H-E totally depends on H-T properties like Cp, K, and viscosity. Simulators like Aspen plus and Hysis predicts these properties within an certain accuracy. Again the simulators depends on the user and the input data to it, For instance, temperature and pressure profile of the process will change these properties for sure.. For gases lower pressure means lower density which in turn equate to lower H-T coefficient.
take an example of an overhead distillation column condenser, extra surface area is recomended during abnormal operation and for getting higher purity when the user will increase the reflux ratio. The condenser will see higher vapour load at higher RR.
Many big oil companies I've worked with, have sort of standard developed that for all the H-E's an additional 10-20 % additioanl surface area required.
Hope this throws some more light on the initial question asked by Fatima
ARAZA
#7
Posted 08 January 2010 - 10:22 PM
thanks for good feedback. i got a clear picture from all of you.

#8
Posted 09 January 2010 - 05:46 AM
Hi Kkala,
HE overdesign as per my understanding more to manufacturer benefit and less to client...
This can be the case when we purchase exchangers from manufacturer's catalogues; over design will probably push to higher size.
In case that we purchase an exchanger based on our requirements (through a Process data sheet), the manufacturer makes the design and specifies surface area. Excessive requirements can result in higher size, but manufacturer is not responsible. However we should be able to check manufacturer's design to see whether it can comply with our written requirements.
This check can be "easier said than done"; a lot of small companies do not have suitable software, and probably none checks offered exchanger by hand today (including me).Manufacturer's reliability and fame are important in this case. Yet a critical look can help, extended on both our documents and manufacturer's documents.
I remember the case of an LPG vaporizer in the past, where fouling factor values followed by "Btu/(hr ft2 0F)" as units in the data sheet, while the correct was "kcal/(hr m2 0C)" which is 4.9 times higher. This resulted in about three times more heating surface area. Only one bidder understood our mistake and offered a "small" vaporizer, without a warning (he should have made a note to us).
#9
Posted 10 January 2010 - 09:43 PM
any issue regarding the HE performance, if it comes from manufacturer or even client, each will be responsible. we as manufacturer shall have warranty on HE designed. to avoid problem comes from unit error, client & manufacturer should always practising cross checking on process data sheet. of course, everyone does mistakes but here when it comes to overspending expenses, mistakes unaccepted.
Similar Topics
Purpose Of Natural Gas Saturator?Started by Guest_daraj_* , 06 Aug 2023 |
|
![]() |
||
Overdesign In Htri Simulation ModeStarted by Guest_Aref-Gh_* , 26 Jan 2022 |
|
![]() |
||
![]() Purpose Of Condensate Pot In Steam ReboilersStarted by Guest_Venkat @89_* , 23 Sep 2019 |
|
![]() |
||
![]() How To Setup A Bench Size Chemical Process For Control Purpose?Started by Guest_ahmedabdalrahiem_* , 14 Sep 2020 |
|
![]() |
||
Concept And Purpose Of Overflash Pump In Distillation ColumnStarted by Guest_Venkat @89_* , 10 Apr 2020 |
|
![]() |