I am designing a sulfur removal system as a requirement for my process design class. I have decided to utilize calcium acetate to remove H2S from gas feed stream. Majority of the papers and research conducted was performed using a DTR (drop tube reactor). I am to scale up the process. My question is what kind of reactor can I use at the large scale? Please help. All feedback is much appreciated.
|
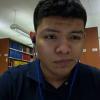
Industrial Sulfur Removal Process Systems
#1
Posted 02 April 2014 - 11:52 PM
#2
Posted 03 April 2014 - 12:03 AM
reaction in a gas-solid reaction.
#3
Posted 03 April 2014 - 09:27 AM
Jorge:
Based on what you state, you are not “scaling up” the laboratory-scale apparatus used to show the removal of H2S with sprayed calcium acetate (or Calcium magnesium acetate). The use of a “drop tube reactor” is a laboratory operation. It is not a pilot plant – which is a working, small-scaled, process that can indeed be scaled upwards.
Professor William Nimmo at the University of Leeds has studied the removal of H2S by Spray-Calcined Calcium Acetate. He has investigated the use of calcium acetate by experimental studies using drop tube (DTR) and fixed-bed flow reactors. What has been achieved is academic information that could lead to the development of a practical, industrial-scale process. However, without knowing all the academic findings – such as all chemical reactions (if such take place), reaction rates, efficiencies, exotherm or endothem identifications, pressures, temperatures, etc. etc. – one can’t visualize what the professor means by spray operation or much less by “fixed-bed flow reactor”.
There are such things as spray operations and fixed beds, but the specifics have to be made known in order to develop a working, practical industrial process. For example, the generic term is “fixed bed”. From that point on, you can have a fixed, packed bed of catalyst (or reactant?) in a vessel; or you can have a vessel very much like a vertical heat exchanger with the tubes packed with catalyst. It makes a big difference on what and how you need to carry out the operation. Without the specific details of how and what is taking place, one can’t recommend any type of configuration of “reactor”. For example, is a catalyst employed? Is there a consumable reaction taking place? If so, then the operation has to be batch-wise in order to replenish the reactants - if the operation is done under pressure.
In short we need more detailed information before commenting or recommending. Perhaps you have that information. If not, you can find the professor’s article at:
http://pubs.acs.org/....1021/ie9900622
#4
Posted 03 April 2014 - 10:22 AM
Thank you for your information.
Similar Topics
Why Superheated Happen In The Crystallisation Process At 60DegcStarted by Guest_HSN202906_* , 08 May 2024 |
|
![]() |
||
Ammonium Sulfate Process SimulationStarted by Guest_amir55261_* , 06 Apr 2024 |
|
![]() |
||
![]() Mtbe Process Flow Diagram Master Thesis.Started by Guest_sayoub_* , 15 Feb 2024 |
|
![]() |
||
Co2 Removal Membranes Between Compressor StagesStarted by Guest_Sinclc_* , 26 Mar 2024 |
|
![]() |
||
Let Down Vessel In Methanol ProcessStarted by Guest_Manue_* , 21 Mar 2024 |
|
![]() |