
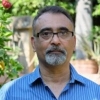





Comparing Liquid And Vapor Heat Transfer Fluid (Diphenyl:diphenyl Oxide) Systems
28 September 2012

One thing common in all the polyester polycondensation plants was the process heating using thermic fluids also known as Heat Transfer Fluids (HTF). While Dupont/Chemtex and Inventa preferred to use a HTF which was an eutectic mixture of Diphenyl (26.5%) and Diphenyl Oxide (73.5%), Zimmer preferred to use a hydrogenated terphenyl as HTF for process heating.
Common trade names for Diphenyl:Diphenyl Oxide mixtures available in the market include Dowtherm-A, Therminol VP-1, Diphyl and Therm S-300 which have equivalent properties.
The hydrogenated terphenyl is available as a commercial HTF by the trade name Therminol-66 or Dowtherm-RP and have equivalent properties.
While Dowtherm-A can be used both in the liquid and vapor phase for heating, Therminol-66 is used only as a liquid phase heating medium. The Atmospheric Boiling Point of Dowtherm-A is 257 deg C and that of Therminol-66 is 359 deg C.
Zimmer technology uses liquid heating preferentially at low pumping pressures and hence they prefer Therminol-66 and its equivalent.
Today's blog entry is about the use of Dowtherm-A and its equivalent for process heating in both vapor and liquid phase and the salient features of each of the type. Let me begin with "Liquid" phase heating.
Liquid Phase Heating:
- Less total equipment, instruments, and controls
- Lower first investment (capital cost)
- Can be used in both heating or cooling mode (for example in polymer coolers)
- No temperature gradient due to pressure drop in supply piping
- Minimal venting requirements (once initial venting is done during system filling and start-up further venting is only required due to long-term build-up of low molecular weight degradation compounds)
- Cold spots are eliminated due to inert gas blanketing or vapor condensate backing up as in a vapor system
- Piping slopes are not required unlike vapor condensate systems except for gravity drain pipes
- Unlike vapor systems, properly designed and installed condensate systems are not required
- No need for desuperheaters as required in vapor sytems
- Higher operating pressures compared to vapor systems creating a greater hazard due to leaks from the system
- Higher operating costs due to continuous and large pumping requirements
- Higher operating inventory of HTF compared to vapor systems
- Larger charge and drain systems due to higher operating inventory
- Greater requirement of safety relief devices compared to vapor systems
Vapor Phase Heating:
- Unmatched for process heating in reactors and autoclaves due to uniform isothermal heating with negligible baffling
- Significantly less circulating fluid required for a given heat load
- Simple pressure control loops can be employed for process heating
- Less total inventory of HTF in the heating system
- Operating costs lower due to absence of large liquid circulation pumps
- Lower operating pressures compared to liquid systems thereby reducing the hazard potential due to leaks
- Smaller charge and drain systems required due to lower operating inventory
- Fewer safety valves required; safety valve containment required only where dictated by process hazards analysis
To conclude, process engineers involved in the selection and design of HTF systems using Dowtherm-A and its equivalent can use the aforementioned general guidelines for deciding the suitability of either liquid heating or vapor heating in their design.
Hoping to have some comments on this blog entry from the members of "Cheresources".
Regards,
Ankur.
Thanks for sharing such information. Actually there may be not anything to comment on since you have put the plusses of each system clearly. Just to make the blog a little lively i will offer my opinion.
The Licensor should be knowing the reason why they want to adopt either of the system knowing well the other system. However i would like to state that:
1. if a fine control of process side temp is required, then liquid system may be better.
2. Vaporisation cycles may lead to more degradation since you are reaching its maxm liquid temp each time. So a degradation rate per tonne of fluid may be compared. Your experience may help to tell this.
3. Even if the liquid system(therminol 66) boiling point is higher, since it is used as liquid, can it be operated at lower temp? If yes then the operating pressure can be reduced. Of course the process requirements must permit the use at lower temp.
Regards,
Milind