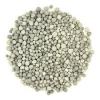
Today's blog entry is in continuation of the blog entry I had made earlier for production of phosphoric acid using the wet process. The phosphoric acid produced by the wet process can be used as a raw material for the production of triple superphosphate.
The process description for Triple Superphosphate is referenced from Kirk-Othmer Encylopedia of Chemical Technology. the material balance is provided as an excel attachment to the blog entry.
Triple (Concentrated) Superphosphate. The first important use of phosphoric acid in fertilizer processing was in the production of triple superphosphate (TSP), sometimes called concentrated superphosphate. Basically, the production process for this material is the same as that for normal superphosphate, except that the reactants are phosphate rock and phosphoric acid instead of phosphate rock and sulfuric acid. The phosphoric acid, like sulfuric acid, solubilizes the rock and, in addition, contributes its own content of soluble phosphorus. The result is triple superphosphate of 45- 47% P2O5 content as compared to 16- 20% P2O5 in normal superphosphate. Although triple superphosphate has been known almost as long as normal
superphosphate, it did not reach commercial importance until. the late 1940s, when commercial supply of acid became available.
Simplicity of production, high analysis, and excellent agronomic quality are reasons for the sustained high production and consumption of TSP. A contributing factor is that manufacture of the triple superphosphate has been an outlet for so-called sludge acid, the highly impure phosphoric acid obtained as a by-product of normal acid purification.
Chemistry and Properties: TSP is essentially impure monocalcium phosphate monohydrate, Ca(H2PO4)2 ·H20, made by acidulating phosphate rock with phosphoric acid according to:

The complete chemistry of TSP production has been studied and reported in great detail. As in the production of NSP also known as Single Superphosphate (SSP) there are also reactions with impurity minerals. The range of constituents in commercial TSP from wet-process acid and phosphate rocks are typically: Ca(H2PO4 )2.H2O, 63-73%; CaSO4, 3- 6%; CaHPO4 and Fe and Al phosphates, 13- 18%; silica, fluoro silicates, unreacted rock, and organic matter, 5-10%; and free moisture, 1-4%. The average citrate solubility of the P2O5 in best quality TSP is 98-99%, but products with citrate solubility values a few percentage points lower are not uncommon. The P205 citrate solubility of TSP made by a quick-cure process is a ca 96%. Other common properties of TSP are bulk density, non-granular, 879 kg/m3; granular, 1040-1200 kg/m3; and critical relative humidity at 30°C, 94%.
Production Technology: Phosphate rock and wet-process phosphoric acid are the only raw materials required for manufacturing TSP. The grade of rock can be a little lower than that needed for NSP production. Over the years, a large number of process modifications, both batch and continuous, have been used. For the production of nongranular TSP, 52-54% P2O5 acid is used without dilution or heating. The P2O5:CaO mole ratio, including the P2O5 in the rock, is 0.92-0.95. The rock is ground to 70% <74.urn (200 mesh). Pile curing for a few weeks is typical, as for NSP.
Granular TSP (-6 + 16 mesh (1.19 to 3.35 mm dia)) is preferred for direct application and is used in bulk blend fertilizers. A widely used slurry granulation process is the Dorr-Oliver process. The ground rock is mixed with 38-49% P2O5 acid in a series of reaction vessels. Slurry from the reaction train then is mixed with a large proportion of recycled undersize granules and crushed oversize in either a pugmill or drum granulator. The granules are dried and screened. The product-size material is about 1 part in 13, thus the recycle ratio is 12:1. Other processes involve granulation of previously prepared nongranular TSP.
Economics: In contrast to NSP, the high nutrient content of TSP makes shipment of the finished product preferable to shipping of the raw materials. Plants, therefore, are located at or near the rock source. The phosphoric acid used, and the sulfuric acid required for its manufacture, usually are produced at the site of the TSP plant. As in the case of NSF, the cost of raw materials accounts for more than 90% of the total cost. Most of this is the cost of acid.
Since about 1968, triple superphosphate has been far outdistanced by Diammonium Phosphate as the principal phosphate fertilizer, both in the United States and worldwide. However, production of triple superphosphate is expected to persist at a moderate level for two reasons: (1) at the location of a phosphoric acid-diammonium phosphate complex, production of triple superphosphate is a convenient way of using sludge acid that is too impure for diammonium phosphate production; and (2) the absence of nitrogen in triple superphosphate makes it the preferred source of phosphorus for the no-nitrogen bulk-blend fertilizers that frequently are prescribed for leguminous crops such as soy beans, alfalfa, and clover.
The above paragraphs are edited from Kirk-Othmer Encyclopedia of Chemical Technology.
Also an excel workbook is attached providing some material balance calculations for Triple Superphosphate.
Comments and observations on this blog article are welcome.
Regards,
Ankur
Attached Files
-
TSP_Production_Flowsheet_and_Calcs.xlsx (193.14KB)
downloads: 3801