|
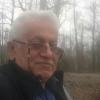
Vertical Can Type Pump
#1
Posted 21 September 2011 - 01:34 PM
Thank in advance
#2
Posted 22 September 2011 - 01:04 AM
The main advantages of vertical can pumps are lower fixed cost and providing additional NPSH, because the first stage impeller is located below floor level in the relevant can.
Fallah
#3
Posted 22 September 2011 - 05:22 AM
Another reason for selecting vertical pumps (in some local refineries) is limited area available. This can occur e.g. in a group of three naphtha pumps. In this case (where NPSHr is same for horizontal or vertical pumps) vertical pumps are considered of higher fixed cost.
Vertical pumps have also other disadvantages: They reqire elevation by crane and transport to shop for almost all maintenance works. They may not have a possibility of horizontal pumps (sold at much higher numbers), e.g. we would hardly find a vertical fuel oil / tar pump with steam jacket on the casing.
#4
Posted 22 September 2011 - 06:24 AM
Vertical multistage pumps met for liquid NH3 or LPG service were expensive items; but horizontal pums could not comply with NPSH required.
Another reason for selecting vertical pumps (in some local refineries) is limited area available. This can occur e.g. in a group of three naphtha pumps. In this case (where NPSHr is same for horizontal or vertical pumps) vertical pumps are considered of higher fixed cost.
Vertical pumps have also other disadvantages: They reqire elevation by crane and transport to shop for almost all maintenance works. They may not have a possibility of horizontal pumps (sold at much higher numbers), e.g. we would hardly find a vertical fuel oil / tar pump with steam jacket on the casing.
Note: Indicative example of horizontal / vertical pump pricing in the attached file "pumps.xls". Expected price difference between horizontal & vertical centrifugal pumps.
Edit note: Same text as in previous post by kkala, with addition of attached "pumps.xls". Previous post would have been deleted after this, but now it should remain due to the negative feedback received. Pravin1510 is kindly requested to clarify reasons of negative feedback mentioned.
Attached Files
Edited by kkala, 22 September 2011 - 06:50 AM.
#5
Posted 22 September 2011 - 09:28 AM
#6
Posted 22 September 2011 - 01:25 PM
My impression is that for a given flow & head, horizontal (centrifugal) pumps have lower fixed (capital) cost than vertical pumps in most of the cases. But this is reversed as NPSH requirement gets lower and lower. Below a limit of NPSH required (high suction specific speed, say 13500), horizontal pumps would not be found in the market . Only vertical pumps would do the task.
Vertical multistage pumps met for liquid NH3 or LPG service were expensive items; but horizontal pums could not comply with NPSH required.
Another reason for selecting vertical pumps (in some local refineries) is limited area available. This can occur e.g. in a group of three naphtha pumps. In this case (where NPSHr is same for horizontal or vertical pumps) vertical pumps are considered of higher fixed cost.
Vertical pumps have also other disadvantages: They reqire elevation by crane and transport to shop for almost all maintenance works. They may not have a possibility of horizontal pumps (sold at much higher numbers), e.g. we would hardly find a vertical fuel oil / tar pump with steam jacket on the casing.
Note: Indicative example of horizontal / vertical pump pricing in the attached file "pumps.xls". Expected price difference between horizontal & vertical centrifugal pumps.
Edit note: Same text as in previous post by kkala, with addition of attached "pumps.xls". Previous post would have been deleted after this, but now it should remain due to the negative feedback received. Pravin1510 is kindly requested to clarify reasons of negative feedback mentioned.
What is the rule of thumb based on your experience for available NPSH of the pump that below that value horizontal pump is not available at market and vertical pump to be used?
#7
Posted 14 October 2011 - 04:20 PM
The easy answer (given to me by Mechanical Department) is that this depends on the specific pump requirements, which can be the base for a relevant market research. But actually a preliminary estimate based on suction specific speed (NSS, rpm*SQRT(gpm)/(NPSHr)3/4) can be made, which has to be verified through a supplier pump extended database.What is the rule of thumb based on your experience for available NPSH of the pump that below that value horizontal pump is not available at market and vertical pump to be used?
Horizontal centrifugal pumps have NSS between 6000 - 12000 (higher means lower NPSHr) based on best efficiency point http://www.waterworl...ific-speed.html. NSS=10500 could be assumed as maximum practical value often met (but actually this varies). Attached "NPSH.xls" is an estimate of NPSHr in function of flow for horizontal pumps, based on NSS=10500. So this is more or less minimum expected NPSHr for horizontal centrifugal pumps, requirements for lower NPSHr have to be satisfied by vertical centrifugal pumps. It is noted that NPSHr strongly depends on rotational speed, so an estimate of pump RPM should be made in advance (rather easy, unless power is transmitted by pulleys).
Nevertheless this is a rough guideline that may not be valid in some cases, especially if pump head exceeds 200 ft (61 m), as concluded from an old practice. If experience in Process or Mechanical Dept cannot assess the result, a search in a supplier database has to be made for this purpose.
For instance, consider the case http://www.cheresour...__fromsearch__1, where a new horizontal centrifugal pump of 35 m3/h and 238 m, with practically minimum NPSHr, had to be specified. Using the pump selection tool of www.flowserve.com (or of another supplier) and searching for API 610 (10th ed) pumps, we can find numerous such pumps in the data base for NPSHr=1.8 m (5.9 ft), e.g. ERPN 65-400 or PHL 40.10.08 35Y; but no pump having NPSHr=0.9 m (3 ft). Yet first case corresponds to NSS=9500 at 2900 RPM (there is such a pump) and second case to NSS=8000 at 1450 RPM ( such a pump was not found). According to "NPSH.xls" both cases represent real horizontal pumps (not true), on the other hand required pump head is higher than 61 m.
But why not go directly to pump data base and avoid the estimate based on NSS? Better to have a quick preliminary NPSHr estimate at the beginning to avoid misunderstanding; it is not easy to interpret the pump data base; apart from NPSHr, the suitable pump must satisfy several other criteria to be assessed rather by Mechanical Dept, or in cooperation (e.g. "distance" from best efficiency point, RPM, diffuser, etc). Process could do the NSS "guess" before this.
Above procedure is not part of a practice and comments would help its improvement. Following additional notes could be also useful.
1. Vertical pumps have lower NPSH compared to horizontal (both centrifugal), if datum is considered as the centerline of their above ground inlet nozzle. Actually vertical pumps place their (first) impeller lower than ground, thus reducing NPSHr corresponding to their above ground inlet nozzle (see also explanation by fallah).
2. NSS statistically increases with capacity increase, that is impellers are better machined in bigger pumps.
3. Multistage pumps can be assumed of same NSS for each impeller, which is the NSS of the pump. Efficiency is improved by multiple stages, http://www.waterworl...fic-speed.html .
4. NSS is valid for best efficiency point (BEF). When we specify a new pump and try to estimate NPSHr through NSS, we do not yet know (BEF), but use design requirements. These are not likely to be far from BEF, and NSS limit of 10500 is a bit reduced compared to 12000.
Attached Files
Edited by kkala, 15 October 2011 - 01:23 PM.
#8
Posted 15 October 2011 - 01:11 AM
One of major drawback in apply canned motor style sealless pumps to refinery services has been the lack of larger than 150 hp motor. Even though larger canned motor s have been advertised, they were not considered commercially viable due their cost and lack of operating experience.
#9
Posted 13 November 2011 - 10:34 AM
Pravin1510 has not been active (*) in the forum since the time of placing the negative feedback on 22 Sep 2011. Probability for explanations seems quite low now, however post on vertical pumps (22 Sep 11) represents my real experience.....Previous post would have been deleted after this, but now it should remain due to the negative feedback received. Pravin1510 is kindly requested to clarify reasons of negative feedback mentioned.
Following supplementary notes to the subject may be worthy of consideration.
1. Summary from a local practice: Where NPSHa is extremely low and usual horizontal centrifugal pump is inapplicable, installation of a vertical incased pump is indicated. This pump is buried (or placed in a pit), while nozzles and driver is above grade. Taking the suction nozzle centerline as datum, a NPSHa value greater than zero is required. Indicative minimum values are 0.15 m for 30 m3/h flow rate, 0.3 m for 300 m3/h, 0.5 m for 700 m3/h, 0.6 m for 2000 m3/h.
2. Probably above aims at vertical pumps of practically reasonable cost. Even lower NPSHa than these values could be obtained. The deeper the pump is buried the lower the NPSHa, which is opinion of local Mechanical Dept too.
But can this sufficiently explain the minimum recommended NPSHa values of paragraph 1? Advice would be appreciated.
3. When vertical pumps are specified for end of curve operation, data sheet should clarify whether this requirement concerns NPSHa too, taking into account that pump NPSHa is specified at liquid minimum level (LLL or LLLL).
Once we specified offsite vertical pumps of low NPSH for volatile petroleum products, required to operate at end of curve. This concerned motor, not NPSHa, but was not well clarified. Then we were informed that Vendors offered unnaturally long pumps to cover increased NPSH requirements at end of curve. This would have caused delay, if Project had not been canceled.
(*) Editing note 20 Oct 2012: Pravin1510 has not been active from Sep 12, 2011 (when negative feedback was placed) till today,
Edited by kkala, 20 October 2012 - 04:22 AM.
Similar Topics
Positive Displacement PumpStarted by Guest_Selvakannan_* , 31 Jul 2025 |
|
![]() |
||
Steam On Shell Side Of A Vertical HexStarted by Guest_Lyne_* , 09 Jul 2025 |
|
![]() |
||
Kitchen Stove Burner TypeStarted by Guest_Vegeta_* , 27 Jun 2025 |
|
![]() |
||
Levels For Kettle Type ReboilerStarted by Guest_RajD_* , 04 Apr 2025 |
|
![]() |
||
Selection Type Of Heater For Refrigerated PropaneStarted by Guest_livetolove003_* , 07 May 2025 |
|
![]() |