|
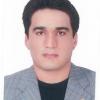
By-Pass Line For Psv
#26
Posted 02 February 2012 - 07:11 AM
Exclamation seems to be describing a plant which does not have any of the safety features which you mention. That is scary, either because this is a real plant, or because he doesn't understand the actions which you correctly describe. He seems to think that the only protective action is for the poor old operator to risk his life fiddling with a manual valve.
In 1989, the Piper Alpha oil platform in the North Sea was destroyed by a catastrophic fire, which killed 163 men.
The first cause of this was someone had removed a PSV from a pump discharge, replacing with a blind flange, and had not removed the pump from service. When the shift changed, the pump was started, and LPG sprayed into the module, starting a fire.
There were a number of other factors in the escalation of the disaster, in particular, the automatic start of the fire water pumps had been disabled because there was a diver working near the pump intakes. When the fire started, nobody knew this, and everything filled with smoke. The operators could have started the fire pumps but did not because they could not get to the local start switch in the smoke and darkness.. Hence, don't rely on the operator in an emergency.
The operator may be injured, or uninformed, or running away....
Would your risk based decision making have identified this scenario? Or would those men have still ended up dead?
Paul
#27
Posted 02 February 2012 - 07:14 PM
2. The Piper Alpha Incidents and not to mentioned others like Bhopal, was the trigger point for the serious application of safety methods such as HAZOPS.
3. Piper Alpha is a good example of facilities that was not HAZOPS and we always cited Piper Alpha in HAZOPS trainng as an example where HAZOPS could have prevented the incidents.
4. LOPA was introduced lately as an extension to HAZOPS. and SIS was introduced to add another layer of protection.
5. For any work that to be carried out, risk assessment should be done first so that we fully understand the risk involved. Any decision should be based on the risk assessment. This is the basic concept behind Risk Based Decision Making.
6. If the risk is unacceptable, then efforts should be made to reduce the risk by installing additional layer of protection.
7. If, for example the only layer of protection is PSV, then one or more layer of protection should be in place before the PSV is taken out for service.
8. With other layers of protection, the risk should be low enough for maintenance of PSV on stream.
9 The point I want to make here is that, if we understand the risk involved and necessary preventive mesures are in place, there is no reason for not taking PSV out of service on stream.
10. Engineers should think outside their "engineering box". We have business to run. Installing additional protective layers can be justified immediately by the loss of production due to shutdown for repairing leaking PSV.
11. If we understand the proablity theory, then we should be able to figure out the risk reduction factor for each layer of protection.
12. If any of you, process engineers, are not yet familiar with Process Safety Management (PSM) it is about time for you to start learning and apply the concept in your workplace.
Edited by S.AHMAD, 02 February 2012 - 07:33 PM.
#28
Posted 03 February 2012 - 05:57 AM
I agree completely wiith your points 3 thru 8. I repeat, however, that the practice indicated in your point 9 is not allowed by many international oil companies as shown in their standards. The cost of installing a spare relief valve is tiny, and saving that cost would not be justified by the increased risk. Most companies have enshrined the principle of ALARP (As Low As Reasonably Practical) into their corporate safety policies. This principle requires risk exposure to be reduced not just to the corporate threshold limit, but below that, until the additional cost becomes disproprtionate as defined in the standards. This has to be demonstrated in ALARP reports (I have written some).
I have attended many HAZOPs. If the right people are attending, with an experienced chairman, they are very useful in identifying hazards and making improvements. However, too often they can become an empty ritual to pacify the client with too little time allowed, and important issues can be missed or false problems identified.
I am also familiar with SIL assessments, risk matrices, bow-tie reviews, QRA, etc etc. All these techniques are about identifying and reducing risk.
In the years since Piper Alpha, improved safety and reduction of risk exposure have been recognised by the oil and gas business (at least among those I have worked with) as not only a civilised human imperative, but also good business policy. Operations are more efficient and thus more profitable in a well-designed, well-operated and well-managed plant. No accident is acceptable.
Paul
Edited by paulhorth, 03 February 2012 - 05:59 AM.
#29
Posted 04 February 2012 - 04:05 AM
My intention of saying lets put standards aside was to set a engineering challenge and think out side the box.
i think some times debate becomes rather personnel with every engineer striving to prove himself right. Engineering should be flexible and should have a broader view.
by the way, I am a design engineer with commissioning experience and some real good multi tasked experiences and i often love to put standards at question, since they are not ultimate and will keep change for the better.
No offence intended:
#30
Posted 05 February 2012 - 12:08 AM
2. We still need to use our judgment in applying the phrase “reasonably practicable”
3. The decision factor is the cost benefit analysis (CBA). Where the incremental cost is compared with the benefits gained from the incremental cost. If the cost of benefits is no longer justifiable. Then we can say that we have reached “ALARP”.
4. Fullstop.
#31
Posted 22 March 2012 - 02:48 AM
why in some case you dont have any bypass on some PSV?
but in some case (fire case) for reactor regeneration you need put spool against the PSV for regeneration and after that operation you put PSV and put the reactor in operation mode.if you have bypass you dont have hard case.
but in basis of design in us plant wrote dont put bypass onPSV in fire case.but you see they put on that cond. !!!
#32
Posted 22 March 2012 - 03:12 AM
1. As far as I am aware of, there is no codes or standards that prohibit the installation of bypass for PSV. What available are good practices by individual company.
2. Bypass is normally provided to facilitate on-stream maintenance of the PSV, that is without shutting down the unit.
3. Bypass is also used for operational purpose, like in your case. Other example is for gas freeing (purging) the vessel for maintenance/shutdown.
4. PSV for ONLY FIRE CASE (no other credible emergency scenarios), bypass is not necessary and if installed it serves for no purpose other than operational requirements.
#33
Posted 22 March 2012 - 01:34 PM
hi sir
why in some case you dont have any bypass on some PSV?
but in some case (fire case) for reactor regeneration you need put spool against the PSV for regeneration and after that operation you put PSV and put the reactor in operation mode.if you have bypass you dont have hard case.
but in basis of design in us plant wrote dont put bypass onPSV in fire case.but you see they put on that cond. !!!
Ghadyanlou,
Project spec would specify the by pass requirement across a PSV either in fire case or another.
As in the project i am involved all PSV's should have by pass lines mostly for maintenance purpose.
Fallah
#34
Posted 23 March 2012 - 03:03 AM
in design criteria in us document wrote you dont allow for fire case or high pressure .
i saw in some case bypass is not design for PSV .but on this plant you can find many PSVs that have bypass.
kind regards
#35
Posted 24 March 2012 - 07:25 AM
This week I have been working on a design verification for a major middle east oil company client, and their design standards include, as expected, exactly this prohibition.
The purpose of the bypass is NOT to allow removal of the PSV. Don't think of it as a PSV bypass, it is a connection from the vessel to the flare to allow maintenance purging when the vessel is out of service.
Think about it: How could a PSV bypass be used, if you remove the PSV? If it is left open then the vessel is not under pressure. If it is closed, what the hell is the operator expected to do in an emergency? Climb up the vessel during a fire and try to open the bypass? That's ridiculous.
Paul
#36
Posted 25 March 2012 - 01:10 AM
Based on this fact that a single PSV mostly would be applied in the situations that only fire case is applicable (the spare would be stored in warehouse), agreed with the most of your points, other than two as follows:
1-Because the PSV fire case (single) dosen't comply a process function too, can be momentarily isolated for maintenance while the relevant vessel is in service.
2-Neither the PSV itself nor its by pass valve wouldn't protect the relevant vessel in most fire cases, also due to the fact that the sizes of most PSV's by pass lines are 2", in any case (PSV being in service or not) no need to operator action on opening the by pass valve during a fire case.
Fallah
Edited by fallah, 25 March 2012 - 01:11 AM.
#37
Posted 26 March 2012 - 08:51 AM
#38
Posted 12 July 2012 - 05:14 AM
Then after removing the PSV, blind flange may be provided at PSV flange and circuit may be made available for depressuring the upstream segment thru bypass valve.
Similar Topics
Ammonia Line Vapor GenerationStarted by Guest_simadri_* , 07 Apr 2025 |
|
![]() |
||
![]() Flow Through Normally No Flow LineStarted by Guest_iippure_* , 08 Apr 2025 |
|
![]() |
||
Inlet Line Not Free DrainingStarted by Guest_Asifdcet_* , 07 Apr 2025 |
|
![]() |
||
Improving Safety By Re-Routing Priming Vent Line In Centrifugal Pump HStarted by Guest_Srinivas Agastheeswaran_* , 31 Jan 2025 |
|
![]() |
||
Psv On Ko Drum With Flame Arrestor At Flare Vent LineStarted by Guest_Tintin2024_* , 29 Oct 2024 |
|
![]() |