We have problem with flash point of RFCC Main column bottom products as decant oil. Flash point is very low, (47 -52 Deg C, spec 110 degC). We have been operating unit for 4 years. In the first year, the flash point was quite good, but it became worse in the last three years.
Our original designed crude has been in shortage, then we use others crude from Middle East for compensation. Does crude itself takes all the blame to this problem?We tried to adjust operating parameter in Main column bottom to get high DCO flash point but unsucessful..How to explain in this case..
Does anyone have experience of this scenario? Kindly share your experience.
|
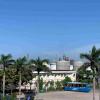
Low Flash Point Of Rfcc Decant Oil
#1
Posted 09 July 2013 - 07:44 PM
#2
Posted 11 July 2013 - 06:24 AM
Do you see the same pattern of lowering flash point all across Main Frac product that's Lt and Heavy naphtha and LCO cuts or is it only happening at bottoms slurry oil ?
#3
Posted 11 July 2013 - 09:36 PM
My LCO and HVN flash point is high. It is around 110oC. I think something wrong at Bed#5 ( slurry bottom).We tried to reduce Slurry PA return reach minimum and adjusted bottom temperature but it have no meaning..
#4
Posted 23 August 2013 - 10:49 AM
Something is wrong with the column hardware ,its not possible to have a higher flash point of upper cuts as compared to bottom cuts.Can you please share with us column PFD and column datasheet along with a sketch.
#5
Posted 24 August 2013 - 12:10 AM
Hoang,
just for brainstorming....
1) It could be a problem of stripping.
2) The given Flash points of HVN (and LCO) are not realistic.
3) Is it possible to see the ASTM curves of BTM, LCO, HVN?
4) Have you made check runs and relevant simulations to try to understand the situation?
5) Could you provide some data (flowrates, temperatures) relvant to the tower operation?
Good luck!
#6
Posted 26 August 2013 - 02:11 AM
Dear Mr. Tri,
Long time no see, do your remember me? I'm Mr. Song in SK.
Regarding your problem, please check the feed bypass valve, I read the some topic with this trouble. If the feed bypass valved is leaked. SLO flash point can be affected because the feed will go to Main column directly.
And also, the flash point can be changed if you change the crude oil. Our flash point is normally, 60 ~ 70C.
Good Luck
#7
Posted 26 August 2013 - 07:26 AM
Dear Mr gegio
We are using HVN tripper with reboiler to remove light component and LCO tripper with LP steam tripping. The flash point of LCO is around 100oC. Unfortunately, we can not use LP stripping for SLO because we have water content limt in SLO before going to Slurry separator ( Gulftronic).
I supply some operating data in Column and PID attachement
TIC439: 340oC
TI437: 385 max
TI528: 370 max.
TI441: 250oC
TI440:205oC
TIC443: 355 max
We tried to check run on simulation but didn't find any root cause. also tried to check feed leaking in SLO exchanger circuit and found no leaking.
Regards
Attached Files
Edited by Hoang Tri, 06 September 2013 - 08:47 PM.
#8
Posted 26 August 2013 - 07:36 AM
Dear Mr. Tri,
Long time no see, do your remember me? I'm Mr. Song in SK.
Regarding your problem, please check the feed bypass valve, I read the some topic with this trouble. If the feed bypass valved is leaked. SLO flash point can be affected because the feed will go to Main column directly.
And also, the flash point can be changed if you change the crude oil. Our flash point is normally, 60 ~ 70C.
Good Luck
Dear Mr Song
it's long time to see you. I remember you well. in your reply we checked but didn't find any leaking from feed to SLO and we tried to adjust many operating parameter at bottom to raise up flash point but impossible and we lost benefit by selling DCO lower cost because Flash point is low and sometime we mixed Residue with DCO to meet specification..
Could you give me your email address?
Best regards
#9
Posted 27 August 2013 - 01:50 AM
Hoang,
you should easily understand the data you provided are not enough for any understanding and further elaboration (see post #5 above).
Anyway, it seems very strange to me that a problem like this hasn't solved in 3 years.
good luck
#10
Posted 06 September 2013 - 08:58 PM
Sorry mr geigo for late .Today I attach data file about Main fractionator
Attached Files
#11
Posted 07 September 2013 - 03:12 AM
Hoang,
the above data are a big step ahead but not enough to help you in studying your problem from a "designer" point of view (maybe some operators can give you valuable ideas.....)..
As Himanshu already told you in post #4 you should provide:
- the column PFD;
- the column data sheet.
and, moreover, after a look to the P&ID #310 and your operating data, you should provide too:
- P&IDs 303/4/9/11 (at least);
- the other operating data around the tower (ie not limited to slurry oil, as it is now);
- SG of the various streams;
- characterization (ASTM points, SG...) and operating data (T, P, flow) of feeds to the towers.
#12
Posted 07 September 2013 - 04:10 PM
Data and PID&PFD, Operating parameter
Attached Files
#13
Posted 07 September 2013 - 08:45 PM
Process flow drawing
Attached Files
#14
Posted 08 September 2013 - 04:38 AM
Hi Hoang,
it is a challenging problem, isn't it? ;-)))
I've spent a couple of my Sunday hours to analyze your documentation (I could say this my hobby other than my job).
I didn't see the DCS printouts and you didn't attach any info relevant to the tower (in particular bed #5) but I can preliminary say that, for me as an external observator, there are other 2 unknowns:
- the stream 1 in the PFD, ie Disengaging Effluent from Reaction Section: with its 520°C (from the PFD) it is the one providing the stripping effect on the liquids coming from bed #5; up to now there is no info about its quantity and properties;
- (less important) there could be the possibility that some light components can enter the CLO product stream thru the Slurry Separator X-1504?
If you have additional info about the 3 points above, I think that the qualitative analysis can be concluded.
Not the quantitative one, because there are practically no info available about the characteristics of the feed streams and they are mandatory to prepare a simulation.
Regards
#15
Posted 08 September 2013 - 04:58 AM
the 1st i would like to say thank for your kindly help
Mr gegio, I atactched DCS printouts in operating parameter file and gave enough info about column condition now..
Every thing i asked in the forum which is existing at My refinery, Many ideas gave to us but only theory and tried but failed.i known many experiened man in the forum can help me...!
i asked to take a chance to learn from everybody eventhough what is the result!
1) your request about quantity and property about disengaging effluent, i will ask and send to you later
2)We tried to take SLO sample at upstream and downstream X-1504 and we had same flash point result. That's mean no reason about light component enter the CLO product stream.
Many thanks my friend in the forum..
Edited by Hoang Tri, 08 September 2013 - 05:05 AM.
#17
Posted 18 September 2013 - 05:49 AM
Dear Hoang,
I think the crude oil properties might cause the problem you mentioned. How much is the asphaltenes content in your RFCC feed?
What did you do with the low flashing point DCO ? Blending some from LCO to DCO, right? It might mean the ecomomic loss at the unit.
#18
Posted 20 September 2013 - 10:08 PM
Dear Hoang,
I think the crude oil properties might cause the problem you mentioned. How much is the asphaltenes content in your RFCC feed?
What did you do with the low flashing point DCO ? Blending some from LCO to DCO, right? It might mean the ecomomic loss at the unit.
Dear sir
Could you explain more detail about crude oil properties caused that problem?. Asphaltenes content in our feed is around 0.18% mass. We bended DCO with Residue (feed) to increase DCO flash point. Of course, We had the economic loss during DCO flash point low
Best regards
#19
Posted 25 October 2013 - 08:09 AM
Wainting for next TA internal inspection and modification with bottom steam ring
Similar Topics
![]() Flash Steam Vessel SizingStarted by Guest_JohnFields343_* , 24 Apr 2024 |
|
![]() |
||
Hydrocarbon Dew Point Control UnitStarted by Guest_BabRafiq1_* , 05 Apr 2024 |
|
![]() |
||
Sizing Of Vertical/horizontal Flash DrumStarted by Guest_Mohammad3799_* , 10 Mar 2024 |
|
![]() |
||
Increasing Raw Natural Gas Dew PointStarted by Guest_lowrentstuff_* , 18 Sep 2023 |
|
![]() |
||
Dew Point Margin In Strippers & Fractionation ColumnsStarted by Guest_Venkat @89_* , 05 Sep 2023 |
|
![]() |