|
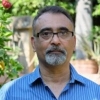
Special Pumps For Lpg Service
#1
Posted 23 June 2008 - 02:23 PM
Are there any special pumps for liquids such as LPG which are having very high vapor pressures at ambient temperatures. What I am trying to find out is if there are special designs which can tolerate a small amount of vapor along with liquid at the suction of the pump without causing cavitation, vibration, premature pump failure and reduced performance and efficiency.
Request learned forum members to provide any links or literature for any such pumps.
Regards,
Ankur
#2
Posted 23 June 2008 - 03:35 PM
I believe you have left out the most important basic data: you are referring to SATURATED LPG and not sub-cooled LPG. This characteristic is what sets LPG applications apart from others - although this is not a big deal nor different from handling hundreds of other similar applications in the processing world - steam condensate, distillation tower bottoms, liquified industrial gases, etc., etc., it is still important to always bear in mind.
The pumps designed specifically to pump LPG are not very different from other pumps. However, their internal clearances are less (in the case of PD pumps) and the materials of construction tend to be different.
The main factors contributing to a successful design and installation of an LPG pump are usually the same: as liberal a NPSHa as you can afford and good fluid flow piping design. Dissolved gases are not a problem when you concentrate on a positive and liveral NPSHa. A good Suction Specific Speed will ensure no cavitation, nil vibration, and prolonged pump operation with good performance and efficiency.
#3
Posted 24 June 2008 - 01:24 AM
For high vapor pressure fluid in ambient temp.(e.g. LPG) we have to provide proper facilities for precooling of the pump and relevant discharge line (and proper location for relief of produced vapor) before start-up.
Regards
#4
Posted 24 June 2008 - 01:14 PM
After due search of the internet I found some very interesting information on pumps used in the LPG industry. Certain facts for LPG pumping are as follows:
1. LPG (propane) has two phenomenas related to boiling:
a. Externally driven boiling which is caused by addition of heat from an externa l source.
b. Internally driven boiling which is caused by lowering of the pressure of the vessel in which
it is stored.
A pump manufacturer called Corken provides special pumps known as sliding vane pumps for LPG service which can tolerate a fair amount of gas in the pump suction. They have published a guide on liquified gas transfer equipment which is a very good reference on pumps, compressors and valves in the LP gas service. It also provides the fundamentals of the phenomena of handling LP gases. Following is the link:
http://www.corken.co...ining/cp226.pdf
I would urge learned members to go through this guide and also share some more experience of LP gas handling on this thread.
Regards,
Ankur.
#5
Posted 24 June 2008 - 02:58 PM
I have pumped LPGs for many years in the past and I never had a situation where there was external boiling. I have never seen or experienced internal boiling.
I also know from experience that NO PRECOOLING of the LPG pump is necessary. And I have never designed for it since I never saw a need for it.
Pumping LPG does not involve complex techniques nor is it rocket science. It is a very simple, dependable operation when designed correctly and operated according to common sense and correct procedures. LPG has been pumped around the world in both developed, developing, and under-developed countries for many years - on a daily basis by operators who have no sophisticated or technical education. Some of my best operators never finished grade school in some of the countries where I worked. And we never had any problems pumping liquefied, saturated gases - especially LPG.
My point here is to expound what I wrote in my first response: obtain a good, liberal pump design with a healthy NPSHa and a well-trained operators who take good care of their operation and you will never have any problems.
#6
Posted 26 June 2008 - 07:27 AM
Generally, for pumping saturated LPG it is common to use a vertical centrífugal pump (canned type). This type of pump increases the NPSHa and solves the problem of internal boiling, if the pipe system is well designed.
For eg:
Flowrate = 1,050 USgpm
Discharge head = 922 ft
NPSHa = 8 ft
We have used a canned vertical centrifugal pump with NPSHr = 5.2 ft without any problem.
Std: API 610 8th edition, 1,750rpm, 7 stages.
I have a drawing and a data sheet of the pump. I don't know if it is allowed to post the brand.
Martin
#7
Posted 27 June 2008 - 01:51 AM
Regards
#8
Posted 01 December 2008 - 06:51 AM
Dear Mr Art,
I personally agree with your above points, but considering propane temp. (around -30 C) our client worries about probable need for precooling and also probability of having two phase flow in discharge line,both in start-up condition. Please kindly help by submitting detailed reasons against client concerns.
Regards
#9
Posted 01 December 2008 - 08:15 AM
My comments on subcooling LPG prior to pumping were based on pumping ambient temperature, saturated LPG. However, I have also pumped saturated LPG at negative temperatures (around -30 C). Additionally, I have pumped numerous liquefied, saturated gases at many temperatures – most of them below ambient. Liquid CO2, liquid CO, Liquid Oxygen, Liquid Nitrogen, Liquid Argon, Liquid Ethylene, LNG, etc.. etc. None of these gave any particular problem(s) beyond the usual expected.
My point here is to stress to everyone who reads this that there is nothing to fear from the fact that the liquid is saturated. Depending on how negative your liquid temperature is and how well you have your system insulated, you should have no problems in moving the liquid from one system to another. I have employed centrifugal, gear, and piston pumps and have routinely pumped liquid oxygen from 5 psig, saturated conditions to 3,000 psig discharge pressure. The principles of vapor pressure, NPSHa, Suction Specific Speed, and Specific Speed, while maintaining 100% liquid-filled suction ports are the same as for sub-cooled water and provide the tested and proven tools to apply to a successful pump installation.
Your clients should be well aware that there is no subcooling involved in pumping tons of LNG per hour from LNG carriers to shore-based terminals as well as from the terminals to the carriers. And yet, this critical operation is done on a routine, and repeatable basis. There are scores of saturated, liquefied gases being pumped without the use of subcooling simply because there is no colder fluid around to do the sub-cooling.
If your client insists on subcooling, then by all means supply subcooling. This certainly only helps to ensure good pumping capability. However, it will also ensure more capital and operating expense. I see no reason for your clients concern about being able to pump saturated LPG at -30 oC. However, I know nothing about the application or the scope of work so I can't comment any more than to say that I can pump saturated LPG at -30 oC just as easily as I can subcooled LPG – if I am left to my engineering design and operation.
#10
Posted 01 December 2008 - 12:10 PM
Dear Art,
Thanks for your fast and useful reply,but i want to know when you were going to start the pump to transfer the saturated LPG at -30 C,did you make the pump and its discharge line precooled (while the LPG was not in subcooled condition) to avoid creation of two phase flow in pump discharge?As per client opinion, if the discharge line is not being precooled ( in this case up to around -30 C) before pump start up,two phase flow and following that pump cavitation could be occured (at least in the beginning of start up).Based on this and also intermittent service of the pump,my client insist on other alternatives to transfer the LPG such as vaporization by electrical heater.
For more information,in my case pump is suction filled by which the LPG would be transferred from a knock-out drum to another sump drum.
Regards
#11
Posted 05 December 2008 - 01:20 AM
#12
Posted 05 December 2008 - 07:53 AM
I think you are missing out on what I have taken for granted as being common engineering design factors when you are dealing with sub-zero, saturated, liquefied gases. For example, it is common knowledge and practice that if you intend to pump a sub-zero, liquefied gas YOU MUST EITHER HAVE A PUMP AND PUMPING SYSTEM EXISTING AT THE SAME (OR COLDER) TEMPERATURE OR YOU MUST PRE-COOL THE SYSTEM PRIOR TO PUMPING. This is the trade-off you have to pay for pumping at the sub-zero temperatures. This is common sense.
I don't understand why you have shifted what was an original topic described by Ankur as "liquids such as LPG which are having very high vapor pressures at ambient temperatures" into a topic of sub-cooled, sub-zero, LPG. The two subjects are entirely of a different nature and require distinct engineering design.
Either your client doesn't understand the principles behind a saturated, sub-cooled liquid LPG medium or you are not communicating exactly what seems to be a problem. In order to pump sub-zero, liquefied LPG you MUST HAVE AND MAINTAIN a pumping system at that same, sub-zero temperature or you will not be successful in transferring 100% of the liquid product. Heat transmission from the surrounding ambient will vaporize the sub-zero liquid and either vapor-lock the pump, create 2-phase flow, or simply cause pump cavitation. That is why I repeat: "My point here is to stress to everyone who reads this that there is nothing to fear from the fact that the liquid is saturated. Depending on how negative your liquid temperature is and how well you have your system insulated, you should have no problems in moving the liquid from one system to another".
It is common sense that if you store and transport your LPG in the pressurized, ambient temperature-saturated state, you have no vaporization or heat transfer/insulation problems. That is precisely why I prefer the storage and transport of the pressurized, saturated variety of LPG.
You ask for comments and my main comments is that you (or your client) should either supply refrigeration to cool down the pumping system if you keep insisting on handling the sub-zero LPG. If you don't want to supply refrigeration, then you are going to have to sacrifice a portion of the sub-zero LPG to cool down the pumping system and subsequently flare the resultant vapors or vent them to the atmosphere – both of which I prefer not to do. But if you or your client insist on sub-zero LPG handling, then you must pay the price.
#13
Posted 05 December 2008 - 11:34 AM
Thanks for your attention/comment.
if i want to sacrifice a portion of the sub-zero LPG (because this is off-spec product and not important to sacrifice) to cool down the intermittent pumping system, can i consider a permanent open by-pass line (between tank and pump discharge) including check valve for precooling the pump and its discharge line? Obviously, if this configuration could be acceptable, pumping system shall be isolated (with cold type) and also the pump should be started a reasonable time after the tank is to be filled (precooling is done).
Any submitted idea would be highly appreciated.
#14
Posted 05 December 2008 - 02:31 PM
Fallah:
I'm not sure if I correctly understand what you propose, but if you have the ability to "sacrifice" some of the sub-zero LPG then I would simply purge out cold, low pressure product out of the pump's circuit by allowing it to flow from the source tank, through the pump's casing and out through a purge valve located downstream in the pump's discharge line. This will cool down everycomponent up to the point where the purge is done. You can do this with the pump not operating and allowing it to cool down to operating temperaure.
Of course, you should cool down every metal component as well as the insulation on the system.
Another way that I have employed where I have a storage tank as source and where I have system vapor refrigeration available is to hard-pipe the purge line back to the vapor space in the storage tank. That way the vapors generated are liquefied and recovered by the tank's refrigeration system.
Similar Topics
![]() Centrifugal PumpsStarted by Guest_panoska_* , 01 Feb 2025 |
|
![]() |
||
![]() Selection Of Type Of Pumps For "negative" Npsha And Solution TStarted by Guest_linda_pro_* , 29 May 2024 |
|
![]() |
||
![]() Valves On Low Pressure Steam ServiceStarted by Guest_Ali4269278331_* , 15 Apr 2024 |
|
![]() |
||
Bringing Back Sponge Absorber To Service EvaluationStarted by Guest_mje03_* , 30 Oct 2023 |
|
![]() |
||
Vibration Of The Pump (Reciprocating Pumps / Plunger Pumps)Started by Guest_vsedhuraman_* , 06 Oct 2023 |
|
![]() |