Hi all,
In my gas processing facility, amine is used to absorb CO2 from the feed gas. Recently, during start-ups, when we commence circulation of amine through the absorber, we get a backflow of amine into the feed gas knock out vessel. The piping from the knockout vessel is elevated almost 2.7m above the inlet into the amine line for the purpose of preventing the possibility of this occurence. The pressure in the 2 vessels are thesame as at the point of introduction of the amine
I've attached pictures showing the orientatton of the 2 vessels and the internals of the bottom of the absorber column.
Does anyone have any experience of this, or any ideas why it may be happening?
regards
Ogeds
|
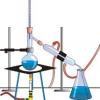
Amine Backflow Incidents During Start-up
Started by Olaniyi, Mar 05 2009 10:08 AM
5 replies to this topic
Share this topic:
#1
Posted 05 March 2009 - 10:08 AM
#2
Posted 05 March 2009 - 08:57 PM
Dear Ogeds,
Where is your picture? The detail of the gas inlet pipe is important.
I think 2 things you should check.
1. The pressure of the gas.
2. The gas inlet pipe design.
John
Where is your picture? The detail of the gas inlet pipe is important.
I think 2 things you should check.
1. The pressure of the gas.
2. The gas inlet pipe design.
John
#3
Posted 07 March 2009 - 11:17 AM
Ogeds:
John is right. I've been waiting for your picture, sketch, drawing, or whatever illustration to make sure I've got the arrangement correct. In the process of waiting, I've put together the enclosed workbook. I believe your absorber arrangement is the one depicted in the #2 PFD illustrated. Am I correct? If so, then we can start to analyze what can go wrong to cause an Amine solution (MEA?) of approximately 15% wt (?) to rise 2.7 meters above the absorber inlet nozzle. Please feel free to mark up and re-draw (if necessary) the PFDs in order to better convey your actual arrangement.
The way the #2 arrangement can spill over an amine solution into the upstream separator is by two methods:
1. If the pressures in both the separator and the absorber are equal, the level of amine solution must be more than 2.7 meters higher than the absorber's inlet nozzle. I doubt the two pressures are equal at the moment of startup and that the amine level is above the inlet nozzle, but I could be wrong. A lot of what happens is primarily due to the startup procedure in practice (or dis-practice!).
2. The level of amine is above the absorber inlet nozzle and the pressure in the inlet separator is kept lower than that in the absorber. This can happen momentarily - that is all that is required. Once again, the startup procedure is what can determine if this is possible or not.
I recommend you study the startup procedure in detail and then participate in an actual startup to ensure that the procedure is religiously followed. Operators - for many reasons - often modify the startup procedures of major equipment. This is OK, as long as the supervising engineer is kept informed and the written procedures are revised accordingly. However, often for reasons of timing and inconvenience, operators forget to notify or to write down what they have changed or modified. This last act can drive you nuts if you are not keeping up with the actual practices by participating in the actual startups. When I was a production manager of several plants, I often dropped in un-invited into normal startups and shutdowns just to make sure that all established procedures were being followed to the letter. It was not that I didn't trust my operators; it is simply a fact that all operators are human beings subject to forgetting and sometimes lazy in communicating information that they have discovered. They are no more different than engineers in that respect.
Please let us know what you find out or keep us informed as to what you have discovered or if you know further details. I look forward to hearing of how you resolve this mystery or what is the cause of the backflow.
Amine_Acid_Gas_Removal_Process.zip 41.67KB
102 downloads
John is right. I've been waiting for your picture, sketch, drawing, or whatever illustration to make sure I've got the arrangement correct. In the process of waiting, I've put together the enclosed workbook. I believe your absorber arrangement is the one depicted in the #2 PFD illustrated. Am I correct? If so, then we can start to analyze what can go wrong to cause an Amine solution (MEA?) of approximately 15% wt (?) to rise 2.7 meters above the absorber inlet nozzle. Please feel free to mark up and re-draw (if necessary) the PFDs in order to better convey your actual arrangement.
The way the #2 arrangement can spill over an amine solution into the upstream separator is by two methods:
1. If the pressures in both the separator and the absorber are equal, the level of amine solution must be more than 2.7 meters higher than the absorber's inlet nozzle. I doubt the two pressures are equal at the moment of startup and that the amine level is above the inlet nozzle, but I could be wrong. A lot of what happens is primarily due to the startup procedure in practice (or dis-practice!).
2. The level of amine is above the absorber inlet nozzle and the pressure in the inlet separator is kept lower than that in the absorber. This can happen momentarily - that is all that is required. Once again, the startup procedure is what can determine if this is possible or not.
I recommend you study the startup procedure in detail and then participate in an actual startup to ensure that the procedure is religiously followed. Operators - for many reasons - often modify the startup procedures of major equipment. This is OK, as long as the supervising engineer is kept informed and the written procedures are revised accordingly. However, often for reasons of timing and inconvenience, operators forget to notify or to write down what they have changed or modified. This last act can drive you nuts if you are not keeping up with the actual practices by participating in the actual startups. When I was a production manager of several plants, I often dropped in un-invited into normal startups and shutdowns just to make sure that all established procedures were being followed to the letter. It was not that I didn't trust my operators; it is simply a fact that all operators are human beings subject to forgetting and sometimes lazy in communicating information that they have discovered. They are no more different than engineers in that respect.
Please let us know what you find out or keep us informed as to what you have discovered or if you know further details. I look forward to hearing of how you resolve this mystery or what is the cause of the backflow.

#4
Posted 07 March 2009 - 06:36 PM
Check the Level and LIC for the column's bottom; make sure the amine flows from the bottom and the level does not reach its maximum during start-up.
If amine floods the inlet gas nozzle, and then start-up pressurization in the system begins with fuel gas or nitrogen to the column, or downstream KO, the hydrostastic pressure difference would backflow the liquid.
The key is again the bottom level. One amine unit design is to put a check valve on top of the inverted U pipe, but do that only as extra protection when there are no problems about the PSV protection for that case.
If amine floods the inlet gas nozzle, and then start-up pressurization in the system begins with fuel gas or nitrogen to the column, or downstream KO, the hydrostastic pressure difference would backflow the liquid.
The key is again the bottom level. One amine unit design is to put a check valve on top of the inverted U pipe, but do that only as extra protection when there are no problems about the PSV protection for that case.
#5
Posted 13 March 2009 - 09:14 AM
Before start of amine circulation pump, keep open (say ~5% of valve, which will flow to the flare) feed gas to amine contactor to avoid any backflow. May be there is no NRV in the feed gas line. We have similar types of experience and overcome by flowing some feed gas to contactorfollowed by flare befor starting amine circulation.
Regards.
#6
Posted 13 March 2009 - 01:52 PM
Dear,
For my own reference, can you tell me whether it is a packed column or a tray column? How do you remove the heat of absorption from the column? Is there any pumparound on this column to remove the heat of absorption?
Thanks,
ARAZA
For my own reference, can you tell me whether it is a packed column or a tray column? How do you remove the heat of absorption from the column? Is there any pumparound on this column to remove the heat of absorption?
Thanks,
ARAZA
Similar Topics
Ammonia Plant Start-Up ProcedureStarted by Guest_Baz_* , 08 Apr 2025 |
|
![]() |
||
![]() Using Feed Compressor For Start-Up Nitrogen CirculationStarted by Guest_behrouzifar_* , 06 Sep 2024 |
|
![]() |
||
Logic For Start Up And Shutdown Of Hp CompressorStarted by Guest_umeshgps_* , 17 Aug 2024 |
|
![]() |
||
![]() Amine(Mdea) StorageStarted by Guest_abdullah1320_* , 17 Jun 2024 |
|
![]() |
||
Dp Drop In Structured Packing Amine Absorber Causing IssuesStarted by Guest_kek12345_* , 10 May 2024 |
|
![]() |