Chemical and Process Engineering Resources
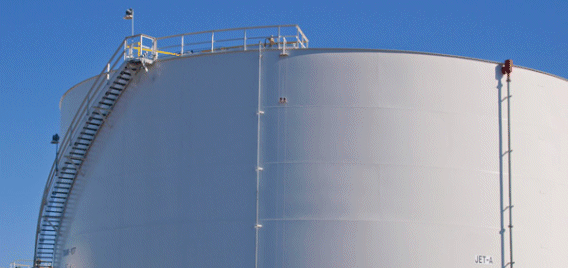
Setpoint Response
When the tank reaches setpoint, tank pressure operating against the sensing regulator diaphragm causes the seat to close. This blocks pilot loading flow and pressure rises to the 10 psi setting. This pressure then operates against the main valve diaphragm, causing the main flow control valve seat to close. Flow to the tank ceases.
At pressures below the setpoint the sensing regulator will throttle, varying pressure in the sensing system and then throttling the main valve. The amount of throttling is proportional to the offset from setpoint. Therefore, as tank pressure rises and approaches the setpoint, the main valve throttles and is closing as the tank reaches setpoint. This maintains accurate setpoints and reduces overshooting.
In addition to a blanketing system, the tank will contain the emergency vent as well as normal pressure and vacuum vents --- all of which must be properly sized for outgassing from pump-in, increases in temperature, drop in barometric pressure, or fire. The vacuum relief provides redundant tank protection for unforeseen conditions, loss of blanketing gas supply or system failure.
![]() |
Figure 2: Sample Operational Stages of Blanketing Process |
The selection of a blanketing pressure is very important. It must be less than the tank's pressure capability, and also should allow some dead-band below the tank vent operating pressure to avoid interaction.
Figure 2 illustrates a tank blanketed to 0.5 inch w.c. having an allowable working pressure of 6 ounces per square inch. A pressure of 0.25 inch w.c. added for shut-off results in a maximum blanketing pressure of 0.75 inch w.c. The tank has a normal pressure breathing vent that starts to open at 1.5 ounces per square inch (2.6 inches w.c.) and is full open at 1.8 ounces per square inch (3.1 inches w.c.).
Further, an emergency vent opens at 3 ounces per square inch (5.2 inches w.c.) and is fully open at 3.5 ounces per square inch (6.1 inches w.c.). There is a dead-band of 2.1 inches w.c. between the two vents. The dead-band between the blanketing system and the normal vent is 2.6 -0.75 = 1.85 inches w.c. The presence of an adequate dead-band will ensure stable operation and avoid unnecessary loss of blanketing gas or product going out an open tank vent.
Proper sizing is important for stable operation. Under-sizing can result in tank pressures dropping well below the setpoint as the main flow control valve struggles to keep up with demand. Over-sizing is less critical. However, taken to an extreme, it can result in unstable operation due to exceeding setpoint.
Summary
A gas blanketing system will effectively contain gases within the vapor space of a tank. Such a system can contain the gas, or protect the tank contents form contact with atmospheric air. It also can maintain the vapor space contents at an oxygen concentration level low enough to prevent ignition of flammable vapors.
The system are simple to use and require little, if any, maintenance. They are capable of blanketing at pressures as low as 0.5 inch w.c., minimizing consumption of blanketing gas.
Nitrogen is the most common blanketing gas, but others are used if compatible with the process. From a virtually endless list of products that qualify for blanketing, those that are volatile as well as those sensitive to contact with moisture or air are all candidates.
Since the original publication date there have been advances in the technology used to provide gas blankets. While this article does not illustrate these, the basics discussed in the article are still valid. Visit www.ostand.com for more articles on tank blanketing.
2 Comments
I dont know how calculated the volumen of a blanketing tank, my problem is calculated the volumen for thermal effect (inbreathing). Grateful for your response.
Is the Nitrogen gas inlet nozzle,should only on the tank roof ?
In my Ethanol tank,i dont have a spare nozzle on the tank roof.But i have the nozzle on tank shall (almost at the top)
Shall i use the shell nozzle for N2 Blanketing?
Appreciate your good response.