Hi every one,
I have a question relating to nozzle sizing. What is recommended liquid velocity of nozzle outlet? E.g it should be lower than 1 m/s (Shell Standard). A lot of engineering document from our site chose 1m/s as default assumption for vessel design. Why? Where is it come from?
Please help me to clarify.
Thanks - vnpetroleum
|
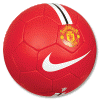
Nozzle Sizing
Started by vnpetroleum, Mar 25 2011 03:07 AM
6 replies to this topic
Share this topic:
#1
Posted 25 March 2011 - 03:07 AM
#2
Posted 25 March 2011 - 03:35 AM
vnpetroleum,
Nozzle sizing for vessels is done on the basis of 'momentum' criteria i.e rho*v2
where:
rho = density of the fluid, kg/m3
v = velocity of the fluid, m/s
For separator vessels which are typically used in the upstream oil and gas the following table should provide you the guidelines. The table is reproduced from a standard for a middle-east offshore Oil & Gas company and which I had prepared as an engineering project and which has also been one of my better known accomplishments during my career till date.
Inlet Device
Momentum
None
rmV2m,in <=1400 kg/m.s2
Half Open Pipe
rmV2m,in <= 2100 kg/m.s2
Schoepentoeter
rmV2m,in <= 8000 kg/m.s2 (Note-1)
Cyclone (conventional)
rmV2m,in <= 10,000 kg/m.s2 (Note-1)
Multi-cyclone
rmV2m,in <= 35,000 kg/m.s2 (Note-1)
Where rm is the mean density of the mixture in the feed pipe in kg/m³
& Vm,in is the velocity of the mixture in the inlet nozzle in m/s
Hope this helps.
Regards,
Ankur.
Nozzle sizing for vessels is done on the basis of 'momentum' criteria i.e rho*v2
where:
rho = density of the fluid, kg/m3
v = velocity of the fluid, m/s
For separator vessels which are typically used in the upstream oil and gas the following table should provide you the guidelines. The table is reproduced from a standard for a middle-east offshore Oil & Gas company and which I had prepared as an engineering project and which has also been one of my better known accomplishments during my career till date.
Inlet Device
Momentum
None
rmV2m,in <=1400 kg/m.s2
Half Open Pipe
rmV2m,in <= 2100 kg/m.s2
Schoepentoeter
rmV2m,in <= 8000 kg/m.s2 (Note-1)
Cyclone (conventional)
rmV2m,in <= 10,000 kg/m.s2 (Note-1)
Multi-cyclone
rmV2m,in <= 35,000 kg/m.s2 (Note-1)
Where rm is the mean density of the mixture in the feed pipe in kg/m³
& Vm,in is the velocity of the mixture in the inlet nozzle in m/s
Hope this helps.
Regards,
Ankur.
#3
Posted 25 March 2011 - 06:14 AM
vn,
Ankur has given momentum criteria for the INLET nozzle on a separator, where there is two-phase flow.
You asked about the LIQUID OUTLET nozzle.
In the case of a liquid outlet nozzle, the aim should be to avoid excessive velocity which could cause a vortex (thus drawing out vapour) or could disrupt the water-oil interface inside the vessel (if it is a three-phase separator). If the liquid is fed to a pump suction, the velocity should be low to limit the pressure loss in the suction line and thus keep the NPSH high enough. A velocity of 1 m/s is a good rule of thumb in these cases.
For some vessels like compressor KO drums, the liquid outlet is not critical, the liquid usually runs through a valve to a lower pressure system. For these cases you can use a higher velocity.
Paul
Ankur has given momentum criteria for the INLET nozzle on a separator, where there is two-phase flow.
You asked about the LIQUID OUTLET nozzle.
In the case of a liquid outlet nozzle, the aim should be to avoid excessive velocity which could cause a vortex (thus drawing out vapour) or could disrupt the water-oil interface inside the vessel (if it is a three-phase separator). If the liquid is fed to a pump suction, the velocity should be low to limit the pressure loss in the suction line and thus keep the NPSH high enough. A velocity of 1 m/s is a good rule of thumb in these cases.
For some vessels like compressor KO drums, the liquid outlet is not critical, the liquid usually runs through a valve to a lower pressure system. For these cases you can use a higher velocity.
Paul
#4
Posted 25 March 2011 - 07:11 AM
Hi,
first, 1m/s is not a Shell STANDARD but a guideline
Paul already gave a summary on what you need to take care of. but the 1 m/s vessel outlet nozzle sizing depends on much more than have been listed.
where does this stream go to ? if a pump then min is NPSH of the pump and velocity is resultant, if a valve then chocked flow & line hydraulics and so on
hope this helps
cheers,
sm
first, 1m/s is not a Shell STANDARD but a guideline
Paul already gave a summary on what you need to take care of. but the 1 m/s vessel outlet nozzle sizing depends on much more than have been listed.
where does this stream go to ? if a pump then min is NPSH of the pump and velocity is resultant, if a valve then chocked flow & line hydraulics and so on
hope this helps
cheers,
sm
#5
Posted 26 March 2011 - 04:50 AM
HI ,
This document may support your query .
Hope this helps
Breizh
This document may support your query .
Hope this helps
Breizh
#6
Posted 27 March 2011 - 10:29 AM
The local practice in the company I offer services to is: specify the size of the nozzle same as the size of the line connected to it. This for tanks or vessels, ingoing or outgoing lines.
So the issue is reduced to the size of the relevant line, where there are several guide lines from place to place. E.g. a rather general rule for liquid sizing is ΔPfriction not higher than 1 psi/100 ft (3 psi/100 ft for pipes<800 ft total length) and velocity not higher than a max value depending on pipe dia.
In atmospheric tanks storing flammable liquids, inlet or outlet velocity should be not more than 1 m/s, if tank level can be low enough so that air can approach the nozzle. This to avoid a sparkle due to static electricity, potentially causing fire.
If liquid level is always above the upper part of the nozzle, higher velocities can be applied.
It is pointed out that I have seen momentum data written on exchanger nozzles by Mechanical Department, which may result in a more rational size.
So the issue is reduced to the size of the relevant line, where there are several guide lines from place to place. E.g. a rather general rule for liquid sizing is ΔPfriction not higher than 1 psi/100 ft (3 psi/100 ft for pipes<800 ft total length) and velocity not higher than a max value depending on pipe dia.
In atmospheric tanks storing flammable liquids, inlet or outlet velocity should be not more than 1 m/s, if tank level can be low enough so that air can approach the nozzle. This to avoid a sparkle due to static electricity, potentially causing fire.
If liquid level is always above the upper part of the nozzle, higher velocities can be applied.
It is pointed out that I have seen momentum data written on exchanger nozzles by Mechanical Department, which may result in a more rational size.
#7
Posted 27 March 2011 - 09:24 PM
All,
Many thanks for your all responses. Our platform is running at the water production higher than design. Basis of design: 3 phase fluid from pipeline (which comed from WHP) to HP Separator, Water to Hydrocyclones, Oil to IP Separator then LP Sep then Oil Transfer Pump. HP Sep is designed at 100 000 bbld Oil/100 000 bbld Water (case 1) and 50 000bbld Oil/ 150000 bbld Water (Case 2). However, now we intend to increase water production up to 175 000 bbld water in the period of 2 months (water from other WHPs). I reviewed this separator and found that water outlet nozzle at HP 1.8 m/s (higher than recommended 1m/s). Water from HP Sep will flow to Hydrocyclones.
As you mentioned, liquid outlet sizing depends on requirement of downstream equipment. What is guideline for hydrocyclones? 1.8 m/s should be OK?
Thanks,
vnpetroleum
Many thanks for your all responses. Our platform is running at the water production higher than design. Basis of design: 3 phase fluid from pipeline (which comed from WHP) to HP Separator, Water to Hydrocyclones, Oil to IP Separator then LP Sep then Oil Transfer Pump. HP Sep is designed at 100 000 bbld Oil/100 000 bbld Water (case 1) and 50 000bbld Oil/ 150000 bbld Water (Case 2). However, now we intend to increase water production up to 175 000 bbld water in the period of 2 months (water from other WHPs). I reviewed this separator and found that water outlet nozzle at HP 1.8 m/s (higher than recommended 1m/s). Water from HP Sep will flow to Hydrocyclones.
As you mentioned, liquid outlet sizing depends on requirement of downstream equipment. What is guideline for hydrocyclones? 1.8 m/s should be OK?
Thanks,
vnpetroleum
Similar Topics
![]() Liquid Liquid Separator SizingStarted by Guest_Kentucky08_* , 03 Apr 2025 |
|
![]() |
||
![]() ![]() Nozzle Sizing CalculationStarted by Guest_BabRafiq1_* , 26 Aug 2022 |
|
![]() |
||
![]() Guidance On Sizing Jacketed Pipe For Glycerine CoolingStarted by Guest_Kentucky08_* , 28 Jun 2025 |
|
![]() |
||
![]() Separator Sizing Step By Step ProcedureStarted by Guest_krishnamurthy_* , 06 Apr 2023 |
|
![]() |
||
Critical Pressure For Choke Valve SizingStarted by Guest_Sherif Morsi_* , 07 Nov 2017 |
|
![]() |