|

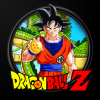
Flare Gas Recovery
#1
Posted 29 November 2019 - 09:51 AM
#2
Posted 29 November 2019 - 10:28 AM
This sounds like a bad idea. And dangerous.
Bobby
#3
Posted 30 November 2019 - 01:29 AM
Edited by Soothsayer, 30 November 2019 - 01:29 AM.
#4
Posted 30 November 2019 - 04:46 AM
Thank you, but why? I was told that a Process Safety evaluation is irrelevant during the concept phase.
Regarding Process Safety evaluations as irrelevant (no matter what phase) sounds like another bad idea. Especially when dealing with a subject that is directly related to process safety (i.e. the flare gas system).
#5
Posted 30 November 2019 - 08:19 AM
Edited by Soothsayer, 30 November 2019 - 11:23 AM.
#6
Posted 01 December 2019 - 02:18 AM
Conceptually, you would have to confirm that ALL pressure safety valves are with adequate capacity to relieve into a higher pressure discharge (=flare) system.
Sonic flares are commonly used offshore but they are normally employed in high-pressure systems.
#7
Posted 01 December 2019 - 05:10 AM
Hi,
Just curious what are the numbers ?
Breizh
#8
Posted 01 December 2019 - 05:20 AM
#9
Posted 01 December 2019 - 05:22 AM
Conceptually, you would have to confirm that ALL pressure safety valves are with adequate capacity to relieve into a higher pressure discharge (=flare) system.
Sonic flares are commonly used offshore but they are normally employed in high-pressure systems.
That's right. We will do that. It seems that’s the only major risk!
#10
Posted 01 December 2019 - 05:24 AM
Hi,
My question is about the quantity you intend to recover .
Breizh
#11
Posted 01 December 2019 - 07:56 AM
Hi,
My question is about the quantity you intend to recover .
Breizh
It is just 500 - 700 Sm3/h of light MW HC gas.
#12
Posted 01 December 2019 - 10:00 AM
Sonic flare is used to enable lower size of the flare network piping, not to recover gas. I was mentioning sonic flare systems just as an example how flare systems can operate at higher pressures.
It's not enough just to pressure up the flare gas system and recycle gas back to process. You need to look at each production and relief scenario and see how recycling in the process will affect that scenario. There is probably several scenarios with multiple relief points (e.g. loss of power, loss of utility, etc.), including total site blowdown (emergency). I wouldn't advise to anyone to recycle the gas back to the process under those circumstances - you would actually be fueling the fire.
Open path to the flare must be maintained at ALL times - and there are no exceptions to this rule.
#13
Posted 02 December 2019 - 01:58 AM
Sonic flare is used to enable lower size of the flare network piping, not to recover gas. I was mentioning sonic flare systems just as an example how flare systems can operate at higher pressures.
It's not enough just to pressure up the flare gas system and recycle gas back to process. You need to look at each production and relief scenario and see how recycling in the process will affect that scenario. There is probably several scenarios with multiple relief points (e.g. loss of power, loss of utility, etc.), including total site blowdown (emergency). I wouldn't advise to anyone to recycle the gas back to the process under those circumstances - you would actually be fueling the fire.
Open path to the flare must be maintained at ALL times - and there are no exceptions to this rule.
Regards.
#14
Posted 02 December 2019 - 12:29 PM
You keep making a bad idea worse. You cannot have any valves or obstructions in the flare line. You should abandon the idea and proceed with other tasks.
Bobby
#15
Posted 02 December 2019 - 03:56 PM
I understand that high pressure drops or pocket shall be avoided. But then how you explain Flare Gas Recovery Units? It is a package with a compressor or an ejector and a PCV downstream. FOV are installed for isolation of the flare header. I could show you systems with ON/OFF valves, check valves, flow meters in flare gas lines in facilities of major and worldwide recognize oil companies. Pressure drop does not necessarily mean obstruction. The flare system, and relief devices, can be design for that!You keep making a bad idea worse. You cannot have any valves or obstructions in the flare line. You should abandon the idea and proceed with other tasks.
Bobby
Once again, please explain why it is bad idea.
Regards.
Edited by Soothsayer, 02 December 2019 - 04:52 PM.
#16
Posted 02 December 2019 - 04:12 PM
the isolation valves (FOV) will open and flaring will occur.
What isolation valves? Could you maybe provide a small (hand-drawn is fine) sketch of what you imagine that system would look like?
#17
Posted 02 December 2019 - 04:16 PM
I understand that high pressure drops or pocket shall be avoided. But then how you explain Flare Gas Recovery Units? It is a package with a compressor or an ejector and a PCV downstream. FOV are installed for isolation of the flare header. I could show you systems with ON/OFF valves, check valves, flow meters in flare gas lines in facilities of major and worldwide recognize oil companies. Pressure drop does not necessarily mean obstruction. The flare system, and relief devices, can be design for that!You keep making a bad idea worse. You cannot have any valves or obstructions in the flare line. You should abandon the idea and proceed with other tasks.
Bobby
Once again, please explain why it is bad idea.
Regards.
As you said yourself: An FGRS has a compressor. A compressor which you for some reason do not want to use.
Edited by PhilippM, 02 December 2019 - 04:18 PM.
#18
Posted 03 December 2019 - 01:56 AM
Soothsayer,
Flare gas recovery units are always designed in parallel to the continuously open flare header (i.e. the main header is not closed by any switching valves). The PCV feeding the flare gas recovery unit always maintains positive pressure inside the relief system, so as to prevent inward flow of Oxygen from atmosphere to flare header and/or into the Recovery Unit.
Imagine your FOV does not open in case of a major relief event, or in case of any significant relief event. That's a scenario with tragic consequences. No serious operator company in this world would approve such design. Even if you have a SIL 3 rated instrumented valve unit (or whatever the safety analysis calls for) for this interlocking system, it can hardly be justified because of unforeseen consequences in case of failure.
#19
Posted 03 December 2019 - 06:37 AM
Soothsayer,
Flare gas recovery units are always designed in parallel to the continuously open flare header (i.e. the main header is not closed by any switching valves). The PCV feeding the flare gas recovery unit always maintains positive pressure inside the relief system, so as to prevent inward flow of Oxygen from atmosphere to flare header and/or into the Recovery Unit.
Imagine your FOV does not open in case of a major relief event, or in case of any significant relief event. That's a scenario with tragic consequences. No serious operator company in this world would approve such design. Even if you have a SIL 3 rated instrumented valve unit (or whatever the safety analysis calls for) for this interlocking system, it can hardly be justified because of unforeseen consequences in case of failure.

Edited by Soothsayer, 03 December 2019 - 06:39 AM.
#20
Posted 03 December 2019 - 07:09 AM
A sketch would definitely help, indeed.
Zero flaring normally refers to "zero operational flaring", which means no flaring under normal operating conditions and NOT no flaring under process or emergency relief condition. That's dangerous and I think everyone understood this is what you intend to do.
If you have a continuous flow of process gas (not relief gas) than you can definitely pressurize this stream and recycle it back to the process - but I fail to see why it has to be through the flare header.
#21
Posted 03 December 2019 - 07:40 AM
A sketch would definitely help, indeed.
Zero flaring normally refers to "zero operational flaring", which means no flaring under normal operating conditions and NOT no flaring under process or emergency relief condition. That's dangerous and I think everyone understood this is what you intend to do.
If you have a continuous flow of process gas (not relief gas) than you can definitely pressurize this stream and recycle it back to the process - but I fail to see why it has to be through the flare header.
Zauberberg,
You are right. I did not explain it well. The FGRU intends to assure zero flaring under NORMAL operating conditions. Of course, flaring will occur under emergency relief scenario.
The reason for doing it through the flare header is because these continuous sources are connected to it. The design was conceived with this normal contribution of gas to the flare system.
Regards.
Edited by Soothsayer, 03 December 2019 - 08:26 AM.
#22
Posted 03 December 2019 - 10:17 AM Best Answer
You can modify the system, in a relatively simple way:
1) Connect the flare gas sources to a new process header, while maintaining their existing connections to the flare (sub)headers. Set a new pressure control valve in the header or, even better, in a new surge vessel downstream, and ensure the existing pressure control valves on flare gas sources will have sufficient delta pressure to discharge full flow while PCV's remain in the stable control regime (because they will discharge to a higher pressure).
2) Interlock the system in such way, that under normal circumstances the vent flow goes to FGRU, and in case of FGRU unavailability (e.g. valve to the process sub-header stuck closed, or FGRU unit shutdown) the flow is directed to flare (sub)headers.
3) Ensure that in case of interlocking system failure, the source vessels are protected from overpressure by other means, and there is unrestricted relief path (i.e. not valved) to the flare.
4) Run an independent safety analysis to confirm suitability of the design.
Note: edited a typo in point No 2.
Edited by Zauberberg, 03 December 2019 - 02:07 PM.
Similar Topics
![]() Flare Header Reverse FlowStarted by Guest_Ahmadhamzahperta_* , 04 Apr 2025 |
|
![]() |
||
Vacuum RecoveryStarted by Guest_Paper_* , 25 Feb 2025 |
|
![]() |
||
Psv On Ko Drum With Flame Arrestor At Flare Vent LineStarted by Guest_Tintin2024_* , 29 Oct 2024 |
|
![]() |
||
Slope Of Flare Sub Headers / Tail Pipes And Main HeadersStarted by Guest_Sawsan_* , 02 Dec 2024 |
|
![]() |
||
![]() Opportunities For Heat Recovery In A Chemical Process PlantStarted by Guest_tanyongboon1_* , 29 Nov 2024 |
|
![]() |