|

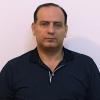
Closed Loop Pump Suction Line Sizing Criteria
#1
Posted 30 August 2024 - 01:11 AM
#2
Posted 30 August 2024 - 03:31 AM
Hi,
Consider this post to support your work:
https://www.cheresou...in-closed-loop/
A google search should provide addtional input .
Breizh
#3
Posted 30 August 2024 - 04:07 AM
As JoeWong mentioned in the thread linked by Breizh - you should be considering the NPSHa and NPSHr, and not concentrating on the velocities.
It is hard to envisage a truly closed single phase liquid system. If it is single phase then there is probably an expansion tank near the pump suction and the line from this tank to the pump suction should be sized as usual for suction piping. If it is two phase then there must be a condensate collection tank near the pump suction and again the suction piping should be sized as normal.
If you provide more details, and preferably a flowsheet, you will get more relevant answers.
#4
Posted 30 August 2024 - 08:50 AM
Hello everybody,As you know, different velocity and pressure drop criteria are normally used for pump suction and discharge pipes. Typically, the process design criteria recommend lower velocity and pressure drop for the pump suction compared to the discharge pipe.My question is, what should we do if a pump is installed in a circulation loop? In this case, the pump suction and discharge pipes can be same size and see same velocity. Will any problems occur with the pump if we deviate from the sizing criteria for the pump suction line and use same pipe size for pump suction and discharge?
Hi Afshin,
In order to provide adequate NPSHA for a pump along a circulation loop, it's normally supported by an expansion tank (atmospheric or pressurized) which is connected to the loop at the suction line with a size larger than the discharge line leading to different PD and velocity at suction/discharge lines.
Then, there would be no reason deviating from the relevant project sizing criteria.
#5
Posted 05 September 2024 - 04:06 AM
Attached Files
Edited by Afshin445, 05 September 2024 - 04:17 AM.
#6
Posted 05 September 2024 - 05:14 AM
NPSHA should be calculated at any condition that may exist, like start-up, normal operating conditions, shutdown, etc. Cavitation is destructive to the pump and pump seal, so it should be avoided under any condition.
#7
Posted 05 September 2024 - 05:31 AM
Hi,
NPSHA should be calculated for the worst condition. I remember using KSB pump for similar condition (high temperature, Pressurized system), should be Etanorm.
Regarding velocity 1.8 m/s is not considered as high velocity for water.
Something is missing on your system is a PSV in case of over pressure.
Edit
https://www.reasonte...r-accumulators/
Good luck
Breizh
#8
Posted 05 September 2024 - 09:21 AM
The additional information and the flowsheet make the problem much clearer.
I agree with breizh that you need a relief valve on the expansion tank - it would be a legal requirement in most areas because the tank contains pressurised water above its normal boiling point.
But the most important thing that is not shown is how the pressure in the expansion tank is maintained. I guess this will be an air or nitrogen system. If you pressurise the system to 8 barg before starting the circulation and the heating then designing the piping from the expansion tank to the pump to satisfy the NPSHr at cold start up should be no problem. And even if the heat sinks are bypassed and you are circulating 160°C water the vapor pressure is only about 5.2 barg and again ensuring the necessary NPSH should be easy.
As I said before, your calculations should be centred on the NPSH and not on the velocity.
#9
Posted 05 September 2024 - 12:26 PM
Thank you Breizh, Kamtar and Naser for your valuable responses, and I apologize for the delayed reply.To clarify my query, I have prepared a simple sketch of the heating loop system (please see attachment). The system is currently under design, and the heating medium being used is water. At the maximum expected temperature (160 °C), the water vapor pressure is approximately 5.2 barg. Since the pressure upstream of the circulation pumps is around 8.0 barg, it does not seem like there should be any concerns regarding NPSH and cavitation under normal conditions when the heating loop is pressurized.However, if the same pipe size (6 inch) is used for the entire loop based on pump discharge sizing criteria, the velocity in each pump suction line will be around 1.8 m/s, and the pressure drop will be about 16 kPa/100 m. This high velocity from the pump suction line sizing criteria perspective raises a question about whether high velocity in the pump suction can be problematic for the pump, despite NPSH not being a concern.Additionally, I would like to understand if NPSHA should be calculated under normal conditions or during start-up when the system is still not pressurized.
You're welcome Afshin,
Yes, high velocity in pump suction line can lead to noisy flow pattern at the impeller inlet which may reduce pump reliability and performance, but 1.8 m/s is not a high velocity for pump suction line at all.
The NPSHA should be calculated under worst condition which appears to be at start up in your case.
I think the loop should mostly be pressurized through the expansion tank before pump start up.
Similar Topics
![]() Liquid Liquid Separator SizingStarted by Guest_Kentucky08_* , 03 Apr 2025 |
|
![]() |
||
![]() ![]() Nozzle Sizing CalculationStarted by Guest_BabRafiq1_* , 26 Aug 2022 |
|
![]() |
||
Compressor Suction DrumStarted by Guest_Lyne_* , 04 Jul 2025 |
|
![]() |
||
![]() Guidance On Sizing Jacketed Pipe For Glycerine CoolingStarted by Guest_Kentucky08_* , 28 Jun 2025 |
|
![]() |
||
Hot Oil Loop / Heating Medium DesignStarted by Guest_Lyne_* , 30 Mar 2024 |
|
![]() |