Good evening,
Just a quick one: what are the effects of undersized gas outlet nozzle in water knockout drums? Can this promote upset/dislodging of vessel internals?
In-house calculations show there is excessive momentum (>5,000 kg/ms^2) at the vessel gas outlet. At the same time, the performance of this vessel with regards to water removal efficiency is quite poor (<98%).
Any info on this subject?
Thanks,
|
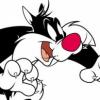
Undersized Gas Outlet Nozzle
Started by Zauberberg, Jun 16 2009 07:43 AM
5 replies to this topic
Share this topic:
#1
Posted 16 June 2009 - 07:43 AM
#2
Posted 16 June 2009 - 08:19 AM
For your reference only.
Several years ago, I worked with a separator installed with a wire mesh demister in a plant. Once the plant capacity was maintained above 110%, the demister was torn after sometime and water separation efficiency was very very poor.
Several years ago, I worked with a separator installed with a wire mesh demister in a plant. Once the plant capacity was maintained above 110%, the demister was torn after sometime and water separation efficiency was very very poor.
#3
Posted 16 June 2009 - 08:26 AM
A drop in separator efficiency should be expected. Much of the internal volume of the separator is devoted to developing the flow (even though it will never approach fully developed flow in so short a distance). An undersized outlet nozzle will result in high velocities extending downward to (probably) the top of the demister. At least locally, there could be high stresses trying to pull apart the demister. Even if strong enough to resist this, I can visualize poor disengagement of the liquid since reentrainment would likely occur.
#4
Posted 16 June 2009 - 10:29 AM
Thanks for the replies. In fact, this vessel started experiencing pressure drop 3 times higher than design once when the feed gas rate has been increased. Vessel internals consist of Schoepentoeter, Yorkmesh, and the Vane Pack. High pressure drop could be an indication that something has happened with the internals, and low separation efficiency observed in the field points in the same direction.
According to design standards, the current gas load factor is still below the maximum design value for this type/size of vessel, and I was wondering if only the slightly undersized gas outlet nozzle can create such a big bunch of problems.
Best regards,
#5
Posted 17 June 2009 - 11:19 AM
What is the path forward in debottlenecking the nozzle? Cutting a new one, with an appropriate size?
Changing vessel internals would not debottleneck the nozzle, and cutting a new one is an adventure in remote locations such is Bioko Island.
The vendor says the gas distribution plate - installed beneath the nozzle - is there to compensate for excessive velocities (momentum), but I wouldn't believe it; the vessel is suffering from low efficiency when feed gas rate is increased (and still below revamp design value).
Any information is appreciated.
#6
Posted 17 June 2009 - 10:46 PM
QUOTE (Zauberberg @ Jun 17 2009, 09:19 PM) <{POST_SNAPBACK}>
What is the path forward in debottlenecking the nozzle? Cutting a new one, with an appropriate size?
Changing vessel internals would not debottleneck the nozzle, and cutting a new one is an adventure in remote locations such is Bioko Island.
The vendor says the gas distribution plate - installed beneath the nozzle - is there to compensate for excessive velocities (momentum), but I wouldn't believe it; the vessel is suffering from low efficiency when feed gas rate is increased (and still below revamp design value).
Any information is appreciated.
Changing vessel internals would not debottleneck the nozzle, and cutting a new one is an adventure in remote locations such is Bioko Island.
The vendor says the gas distribution plate - installed beneath the nozzle - is there to compensate for excessive velocities (momentum), but I wouldn't believe it; the vessel is suffering from low efficiency when feed gas rate is increased (and still below revamp design value).
Any information is appreciated.
Dear Zauberberg Hello/Good Morning,
If there is a safe way to inert gas purge in reverse flow direction without upsetting the system internals to evaluate the extent of and possibly the type of physical blockages and/or depositions if any?
Thereafter if manageable to draw the samples of clogging/deposited material and analysis chemically/physically to check solvency,solubility and use accordingly flushing materials to remove obstructing materials from the system.
Hope this all is manageable at your remote location and may help you with a way forward.
Similar Topics
Blocked Outlet For Continous SourceStarted by Guest_56200358_* , 03 Feb 2025 |
|
![]() |
||
![]() Psv Flashing, Sizing Outlet Line 2-Phase.Started by Guest_felderosfelder101021_* , 09 Dec 2024 |
|
![]() |
||
![]() ![]() Nozzle Sizing CalculationStarted by Guest_BabRafiq1_* , 26 Aug 2022 |
|
![]() |
||
Outlet Temperautre Of ReboilerStarted by Guest_hysyshunter_* , 18 Mar 2024 |
|
![]() |
||
Blocked Outlet For Vessel With Multiple DischargeStarted by Guest_Ghasem.Bashiri_* , 24 Dec 2023 |
|
![]() |