Chemical and Process Engineering Resources
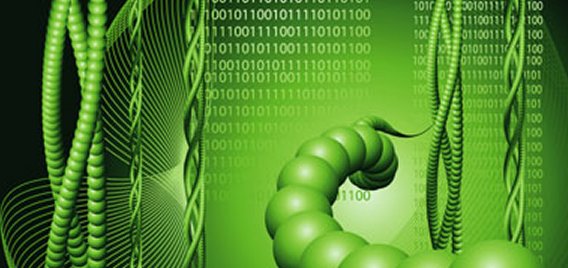
Types of Biosorption
Biosortpion can be carried out as a batch process, a continuous process, or a two-stage process with continuous metal recovery.
Biomass should be defrosted and washed with deionized water. To ensure equal quality of the biomass during all experiments, different kinds of biomass should be mixed together to obtain a uniform mixture.
Batch Process
Batch biosorption experiments can be done in a stirred vessel (Figure 4) with a working volume of approximately 100 mL.
Continuous Process
Continuous process experiments can be carried out in a glass column having an inner diameter of 5-8 cm and filled with a packed bed of biomass pellets of varying heights (20, 40 and 55 cm), set with an adjustable plug (Figure 5). The effluent solution of metal ions can be fed from the top of the column with the help of a pump using varying flowrates. An inert bed of glass spheres can be placed at the bottom of the column below the active biomass bed to ensure homogenous distribution of the feed. The remaining metal concentration can be measured online in the effluent at the top of the column. The breakthrough curves can be recorded as a function of the flowrate and bed height.
Measurements of metal ion concentrations in the solution can be made online with metal-detecting electrodes or ion-selective electrodes, and may be verified with an atomic absorption spectrometer.
Two-Stage Process with Continuous Metal Recovery
Two-stage continuous biosorption and metal recovery can be carried out as shown in Figure 6. This process is similar to continuous biosorption, although the metal solution is adsorbed in two stages. After initial adsorption and filtration in stage one, the effluent is fed with fresh biosorbent into stage two, where further biosorption of the metal ion takes place. The effluent from the second stage is filtered to recover the metal ions and biosorbents. The effluent sample can be analyzed using an ion meter or by adsorption spectroscopy.
Desorption
Regeneration of loaded biosorbent is critical to keeping costs down and to recovering the metal(s) extracted from the liquid phase. The deposited metals are washed out (desorbed) and the biosorbent is regenerated for another cycle. The desorption process should result in:
- high-concentration metal effluent
- undiminished metal uptake upon re-use
- no physico-chemical damage to the biosorbent.
The desorption and sorbent regeneration studies might require somewhat different methodologies, beginning with screening for the most effective regenerating solution.
Because different metal ions have different affinities for the biosorbent, the uptake has some degree of metal selectivity. The selectivity of the elution-desorption operation may be different, which may serve as another means of eventually separating metals from one another if desirable.
The concentration ratio (CR) is used to evaluate the overall concentration effectiveness of the whole sorption-desorption process:
Obviously, the higher the CR, the better the overall performance of the sorption process, making the eventual recovery of the metal more feasible with higher eluate concentrations.
Recovery of the metal from these concentrated desorption solutions is carried out in a different plant by electrowinning. Following desorption of the metal(s), the column may be further pre-treated (e.g., pre-saturated with protons such as Ca, K, etc.) for optimum operation in the next metal uptake cycle. The specific type of pre-treatment used to optimize the column performance may vary.
Feasibility of Biosorption
For successful application on a large scale, any operation needs to be economically viable. The feasibility of a biosorption process depends on such factors as:
- biosorbent uptake performance
- the source of the raw biomass
- biomass granulation and treatment
- the desorption and regeneration processes used.
Often, the source of the biosorbent has a major impact on the feasibility of the operation. Biosorbents (biomass) should always be obtained from the least-expensive source, such as from the effluent of a fermenter, seaweeds from nearby bodies of water, algae, etc. The spent biosorbents can be regenerated at very low cost using water, so the material can be reused many times. Hence, considering the overall unit operations involved in biosorption, we can conclude that the process is generally economically viable.
Advantages of Biosorption
Biosorption is highly competitive with the presently available technologies like ion exchange, electrodialysis, reverse osmosis, etc. Some of the key features of biosorption compared to conventional processes include:
- competitive performance
- heavy metal selectivity
- cost-effectiveness
- regenerative
- no sludge generation.
Biosorption is particularly economical and competitive for environmental applications in detoxifying effluents from, for example:
- metal plating and metal finishing operations
- mining and ore processing operations
- metal processing
- battery and accumulator manufacturing operations
- thermal power generation (coal-fired plants in particular)
- nuclear power generation.
0 Comments