|

Lpg Sphere Relief Scenarios
#1
Posted 28 March 2012 - 12:31 PM
Is my interpretation of the API requirement correct and do i need to consider this as a relieving scenario? If yes how do i go about calculating the relief load?
#2
Posted 28 March 2012 - 09:56 PM
Your interpretation is correct.
If the scenario is credible (that is, if the design pressure of the sphere is lower than the design pressure upstream the control valve), then you should use the pump rated flowrate as the relieving flowrate.
Edited by sheiko, 28 March 2012 - 09:59 PM.
#3
Posted 29 March 2012 - 01:03 AM
Also is gas blowby same scenario or something different?
#4
Posted 29 March 2012 - 01:06 AM
Lack of adequate information as follows:
Supposed you are protecting the sphere. Can you present a simple sketch of the system? Isn't there a LPG return line on sphere to return the LPG vapor back to the source? Is the pump centrifugal type? Is the pump curve available?
Anyway, if design pressure of the sphere are equal to or higher than pump shut off pressure no overpressure protection is required, othrwise the PSV relief load (for centrifugal type pump) would be the pump capacity.
Seems gas blow by wouldn't be a credible scenario for such system at all.
Fallah
Edited by fallah, 29 March 2012 - 01:13 AM.
#5
Posted 29 March 2012 - 01:52 AM
1. Pump shut-off pressure has no effect on the sphere pressure.
2. The only credible scenario that I can think of related to the control valve is liquid overfilling that PSV size should be adequate to release liquid LPG at the maximum possible flowrate that is with control valve 100% open.
3. If pump is already available (existing) you need to determine the meeting point between pump performance curve with that of system curve at 100% valve opening.
Edited by S.AHMAD, 29 March 2012 - 02:03 AM.
#6
Posted 29 March 2012 - 02:13 AM
There is no LPG vapor return line. The pump is centrifugal type with assumed rise to shut off as 25%. The shut off pressure is higher than sphere design pressure.
#7
Posted 29 March 2012 - 09:01 AM
Fallah has made a courteous and well-meaning request: Can you present a simple sketch of the system?
If you comply with his request, he can not only help you on this specific topic, but he can also possibly add valuable and experienced comments on the entire process and other areas as well.
#8
Posted 29 March 2012 - 10:19 PM
#9
Posted 31 March 2012 - 01:20 PM
Yes, indeed and all valves around the sphere (not PSVs) are known to be considered closed during fire. The pump discharge line to sphere must have an isolation valve automatically closing at fire. See http://www.cheresou...vessel-failure , post No 7. Referred valve was mechanically actuated, similar to "LPG In-Tank safety shutoff valves" of http://www.detect-m...l#IntankValves . It is judged that the sphere can be considered isolated during fire if that valve is mechanically actuated.In most scenarios like this, the governing case for the relief valve will be fire.
If the isolation valve is not mechanically actuated to close on fire, best thing may be to consult the HAZOP study already elaborated, assuming that this is an existing installation. The scenario of fire case while the sphere is being charged with liquid LPG should be faced there. But I do not know the way out.
Edited by kkala, 31 March 2012 - 01:23 PM.
#10
Posted 31 March 2012 - 08:19 PM
1. You should respond to fallah, Kkala, and Art’s request to allow us to offer more meaningful comments.
2. If I were you, based on my own visualization of the process, I can only think of two credible scenarios
a. Fire Case
b. Liquid overfilling (flow control valve stuck opened during filling).
3. In the past, most process design overlooked the case of liquid overfill. ExxonMobil has taken this liquid overfill case seriously after some incidents related to liquid overfill. In fact, they have a computer program called LORAT - short for LIQUID OVERFILL RISK ASSESSMENT TOOL. They are using LORAT to evaluate risk of liquid overfilling in their existing plants, worldwide.
4. I hope you do not repeat the same mistake.
Edited by Art Montemayor, 20 July 2012 - 10:29 AM.
#11
Posted 01 April 2012 - 10:43 AM
1. Whether the vessel under consideration can be exposed to an external pool fire.
2. Whether the wetted vessel surface can be exposed to a sustained fire if it is at a height of more than 25 ft (7.6 m). API STD 521 says that at a height more than 25 ft there can be no sustained heat input to the vessel wetted surface and for all practical purposes the fire case may not be applied (API STD 521, clause 5.15.1.1).
Let us consider a scenario where there is no source of a flammable fluid which can cause a pool fire in a radius of 100 ft from the vessel for which the fire case is being evaluated. In other words, the vesssel under evaluation is a stand-alone vessel. Then should you consider a fire case. I would think no.
Let us consider another scenario that a pool fire can be possible due to the proximity of another vessel to the vessel under consideration containing a flammable liquid which can have a pool fire at grade level. However, the bottom surface ot the vessel is at a height of 40 ft from grade. Then should you consider a fire case. I would think no based on the API STD 521 guidelines.
Considering the specific geometry of a sphere, API STD 521 mentions that the wetted surface of a sphere for fire relief calculations should be considered based on the surface area of the sphere exposed to a fire up to a height of 25 ft or its maximum horizontal diameter whichever is greater. (API STD 521, Table 5).
My point here is that a fire case should not be considered arbitrarily without proper evaluation, unless the design guidelines prescribed by the company say that for any vessel handling hydrocarbons fire case has to considered as a policy or default.
I would welcome comments on my rational of some of the relief system expert members of the forum such as Fallah and Lowflo who have contributed immensely to the Relief Devices forum. Probably Art Montemayor can also give some expert advice based on his immense experience.
Regards,
Ankur.
Edited by ankur2061, 01 April 2012 - 11:02 AM.
#12
Posted 01 April 2012 - 02:25 PM
While I appreciate your statements, for most above ground spheres and bullets storing hydrocarbon materials (propane, butane, pentanes and similar), the risk of fire is very high, and the scale of incidents caused by fires around such equipment is noteworthy (http://en.wikipedia....uanico_Disaster)
I agree, one should perform the proper fire assessment for both pool fires and jet fires on such storage equipment to determine the PSV size, and whether any additional systems are required (jet fire impinging on unwetted vessel can be catastrophic too) to reduce the risk of BLEVE. Overfill may still govern the relief device sizing, but my experience is that is usually not the case.
In the jurisdiction I am in, most recent (last 20 years) facilities have used buried or mounded bullets in place of spheres or above ground bullet, largely to avoid the pool fire scenario.
#13
Posted 01 April 2012 - 03:07 PM
In 52 years I have debunked and eliminated a lot of alleged “fire” cases in many a Hazop. Most – if not all - of these alleged fire cases were thrown out because a credible case could not be established as to the development of a POOL OF COMBUSTIBLE LIQUID FUEL directly under, around, or in the immediate area of the subject vessel to be protected. The subject of adequate or natural drainage is of importance in such scenario evaluations and must be defined in order to build a credible pool fire case. I keep repeating the FULL term, pool fire case, because the basis of this scenario is that a POOL of combustible liquid fuel is ignited – not just any ordinary fire case. API carefully stipulates this basis for the development of the resulting overpressure in the affected vessel. Therefore, as Ankur has stipulated, it is important to confirm that the details leading up to and supporting the credible pool fire case.
The API fire case, in my opinion, sets up a scenario whereby the pool of liquid fuel ignites and envelopes the subject vessel – heating its surface through the action of hot convection gases and also through the radiation effect. Therefore, if the actual pool is not truly located under – or around – the subject vessel, but really nearby or proximate to it, then the radiation effect will be the sole contributor to the heat up of the vessel’s walls. Here is where I have a lot of problems with the API limitation of the height of the flames’ effect. Although a radiation effect will be lessened by the distance of 25 feet, nevertheless, there will be a heat transfer effect taking place. Proof of this is that it is certainly unreasonable to expect a person – even a fire fighter - to stand securely and unaffected by the radiation effects of an open flame located 25 feet away. The radiation effect may be slower, but the skin temperature can be intolerable for anyone. The same effect would be felt by a vessels outer wall: the temperature would rise and the internal fluids – especially if they are low boiling liquids – such as acetone, methanol, etc. etc. Agreeably, the rate of pressure build-up is lessened as the pool fire is located further and further away. But the true protection of the vessel should be intact and the protection of the vessel assured – even if the pressure build-up rate (vapor generated internally) is less than that for the full capacity of the pool fire case.
Additionally, I would mention that the Blow-through case is another case that often appears as a viable possibility in process plant vessels that are connected to pressure sources. These can easily be much higher than the fire case in some cases.
Each scenario should be studied on its own merits and justified by credible evidence or logic. It often is too easy to throw about the fears and anxieties of creating a potential fire case. Careful and prudent drainage sometimes eliminates the pool fire case in some cases.
#14
Posted 02 April 2012 - 02:11 AM
Agreed with most of your viewpoints, i present those of mine as follows,
1- Codes and standards such as ASME and API are mostly included guidelines on how to going on when a designer has decided to consider the fire case as an applicable scenario for a vessel and left the first decision to the designer.
2- Most of the times the fire case to be considered for a vessel can be exposed to a pool fire from a burning liquid operating at a temperature higher than its flash point.
3- Leakage of sub-ambient liquids from the vessels handling them while cannot be isolated, could be a potential of creating pool fire provided that the 1)inventory to be as much as a sustained leak would be possible and also considering these liquids will quickly evaporate, 2)the accumulation of such liquids would be possible.
4- There may be many cases cannot be evaluated for possibility of fire case based on specific guidelines in API/ASME and the users have to evaluate the risks and make a proper decision based on good engineering practices.
5- Bottom line is that each case has its own conditions and there is no unique and straightforward procedure to decide when to consider fire case for a vessel and when not to consider that case.
Hope i could contribute in order to clarify the issue as you asked us.
Fallah
#15
Posted 02 April 2012 - 03:40 AM
#16
Posted 02 April 2012 - 03:53 AM
IMO, as far as he has contributed in the discussion he has got the answers and seems he is satisfied, but if you mean the discussion is opened by Ankur in this thread, OK, it might be better to be done via a new thread.
Fallah
#17
Posted 02 April 2012 - 04:05 AM
I have learned a lot since joining this forum so I enjoyed reading comments by Ankur, Art and you as well as Bard. I am just wondering why go-fish did not respond.
Edited by S.AHMAD, 02 April 2012 - 04:07 AM.
#18
Posted 02 April 2012 - 04:48 AM
OK, thanks, hope go-fish would specify if he got his required answer....
Fallah
#19
Posted 02 April 2012 - 07:18 AM
#20
Posted 03 April 2012 - 10:04 AM
In my opinion, complying with two colleagues experienced in refinery surveys, this is not true. I agree with Technical Bard (post No 12), and have not seen a storage sphere without Fire PSVs (FPSVs). My experience of spheres (all with FPSVs on them) is limited to following.
1. All spheres of Aspropyrgos Refinery, rough layout at http://airfresh-soc...ster-1984.html , also having spray water cooling for fire protection.
2. Basic design (1990) of two (dia=19.1 m) propylene spheres in Salonica Refinery approved by M W Kellogg. Deluge water systems for cooling. Project not implemented for economic reasons. Refinery standards were applied.
3. LPG sphere in Ekolina company to fill LPG "bottles" (Aspropirgos), spray water cooling.
Can a member supply references of spheres without FPSVs on them, if possible with limited data indicating the reason? Are cooling systems installed on these spheres for fire protection (if not insulated)? The info could help in understanding the need (or no need) of FPSVs.
Below are some potentially useful views on the topic, of course subject to criticism.
1. Quite improbable for spheres to have bottom at a height of 25 ft, or their diameter (whichever higher), from ground; cost due to elevation is too high for a construction so heavy. Suction pump NPSHr dictated the height of said propylene spheres.
2. API 2510A (not known to me), Fire Protection Considerations for the design and operation of LPG storage facilities, seem to be useful as a guide, see http://www.fireengi...e-for-lpg-bulk .* Suppose that nearest possible pool fire (propane) has 55 ft diameter and can occur 125 ft far from an LPG sphere (see diagram in fire engineering *). The LPG sphere needs no fire protection against this pool fire. Yet it is vulnerable to any possible BLEVE or explosion of a vapor cloud, having originated from a greater distance. This can create fire around the sphere, where FPSVs and external cooling could delay a secondary BLEVE or even prevent it.
3. Disaster examples similar to above para 2 can be seen in San Juanico accident (first web link in this post, or that in Technical Bard's post), or in Feyzin accident, http://en.wikipedia...eyzin_disaster . In both accidents cause was not a pool fire, but a cloud of flammable vapor having exploded. This could cause destruction far from original point of leakage, with subsequent domino effects and fires.
4. Indeed spheres do not have a confined space below (on the ground) to create a pool in case of serious leakage. Liquid after flashing is assumed to be directed on the ground to some safe location. Yet a short pool fire may be created, especially if leakage rate is high. At any case a very flammable liquid is flowing, fire is possible on this ground area.
Piping connected to the sphere can also leak to create an explosion, or be physically damaged to create jet fire, or even some pull fire.
5. A "stand alone" sphere can be hardly found in a refinery, due to space limitations (although layout safety is being improved). Look how far domino effects are extended in Aspropirgos Refinery (first link of this post). Leakage from a sphere considered "stand alone" can cause vapor cloud explosion through a distant spark, similarly to Feyzin accident. Physical damages to piping (para 4) can also occur.
6. Standard IPS-E-ME-130 (para 6.10) requires fire proofing of skirts and leg supports of LPG spheres, without any exception. (NFPA 59A and API 2510 are also referred to).
7. Even if some of the above mentioned events have low probability to occur (which has to be indicated quantitatively), the counter argument is that a low probability event of heavy consequences is credible. Indeed the event of a sphere fire can result in a heavy accident, deserving proper preventive or mitigating measures. Level of these measures seem to be stricter and stricter with time.
8. Preventive measures try to reduce accident probability to acceptable levels, but cannot nullify it. To my understanding, relevant safety and fire fighting studies submitted to authorities are scrutinized only in case of an accident. If relevant inspector / investigator is convinced that every aspect had been adequate from safety viewpoint, we are clear. So we had better be reasonably conservative during design, after knowing the specific points in detail. Which means for mentioned spheres that fire case (and FPSVs on them) should be considered as a rule. If excluded, a "convincing" justification is needed.
Note *: I have seen now that fire engineering does no longer present "Fire Engineering Topics" in their link, apparently modified just now. However mentioned diagram of propane pool diameter - distance can be found in API 2510 A.
Edited by kkala, 03 April 2012 - 11:59 AM.
#21
Posted 03 April 2012 - 09:37 PM
Has anyone found said video. I've found a picture:
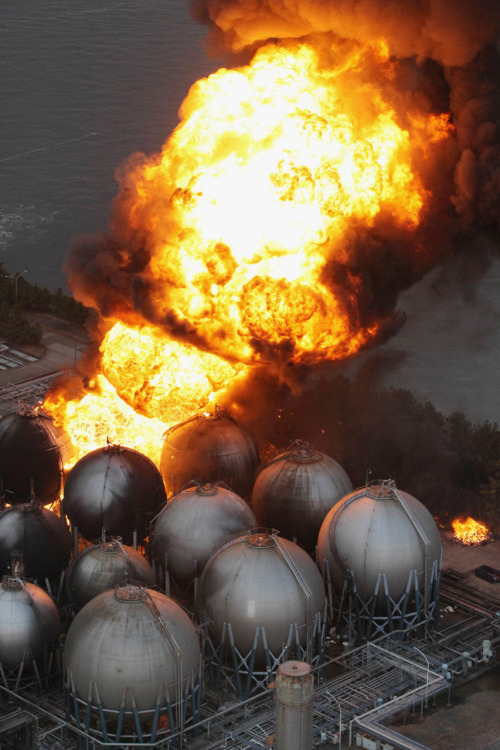
The picture gives a pretty clear indication that the API 25 ft rule doesn't apply in the LPG sphere scenario...
And an abstract of a paper on the damage that indicates 3-5 spheres BLEVE'd.
Edited by Technical Bard, 03 April 2012 - 09:43 PM.
#22
Posted 03 April 2012 - 10:40 PM
#23
Posted 09 April 2012 - 08:01 AM
A thread on reliability of heat load equations (hence their assumptions too) can be seen in http://www.cheresou...-load-equation , especially post No 3 by pleckner.
Note * : "Pocket Guide to Chemical Engineering" by C R Branan, Gulf 1999, Safety Relief Valve Design, Fire, p. 30.
2. Picture of sphere BLEVE is impressive. I understand that all presented spheres were damaged but only 3-5 of them had undergone BLEVE. A member with field experience can advise whether external downward pipes from each sphere represent PSV discharges to flare, and why no external water cooling is observed (insulated spheres?). Distance between spheres is short, compared to Aspropirgos Refinery (layout in first link of post No 20 by kkala). Local seismicity should induce additional measures in heavy storage of hazardous liquids (similar case in http://www.cheresou...a-storage-tank , post No 6).
3. Having at last access to API 2510 A (but not to API standard 2510), following preliminary opinions of installing a pair of LPG spheres in Greece, of 14 m diameter each (net capacity ~2x1200 m3), could be indicative as an example. Values in parenthesis from now on refer to the relevant paras of API 2510 (2nd ed, Dec 1996).
α. "There may be value in spacing greater than 10 ft for vessels larger than 10 ft in diameter, since larger vessels tend to stand higher and would have greater surface area exposed to potential flame impingement from a spill fire in the drainage path" (2.3.2.2). On the other hand local legislation (21 Dec 1990) suggests minimum spacing equal to 0.75*14 = 10.5 m, which is selected as more conservative.
β. Instructions are given for impoundment area, including distance (2.4); also for liquid capacity (2.4.5), but given in API 2510. Local legislation (21 Dec 1990) is less specific, with no conflict found. So API 2510 A / 2510 should be followed on drainage and Spill Containement.
4. "Requirements and recommended practices for relief systems on LPG equipment are discussed in 5.1.6, 6.6.3, 6.6.4, and A.1.5 in API standard 2510. In considering sizing of pressure relief protection for LPG storage vessels, the two most important contingencies are fire and overfilling. The potential for each of these contingencies should be evaluated, and the relief valve should be sized for the larger of the two relief flow requirements". (2.10.1.2, 2.10.1.3).
References of PSVs on LPG spheres not designed for fire contingency (FPSVs) were requested in post No 20 by kkala. Such examples would help understanding cases of non credible fire risk (probably rare). It seems that there are LPG vessels without cooling water protection (6.6.6.1).
However "If there is no flame contact on the shells of the adjacent vessel and the relief valves have not lifted, .... cooling can be delayed or not applied at all. When the relief valves lift, the need for cooling water must be assessed" (6.4.3).
5. Below are points of API 2510 A, probably of interest for the specific topic (but read more from the practice to get the meaning).
5.1 "Alternate designs are acceptable provided equal safety can be demonstrated" (1.1.1).
5.2. "The most serious LPG release is a massive failure of a storage vessel. Such failures are rare" (1.4.1)
A more likely LPG incident, and in the context of this publication a more relevant one, is leakage from piping or other components attached to or near the vessel followed by ignition, a flash fire or vapor cloud explosion, and a continuing pool fire and pressure (torch) fire" (1.4.3).
5.3 Liquified petroleum gas storage vessels should preferably be designed for full vacuum" (2.6.4).
5.4. Heat-activated valves (2.7.1.2) concern the isolation valve mentioned in post No 9 by kkala.
5.5 Atmospheric Relief systems: "A release will not create wide area flammable clouds at grade as long as the exit velocity of the vapor is 100 feet per second or more and there is no liquid carryover into the discharge. Also, should the release be ignited in a fire, the burning plume will not impinge on any other equipment to cause localized failure. The radiant heat to the vessel may be sufficient to raise the metal temperatures to dangerous levels; therefore, application of water to the top of the vessel may be advisable for prolonged releases that have ignited" (2.10.2.2).
"The vertical stack from the valve should be supported independently of the valve" (2.10.2.4).
5.6 "The key to overall safety in any phase of petroleum operations, including pressure storage, is knowledgeable, well-trained operators. Some industry statistics have shown that about 66 percent of all fires are the result of failure to follow proper operating procedures" (3.1.1).
5.7 "..firewater may not be needed for remote facilities, assuming that loss of the facility is an acceptable risk.
Remote-located facilities are those that have few exposure risks within 4000 feet. ..." (5.1.2, 5.1.3).
5.8 "There are three primary methods that may be used to apply water LPG storage vessels exposed to fires: water deluge, fixed monitors, and water spray. In addition, portable equipment may be used but should not be considered a primary method of water application".
Edited by kkala, 09 April 2012 - 08:05 AM.
#24
Posted 13 April 2012 - 01:58 PM
#25
Posted 13 April 2012 - 02:25 PM
Even an external vapor cloud explosion at some distance would be enough to destroy the vessel due to the shock waves it will create and no fire PSV is going to help protect the vessel.
Predicting intensity of fires and explosions is at best an exercise in trying to console ourselves that we provided a protection device to protect the vessel.
To know more about the devastation and unpredictable nature of fires and explosions refer the attachment provided.
Regards,
Ankur.
Attached Files
Similar Topics
![]() Psv Fire Case Relief Load CalculationStarted by Guest_mahmooddalvi09_* , 21 Feb 2024 |
|
![]() |
||
How To Choose Whether It Is Open Bonnet Or Closed Bonnet In Relief ValStarted by Guest_Radha Krishnan Siva Kumar_* , 02 Jan 2024 |
|
![]() |
||
![]() ![]() Multiple Psvs Relief RateStarted by Guest_fmalik_* , 02 Dec 2023 |
|
![]() |
||
![]() Pressure Control Valve Relief To Flare Upstream Block ValveStarted by Guest_Glauco_Tirollo_* , 07 Dec 2023 |
|
![]() |
||
Psv Relief Scenario (Steam)Started by Guest_panagiotis_* , 01 Jul 2023 |
|
![]() |