In the modern process technology era, employing professional and specialized engineering software has become a standard practice for equipment performance evaluation, both in design and optimization/troubleshooting/revamping stages.
The price of process simulator software (KBC Petro-SIM, Aspen RefSYS, amongst others) is very high - and it needs to be justifed through improved refinery economics: Planning/Supply chain optimization, Operations performance (product distribution and quality improvement), as well as Blending philosophy enhancement.
As a part of refinery Operations personnel, my coleagues and myself had an opportunity to work with KBC and Aspen software products. Through comprehensive process plants test-runs, modeling and simulation, we were in position to explore and evaluate a wide spectra of different operating possibilities: cut-point (separation level) improvement, process flow scheme modifications, process unit debottlenecking, refinery wide modeling etc. - which all affect the overall refinery economics significantly. Implementation of these conclusions (when every step of optimization program is done properly) resulted in increased refinery profit, enhanced flexibility/productivity of process units and equipment utilization.
I have never tried, though, to calculate the exact benefit ($) of using simulator tools, and time that is needed for complete software investment return. It is beyond my scope of work at the moment, and far beyond the level of my engineering knowledge.
So, my questions to refinery people are:
- What are your personal experiences with process simulator tools?
- Who is the person (or persons) responsible for process modeling and simulation? Do you have a special Process Department team, or it is a group of people, originating from Operations, Maintenance, Laboratory, R&D, Process Department?
- How do you calculate software investment return, based on your company actual operation?
I am attaching one interesting document, related to Crude Unit modeling. It is also available at: http://www.kbcat.com...h/world_ref.pdf
I hope that interesting discussion from experienced professionals will follow these questions and conclusions.
Best regards.
[attachment=350:Modeling...ude_Unit.pdf]
|
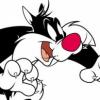
Refinery Wide Simulation
Started by Zauberberg, Dec 26 2006 07:40 AM
4 replies to this topic
Share this topic:
#1
Posted 26 December 2006 - 07:40 AM
#2
Posted 26 December 2006 - 07:45 PM
hi zauberberg,
You have raised very important topic as before. I work in engineering group of EPC company. I have had chance to interact formally as well as casually with refinery personnel on several occasions. Based on my experience, I have observed that the simulation study in an operating refinery in order to optimize, to bottleneck or to troubleshoot had been in the scope of "technical service" department of the refinery. BUT in close co-operation with R&D and operation personnel as required.
There had been dedicated engineers in such department to perform several tasks including but not limited to decide target throughputs of various units based on market demand, to do linear programming, to support operation engineers in troubleshooting, to analyze & report overall refinery operations on regular basis and to take part in new project implementations or revamp studies.
I don't think there can be direct evaluation of hysis or other simulation software against how much savings ($) it can give. Because such software are costly but not to the extent that it would need 'independent' evaluation !!! Further, you don't use this software only for optimization once you have purchased it. You can use for troubleshooting, to compare actual data vis-a-vis design data etc. Basically, there should be annual budget for all kind of technical services including outsourcing and internal expenses. One has to really foresee the need of software in present as well as future scenario and then propose to management to purchase the software. You can dedcide after specific time of purchase whether the software was utilized effectively or not. Quantitative aspect on saving could be one of the several aspects of its usage. But definitely not the only one.
I hope you will get others opinion too.
Thank you,
You have raised very important topic as before. I work in engineering group of EPC company. I have had chance to interact formally as well as casually with refinery personnel on several occasions. Based on my experience, I have observed that the simulation study in an operating refinery in order to optimize, to bottleneck or to troubleshoot had been in the scope of "technical service" department of the refinery. BUT in close co-operation with R&D and operation personnel as required.
There had been dedicated engineers in such department to perform several tasks including but not limited to decide target throughputs of various units based on market demand, to do linear programming, to support operation engineers in troubleshooting, to analyze & report overall refinery operations on regular basis and to take part in new project implementations or revamp studies.
I don't think there can be direct evaluation of hysis or other simulation software against how much savings ($) it can give. Because such software are costly but not to the extent that it would need 'independent' evaluation !!! Further, you don't use this software only for optimization once you have purchased it. You can use for troubleshooting, to compare actual data vis-a-vis design data etc. Basically, there should be annual budget for all kind of technical services including outsourcing and internal expenses. One has to really foresee the need of software in present as well as future scenario and then propose to management to purchase the software. You can dedcide after specific time of purchase whether the software was utilized effectively or not. Quantitative aspect on saving could be one of the several aspects of its usage. But definitely not the only one.
I hope you will get others opinion too.
Thank you,
#3
Posted 02 January 2007 - 05:05 AM
Dear All,
One of the problems that exist with typical simulators like HYSYS and Aspen+ is that because we define refinery feeds as assay and pseudo components,we can not define reaction sets and so we can not simulate refinery reactors like catalytic hydrogenation and etc.I have heard that in new softwares like PETRO-SIM or HYSYS-REFINERY the designers have solved this problem.Who knows about it?
Thanks in advance.
Best of Luck.
One of the problems that exist with typical simulators like HYSYS and Aspen+ is that because we define refinery feeds as assay and pseudo components,we can not define reaction sets and so we can not simulate refinery reactors like catalytic hydrogenation and etc.I have heard that in new softwares like PETRO-SIM or HYSYS-REFINERY the designers have solved this problem.Who knows about it?
Thanks in advance.
Best of Luck.
#4
Posted 06 January 2007 - 11:52 AM
Petro-SIM and RefSYS are available with built-in moduls of refinery reactors: FCC, Reformer, DHT etc. The main catch is unit model calibration, which means that observed reactor system performance is incorporated into your (refinery) process flowsheet. So, every refinery/process unit should be calibrated separately, and it depends on system characteristics and actual reactor performance. From what I have seen, this is very tough and time-consuming job, and it should be done by software vendor experts. It can be (and it should be!) a part of software license agreement.
Do not try to model complex chemical reactions of your reacting system by yourself. There is a very big chance to do it incorrectly. This particularly applies for industrial-scale systems, such are refineries and petrochemical units.
Do not try to model complex chemical reactions of your reacting system by yourself. There is a very big chance to do it incorrectly. This particularly applies for industrial-scale systems, such are refineries and petrochemical units.
#5
Posted 13 February 2007 - 12:50 PM
QUOTE (Nirav @ Dec 27 2006, 12:45 AM) <{POST_SNAPBACK}>
I don't think there can be direct evaluation of hysis or other simulation software against how much savings ($) it can give.
I have heard of a company in Surrey (England) that offers it's modelling/simulation/engineering services to refineries for a "percentage of the savings" basis. That is to say, they check out the process, propose some changes to the plant, and when all is said and done, they pick up a percentage of the money being saved by the plant as a result of their work...
Goodness knows how you can separate the money saved by them, and the money being saved/lost by other changes within the plant.
Similar Topics
Aspen Hysys Simulation Of Acid Gas Removal UnitStarted by Guest_R.t_* , 22 May 2025 |
|
![]() |
||
Refinery Lpg Deethanizer Column DesignStarted by Guest_Ilyes_* , 15 Feb 2025 |
|
![]() |
||
Dynamic Simulation - SeparatorsStarted by Guest_tomr91_* , 10 Mar 2025 |
|
![]() |
||
![]() Dynamic Simulation After Feed Flow ReductionStarted by Guest_Kakashi-01_* , 20 Mar 2025 |
|
![]() |
||
Converting A Static Simulation To Dynamic SimulationStarted by Guest_tomr91_* , 26 Feb 2025 |
|
![]() |