|
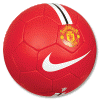
#26
Posted 19 October 2011 - 07:08 AM
#27
Posted 19 October 2011 - 10:03 AM
I have already said
Please refer to the quote from a thermodynamics textbook in Post no. 19.Furthermore, k (the isentropic exponent) is not equal to Cp/Cv for a real gas or vapour.
What I am trying to communicate is that for propane vapour, while Cp/Cv is greater than 1 (see Ankur's results which I agree with), the isentropic exponent k is less than 1.
Paul
#28
Posted 19 October 2011 - 12:24 PM
#29
Posted 06 June 2012 - 08:42 AM
i need an advice regading the relieving temperature of the pressure safety valve.
does anyone know how can i calculate (by hand) or estimate this temperature.
thank you very much!
have a nice day!
#30
Posted 06 June 2012 - 10:36 PM
Relieving temperature is calculated based on the relief scenario and also affected by relieving fluid state, then you should specify these matters and relevant information to be able to calculate.
Fallah
#31
Posted 31 July 2012 - 12:11 PM
I need some advice on the PSV size calculated for gaseous service.
In my case my PSV is to be sized for two operating fluids (not simultaneously) but the unit has been designed for two feeds.
The applicable case for the PSV is fire vase. For one of the fluids the relieving flowrate is coming to be 9500 kg/hr (for fluid 1: To be used only during start up) and for the other fluid the relieving flowrate is aroun 2700 kg/hr (for fluid 2: Normal operating fluid).
If i go with the Cp/Cv values mentioned in the API then my orifice size is coming to be F. while if i use the real gas Cp/Cv values calculated by HYSYS, my orifice size is coming to be E which is already a conservative value since my unit will work only with fluid 2 as the relieving flowrate of 9500 kg/hr has been used for PSV calculation.
Can anyone suggest me that should i go for the ideal Cp/Cv values mentioned in the API or should i consider the value as calculated by HYSYS as my PSV size of E will be suitable for start up fluid also.
Pl. suggest.
Regards
Pallavi
#32
Posted 01 August 2012 - 10:17 AM
Of course if you utilize a different method but then select a conservative size there are no problems but it's difficult to see any advantage in that way to proceed...
There are alternatives, you can for example solve the nozzle mass flux equation with multiple isentropic flashes, see this thread
http://www.cheresour...diabatic-flash/
Edited by PaoloPemi, 01 August 2012 - 10:59 AM.
#33
Posted 07 August 2012 - 09:50 PM
Thanks very much for your help.
Ray
#34
Posted 10 August 2012 - 10:52 AM
http://www.prode.com/docs/pppman.pdf
which exports Excel macros to solve isentropic, adiabatic etc.multi phase flash operations.
API 520 gives different procedures but the method is not complex, for wide boling mixtures given a reliving temperature you calculate the saturation pressure then solve an adiabatic flash , calculate the Leung omega factor, the critical pressure ratio, vapor and liquid density,
I got a Excel page from Prode but most simulators have these procedures coded and can export the results in Excel .
Edited by PaoloPemi, 10 August 2012 - 11:43 AM.
#35
Posted 15 August 2012 - 12:54 AM
#36
Posted 24 August 2012 - 03:59 AM
the Omega method as described in my API 520 2006 D2.2 is very simple to implement in Excel,
you need to calculate the Omega parameter (equation D 10)
w = 9*(V9/V0 - 1)
where
V9 is the specific volume at 90% of PRV inlet pressure (determined by isentropic flash)
V0 is the specific volume at PRV inlet pressure
in my case I utilize Prode Properties which exports in Excel the macro StrV which calculates the specific volume and SPF which solves the isentropic flash at specified pressure, with Prode Properties you can
-calculate the specific volume V0 with StrV at PRV inlet pressure
-calculate the temperature T9 at 90% of PRV inlet pressure with SPF
-calculate the specific volume V9 with StrV at T9, P9 (90% of PRV inlet pressure)
once you have determined the Omega parameter you verify if flow is critical or subcritical, calculate the mass flux (step 3) and the required area (step 4),
the information in API 520 is very detailed, you shouldn't find problems.
My suggestion is to calculate the Omega parameter at two values (for example 70% and 90% of PRV inlet pressure) , this permits to verify the applicability of the model, if the values are very different better to utilize a more sophisticated method,
by the way you can easily include these tests in Excel while the generic procedures available in process simulators or commercial software do not allow this kind of flexibility...
Edited by PaoloPemi, 24 August 2012 - 04:01 AM.
#37
Posted 31 August 2012 - 09:08 AM
I attach the file nozzle.xls which solves the isetntropic nozzle model,
please note that it requires Prode Properties, if you are a student a free copy is available at
http://www.prode.com
best regards
Paolo
Attached Files
#38
Posted 02 September 2012 - 02:29 AM
I am evaluating the results of the isetntropic nozzle model in Prode,
I see that discharging temperature is calculated in two steps (isentropic to stagnation pressure and adiabatic to outlet pressure),
Aspen Flarenet adopts a simillar method,
do you know if this method has been discussed in API standards (or different standards and codes)
#39
Posted 03 September 2012 - 02:16 AM
#40
Posted 24 October 2012 - 05:06 AM
i have one query related to tube rupture PSV. I have a distillation column and a reboiler. my reboiler has steam on shell side with a design pressure of 20 barg and the hydrocarbon in the tubes with a design pressure of 15.5 barg while the column is designed for a pressure of 7.1 barg. my question is though the LPS of my reboiler is designed for 10/13th rule, do i have to provide a psv for tube rupture case since my column is not designed for that pressure or my column PSV is to be designed for relieving the excessive pressure during tube rupture?
Regards
Pallavi
#41
Posted 25 October 2012 - 12:10 AM
At first 10/13 rule in new edition of API 521 is replaced by:" If corrected hydrotest pressure of low pressure side would be higher than design pressure of high pressure side there is no need to PSV for protection against overpressure due to tube rupture..."
In your case the operating/relieving temperature are not mentioned for hydrotest pressure correction; but because: 1.3*15.5>20 seems there is no need to PSV for tube rupture in reboiler itself.
Now about the system including reboiler and the column: Normally the column is connected to the shell side of the reboiler mostly without any isolation valve inbetween hence design pressures of column and reboiler's shell side are to be set equal and would be protected by one PSV; while you mentioned the column is connected to tube side with considerable difference in design pressure. Please check this matter and send back to discussion with the result of checking and also specify the type of the reboiler.
Fallah
#42
Posted 31 October 2012 - 11:32 AM
In our case the difference between the design pressures of the column and the reboiler was overlooked but at a later stage we noticed that there is considerable difference between both the design pressures and PSV is required.
My main concern was that do i have to provide a separate PSV near the reboiler for tube rupture case or the PSV on the column is sufficient to relieve that excess pressure since there is no isolation valve between the reboiler and column.
Regards Pallavi
#43
Posted 01 November 2012 - 12:38 AM
In fact, as i mentioned in your case there is no need to a PSV for protection of low pressure side of the reboiler, i.e. tube side, against tube rupture and the PSV on the column can cover the tube rupture case as an "applicable scenario" of overpressure among other scenarios for the protection of the column itself instead tube side.
Fallah
Similar Topics
![]() Liquid Liquid Separator SizingStarted by Guest_Kentucky08_* , 03 Apr 2025 |
|
![]() |
||
![]() ![]() Nozzle Sizing CalculationStarted by Guest_BabRafiq1_* , 26 Aug 2022 |
|
![]() |
||
![]() Guidance On Sizing Jacketed Pipe For Glycerine CoolingStarted by Guest_Kentucky08_* , 28 Jun 2025 |
|
![]() |
||
![]() Separator Sizing Step By Step ProcedureStarted by Guest_krishnamurthy_* , 06 Apr 2023 |
|
![]() |
||
Critical Pressure For Choke Valve SizingStarted by Guest_Sherif Morsi_* , 07 Nov 2017 |
|
![]() |